Ever found yourself racing against the clock to meet production deadlines? Or maybe you've had to deal with the frustration of running out of stock at the worst possible moment? How about overstocking and tying up cash in inventory you don’t need? If any of these sound familiar, you’re not alone.
Managing production schedules and inventory isn’t just a daily task—it’s a constant balancing act. So, how do you make sure things run smoothly without these headaches? That’s where Materials Requirement Planning (MRP) comes in.
Curious how MRP can help streamline your processes and save you time and money? Let’s dive in and see how it can make a real difference for your business. Before diving into the specifics, let’s get on the same page about what MRP is and why it’s essential.
Overview of Material Requirements Planning (MRP)
Material Requirements Planning (MRP) is a system manufacturers use to ensure that materials and products are available for production and delivery while keeping inventory levels as low as possible. At its core, MRP helps streamline production processes by aligning raw materials, production schedules, and demand forecasts.
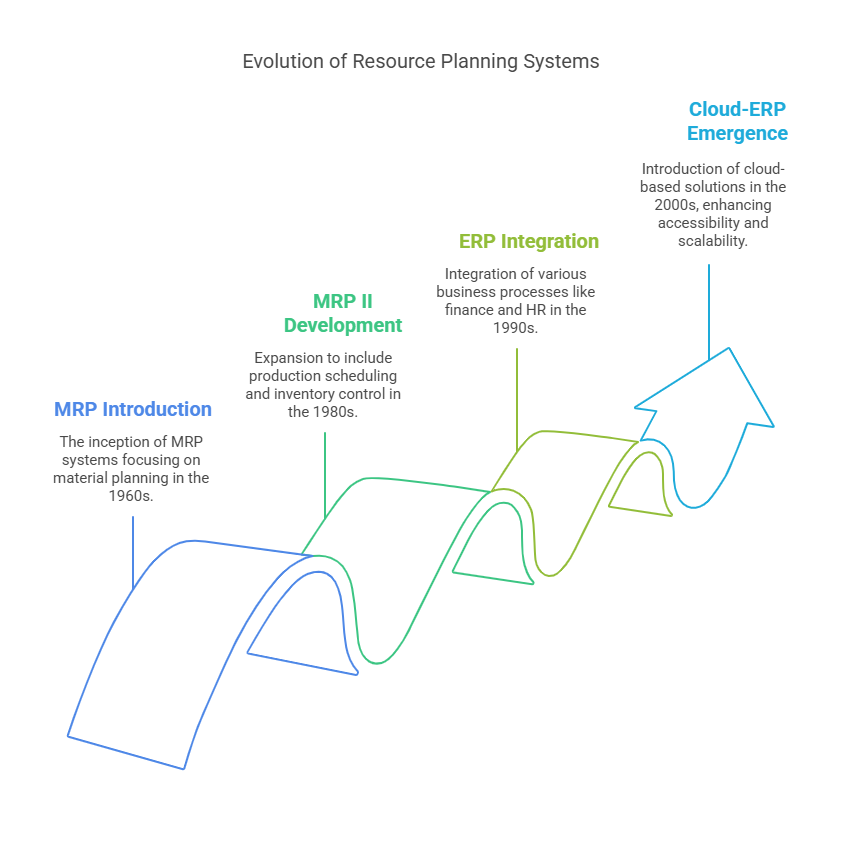
Let’s consider a simple scenario: Imagine a company that manufactures custom furniture. They need to ensure they have enough wood, screws, paint, and other materials to meet customer orders. Without MRP, the company might have too much inventory, leading to wasted space and higher costs, or too little, causing delays in fulfilling customer orders.
MRP solves this problem by tracking the materials needed for each production step and ensuring they’re ordered and delivered just in time. The system factors in the sales forecasts, current inventory, and production lead times to calculate exactly what needs to be purchased and when. This minimizes excess stock, reduces waste, and ensures that production can continue without delays.
In essence, MRP integrates various business processes like inventory management, production scheduling, and procurement, ensuring everything operates in sync. It’s the backbone that helps businesses meet demand while managing their resources efficiently.
Now that we understand what MRP does, let’s break down its key objectives and how it benefits your operations.
Also Read: How to Increase Overall Production Line Efficiency?
Objectives of MRP
Material Requirements Planning (MRP) is a system that helps manufacturers efficiently manage their materials and production schedules. The core objectives of MRP are to ensure raw material availability, keep inventory at optimal levels, and synchronize manufacturing, delivery, and procurement processes. Let’s explore further.
Ensuring Availability of Raw Materials for Production
One of MRP’s primary goals is to prevent production delays due to material shortages. For example, consider a company that manufactures custom machinery parts. Without an MRP system, material shortages can halt production unexpectedly.
MRP calculates the necessary materials for each production step and ensures timely ordering, so components arrive as needed, preventing costly downtime and speeding up the production process.
Maintaining Low Inventory Levels
Another essential objective of MRP is to help businesses avoid overstocking while ensuring that they meet customer demand. Excess inventory ties up valuable resources and increases storage costs. MRP forecasts material needs, enabling companies to order materials just in time for production.
For example, a clothing manufacturer uses MRP to purchase just enough fabric to meet order requirements, avoiding unnecessary stockpiling and reducing storage costs.
Coordinating Manufacturing, Delivery, and Purchasing Schedules
MRP’s ability to synchronize schedules across various departments—procurement, manufacturing, and delivery—ensures that materials and products are available when needed.
For instance, an automotive parts manufacturer uses MRP to align part deliveries with assembly line schedules, ensuring a continuous workflow without bottlenecks. By aligning schedules, MRP minimizes delays and ensures production stays on track.
Minimized Customer Lead Time: Faster Order Fulfillment
Want to reduce the time it takes to fulfill customer orders? MRP systems help businesses achieve shorter customer lead times, giving you a competitive edge. By accurately planning material availability and aligning production processes, MRP enables you to cut down the time from order to delivery. This efficiency, driven by better resource management and proactive material procurement, boosts customer satisfaction and strengthens your market position.
Enhanced Production Efficiency: Streamlined Operations
MRP doesn’t just prevent delays—it actively boosts production efficiency. With a clear view of material needs and production schedules, MRP minimizes idle time, reduces excess work-in-progress inventory, and optimizes the flow of goods through manufacturing. The result? Higher output with fewer resources, allowing your operations to run more smoothly and effectively.
Achieved Cost Optimization: Reduced Waste and Expenses
Beyond just lowering inventory costs, MRP drives broader cost savings. Efficient material planning reduces obsolete or spoiled inventory waste, while synchronized schedules lessen the need for costly rush orders. Plus, by improving resource utilization, MRP helps reduce overall operational expenses, ultimately increasing profitability.
Guaranteed Customer Satisfaction: Reliable Product Delivery
MRP's ability to ensure material availability, optimize production processes, and minimize lead times directly impacts customer satisfaction. With MRP, businesses can consistently meet delivery commitments and maintain reliable product availability. This reliability builds trust, leading to stronger long-term customer relationships.
Maximized Resource Allocation: Optimal Utilization
MRP helps businesses make the most of their available resources—not just materials but also labor, equipment, and capital. By providing a comprehensive view of production needs and timelines, MRP helps businesses plan and allocate resources more efficiently, ensuring everything is utilized where and when it’s needed, maximizing productivity across the board.
Strengthened Decision-Making: Data-Driven Insights
One of the often-overlooked benefits of MRP is the valuable data it generates. MRP offers key insights into material usage, production bottlenecks, and supply chain issues. With accurate and timely data, managers can make informed decisions about purchasing, production planning, and inventory control, leading to more responsive and agile operations.
With clear objectives in mind, let’s explore the key concepts that make MRP systems tick in practice.
Key Concepts in MRP
To fully understand how MRP works, it’s essential to grasp the core concepts that drive the system’s efficiency. These concepts include the distinctions between dependent and independent demand, the role of the Bill of Materials (BOM), and how MRP systems centralize inventory control and production scheduling. Let’s learn more about them below.
- Understanding Dependent vs. Independent Demand
MRP systems differentiate between dependent and independent demand to accurately calculate material needs. Dependent demand refers to materials required to produce finished goods, such as parts for assembling a car. Independent demand, on the other hand, relates to the demand for the finished product itself, such as customer orders for cars.
Recognizing these distinctions ensures that MRP can accurately predict what materials need to be ordered and when, reducing the risk of overproduction or material shortages.
- Role of Bill of Materials (BOM) in MRP
The Bill of Materials (BOM) is a detailed list of all materials and components required to make a product. It serves as the foundation for MRP by outlining the exact quantities needed for each part of the production process.
For example, if a company manufactures a television, the BOM will include everything from the screen to the screws. With this data, MRP can calculate the precise material requirements, ensuring that no part is overlooked and that the production process runs smoothly.
- Functions of MRP Systems Including Inventory Control and Scheduling
MRP systems combine inventory management and production scheduling to ensure materials are available when required. The system tracks inventory in real-time, adjusts orders based on material usage, and automates production scheduling to ensure a seamless flow. This centralized control improves efficiency by reducing human error and manual intervention.
For instance, an electronics manufacturer uses MRP to track components like chips and screens, ensuring they’re ordered and delivered on time to avoid production delays.
- Supply Chain Optimization (Balancing Supply and Demand)
An often understated benefit of MRP is the wealth of data it generates. This data provides valuable insights into material usage, production bottlenecks, and potential supply chain issues. By providing accurate and timely information, MRP empowers managers to make informed decisions regarding purchasing, production planning, and inventory control, leading to more agile and responsive operations.
While MRP offers powerful tools, no system is without its challenges. Let’s weigh the pros and cons.
Advantages and Disadvantages of MRP
Material Requirements Planning (MRP) offers significant benefits to manufacturers, but like any system, it has its drawbacks. Here’s a deeper look at the key advantages and disadvantages of using MRP.
.png)
Advantages of MRP
- Improved Inventory Management: MRP ensures that businesses maintain the right inventory levels—neither too high nor too low—by accurately forecasting material needs. For instance, a car manufacturer can use MRP to track parts, ensuring that only what’s needed is ordered. This prevents overstocking, minimizes waste, and reduces storage costs.
- Optimized Production Schedules: One of MRP's most valuable advantages is its ability to schedule production based on material availability and customer demand. For example, a kitchen appliance manufacturer can use MRP to ensure all parts are available and production is synchronized. This avoids production delays caused by missing materials and keeps operations running smoothly.
- Cost Reduction: By preventing overstocking and reducing manual labor, MRP helps businesses lower their overall costs. With precise material planning, companies avoid spending money on unnecessary stock. For instance, a clothing manufacturer can keep production costs in check by only purchasing fabric as needed, ensuring capital is not tied up in excess inventory.
Disadvantages of MRP
- Reliance on Accurate Data: MRP’s effectiveness hinges on the accuracy of its data. Any errors in inventory levels or demand forecasts can lead to costly mistakes. For instance, if a company’s sales forecast is off, MRP might either order too much material or fall short, causing production delays or excess stock.
- Initial Setup Costs: Implementing an MRP system often involves substantial upfront investment in software, training, and system integration. For small businesses, the costs of these initial setups may pose a barrier. However, long-term savings can justify the investment for companies with large-scale operations.
- Complex Implementation: Transitioning from traditional methods to MRP can be challenging, particularly for businesses with entrenched manual processes. The system requires careful planning and training to integrate effectively with existing operations. Resistance to change is common, which can sometimes slow adoption.
As the landscape changes, MRP is evolving. Enter Demand-Driven MRP, a smarter approach to material management.
Evolution to Demand-Driven MRP (DDMRP)
Traditional MRP systems rely on forecasts and push inventory through the supply chain based on predictions about customer demand. However, this can lead to inefficiencies when actual demand deviates from forecasts.
Demand-driven MRP solves this issue by using real-time demand signals to adjust production and material requirements dynamically. It enables businesses to respond quickly to market shifts, ensuring production is always aligned with current needs.
.png)
For example, a company producing consumer electronics might use DDMRP to adjust its production schedule based on actual customer orders instead of forecasted demand. This flexibility allows the company to avoid overproduction or stockouts.
Benefits of Demand-Driven MRP
- Greater Flexibility: DDMRP enables companies to adapt to changes in demand quickly. By responding to real-time data rather than relying on forecasts, manufacturers can better align their production with actual customer needs. This is particularly useful in industries with frequent demand fluctuations, such as fashion or electronics.
- Improved Supply Chain Visibility: By continuously monitoring real-time demand signals, DDMRP enhances supply chain visibility. This allows businesses to quickly identify potential bottlenecks, optimize material flows, and improve supplier relationships. For example, an automobile manufacturer can use DDMRP to track parts and materials, ensuring timely deliveries and smoother production runs.
- Faster Lead Times: With DDMRP, businesses can reduce lead times by strategically positioning inventory and focusing on critical materials. This system anticipates shortages and triggers replenishment before stock levels become critical, allowing for faster order fulfillment. A company that manufactures medical devices, for example, can use DDMRP to ensure vital components are always available when needed, reducing the time required to restock.
The Shift to Strategic Inventory Positioning
DDMRP emphasizes strategic inventory positioning, which ensures that essential materials are stocked at key points throughout the supply chain. This approach moves away from traditional methods of holding excessive inventory and instead positions materials at critical locations where they are most likely to be needed. By doing so, businesses can minimize storage costs and avoid the risk of stockouts, while still being prepared for fluctuations in demand.
So, when should you take the leap to MRP? Let’s look at the signs it’s time to upgrade your system.
Recognizing the Need for MRP Systems
Running a manufacturing business is no small feat. Between managing inventory, meeting customer deadlines, and ensuring production stays on track, the pressure can quickly pile up. If you’re facing challenges like delayed shipments, wasted resources, or constantly running out of stock, it might be time to consider an MRP system.
Let’s take a closer look at some key signs that tell you it’s time to make the shift.
- Complexity in Production Operations
Does managing your production feel like a juggling act? If you’re coordinating multiple processes—such as inventory control, purchasing, and scheduling—all manually, it can get overwhelming.
As your business grows, it becomes harder to keep track of everything. If you're noticing that small mistakes are leading to bigger delays or inefficiencies, MRP could be the solution to simplify these processes. MRP integrates all these tasks into one system, making it easier to coordinate and track everything from start to finish.
- Handling Increased Customer Demand
Are you seeing a rise in customer demand, but struggling to meet those expectations? Perhaps orders are coming in faster than you can keep up with, or there’s confusion about inventory levels. MRP helps you stay on top of customer demands by aligning materials and production schedules. It ensures that you have just the right materials at the right time, preventing delays and helping you deliver on time—every time.
- Transitioning from Manual to Automated Inventory Management
If you’re still managing inventory manually with spreadsheets or basic tracking methods, you’re probably running into inefficiencies. Manual processes can lead to errors like missing stock, double orders, or slow responses to production changes.
Switching to an MRP system can automate inventory management, ensuring that orders are placed on time, stock levels are tracked in real-time, and materials are always available when you need them. This shift to automation can save you time, reduce human error, and improve your overall efficiency.
- Disconnection Between Teams
Do your procurement, manufacturing, and sales teams often seem out of sync? Communication breakdowns between these teams can cause major issues, such as missing deadlines, overordering materials, or understocking.
MRP systems connect these departments, ensuring that everyone is on the same page. By synchronizing production schedules with material requirements and order timelines, MRP fosters better coordination across all departments.
- Dealing with Overstock or Stockouts
Have you noticed that you’re either running out of stock too often or overstocking items that are not in demand? Both scenarios are costly. Overstocking ties up capital in unsold goods, while stockouts can cause missed sales and delays.
MRP systems help you maintain the perfect balance. By forecasting demand and scheduling material purchases precisely, MRP ensures that you neither overstock nor run out of critical items.
Once you recognize the need, managing your resources effectively becomes crucial—enter Capacity Requirements Planning.
Also Read: Strategies to Improve Work, Operational, and Production Efficiency
Capacity Requirements Planning (CRP)
Capacity Requirements Planning (CRP) is essential for manufacturers to ensure they have enough resources to meet production demands. While MRP manages material availability, CRP ensures that production resources like machines, labor, and equipment align with the material requirements.
For instance, if a company needs to produce 500 units of a product in a month, CRP helps determine whether the existing machinery and workforce can meet that demand. If there’s a mismatch, CRP can trigger adjustments such as adding shifts or temporarily hiring extra workers to ensure production goals are met.
.png)
Integrating CRP with MRP guarantees that the production process can continue smoothly without delays once materials are available. This coordination prevents bottlenecks that occur when production capacity doesn’t match material availability, ensuring on-time delivery and efficient operations.
Without CRP, there’s a risk that materials might arrive, but the production capacity won’t be sufficient to handle the demand. This leads to production delays, missed deadlines, and potential losses in business opportunities. CRP ensures that production meets demand by adjusting resources accordingly.
CRP is great, but integrating it with S&OP takes coordination to the next level, aligning sales with production.
Sales and Operations Planning (S&OP)
Sales and Operations Planning (S&OP) aligns sales forecasts with production and inventory strategies. The process integrates sales, production, and inventory management, ensuring that every department works toward the same goal—meeting customer demand efficiently.
.png)
By integrating MRP into S&OP, businesses can better plan for material needs in alignment with production schedules. For instance, a company might forecast higher demand for a product, but without MRP, the necessary materials might not be available. MRP ensures that production schedules are aligned with material availability, reducing the risk of stockouts and production delays.
S&OP helps businesses plan ahead by considering demand, inventory, and production capabilities. MRP plays a critical role by providing accurate material requirements, enabling better planning and smoother coordination across departments. This allows businesses to respond flexibly to changes in customer demand while keeping costs in check.
But why stop there? Lean manufacturing principles paired with MRP make the entire production flow more efficient, a retailer gearing up for seasonal demand can use MRP to ensure they have the right materials and production capacity in place, preventing delays and maximizing revenue.
Lean Manufacturing and MRP Integration
Lean manufacturing focuses on reducing waste, cutting costs, and improving production efficiency. When MRP is integrated with lean principles, the focus is on streamlining material flows and reducing inventory to only what's needed for production.
For example, a manufacturer can use MRP to order materials just in time for production instead of overstocking components. This minimizes excess inventory, storage costs, and waste. Lean practices reduce waste in inventory and throughout the production process, making operations smoother and more cost-effective.
MRP enhances lean manufacturing by improving forecasting accuracy and ensuring that materials are ordered based on actual demand, not speculation. Unlike traditional systems that lead to excess inventory, MRP helps maintain lean operations by synchronizing material procurement with production schedules.
In addition, combining MRP with tools like Kanban ensures that materials are replenished as needed, promoting a pull-based system where inventory is replenished based on actual consumption. This alignment with lean principles leads to greater efficiency, fewer wasteful practices, and faster production cycles.
Even with lean practices, variability can throw a wrench in the works. Let’s see how MRP handles these uncertainties.
The Impact of Variability
Variability in demand and lead times is an inevitable challenge in manufacturing, but managing it effectively is key to smooth operations. Here’s how variability affects businesses:
- Demand Fluctuations: Unpredictable customer demand can lead to either stockouts or overstocking. MRP helps adjust orders in real-time to match changing customer needs, ensuring sufficient materials are on hand when needed.
- Lead Time Variability: Supply chain disruptions can delay production. MRP incorporates safety lead time, adjusting order schedules to buffer against potential delays.
- Safety Stock: To prevent stockouts during demand spikes, MRP calculates the optimal amount of safety stock needed, maintaining an ideal balance between availability and waste reduction.
With variability in mind, supplier collaboration is key. A smooth supply chain can’t function without solid partnerships.
Supplier Collaboration
Collaboration with suppliers is essential for seamless production. MRP systems enhance this collaboration by sharing real-time material needs and schedules with suppliers. Here’s how:
- Real-Time Data Sharing: MRP connects manufacturers and suppliers by sharing data about material requirements and schedules. This allows suppliers to adjust their production and shipping plans to meet demand.
- Improved Lead Times: When suppliers are well-informed about upcoming orders, they can prioritize deliveries, reducing lead times and ensuring timely material availability.
- Efficient Coordination with IoT: IoT technologies integrated with MRP systems allow manufacturers and suppliers to track material status and shipments in real-time, optimizing the flow of materials and reducing delays.
.png)
Technology also plays a role—cloud-based MRP systems allow seamless collaboration, giving you access anytime, anywhere.
The Role of Cloud-Based MRP Systems
Cloud-based MRP systems have revolutionized how manufacturers manage their operations, offering flexibility, scalability, and real-time access. Key benefits include:
- Accessibility: Cloud-based systems allow teams to access data from any location, improving decision-making and coordination. Production managers can check inventory or schedules from anywhere, ensuring timely actions.
- Scalability: As businesses grow, cloud systems scale easily to accommodate new demands, whether adding more users or expanding production capacity.
- Cost-Effectiveness: Cloud MRP systems often require less upfront investment and no costly IT maintenance. Subscription-based pricing makes them affordable for both large and small manufacturers.
- Automatic Updates: Cloud systems automatically update with the latest features and security patches, keeping your system current without additional costs.
Tech is only as good as the people using it. Let’s discuss how to prepare your team for smooth adoption.
User Training and Change Management
Implementing a new MRP system requires effective training and change management to ensure successful adoption. Here’s how to make it work:
- Comprehensive Training: Provide in-depth training that covers all aspects of the MRP system, including inventory tracking, procurement, and reporting. Tailor training to each department’s needs.
- Clear Communication: Keep employees informed about the reasons behind the change and the benefits it will bring. This transparency helps reduce resistance and fosters support.
- Ongoing Support: After the system is implemented, provide continuous support through helpdesks, FAQs, and follow-up training to address any questions or challenges that arise.
- Feedback and Improvement: Use employee feedback to refine processes and ensure the system continues to meet evolving business needs.
Now that we’ve covered the essentials, let’s dive into how INSIA.ai can supercharge your MRP system for better results.
How INSIA.ai Can Help in Optimizing MRP Systems for Manufacturing Efficiency?
In the world of manufacturing, effective Material Requirements Planning (MRP) is essential for ensuring smooth operations. However, to get the most out of your MRP system, you need a way to integrate diverse data sources and streamline decision-making across various departments. That’s where INSIA comes in.
INSIA.ai offers a comprehensive data integration platform that centralizes all your data, helping to optimize the very processes MRP relies on. From inventory management to production scheduling, INSIA can seamlessly integrate data from different sources and provide real-time insights that empower MRP systems to function at their best.
Here’s how INSIA can work in conjunction with your MRP system to maximize manufacturing efficiency:
1. Centralizing Data for Accurate MRP Execution
MRP systems rely heavily on data—inventory levels, production schedules, material forecasts, and lead times. With INSIA, you can centralize all this data from disparate sources into one unified platform. This centralization ensures that your MRP system has access to accurate, up-to-date information, reducing errors that stem from fragmented data.
- Seamless Integration: INSIA connects with over 30 different data sources, including ERP systems, CRMs, and other databases, ensuring that all relevant material, procurement, and production data is available in one place.
- Accurate Forecasting: By feeding INSIA’s predictive analytics into your MRP system, you can refine your material forecasts and anticipate demand shifts more effectively, ensuring that your MRP system is always aligned with real-world conditions.
2. Real-Time Data for Better Decision-Making
One of the most significant challenges in manufacturing is responding to changes in real-time. Whether it’s a sudden demand spike, a supply chain disruption, or production delays, having timely insights is crucial to keeping operations on track. INSIA’s Push AI feature ensures that you receive relevant insights when they’re needed, allowing you to make immediate adjustments to your MRP system and prevent disruptions.
- Automated Reporting: Receive real-time, automated updates on inventory, material availability, and production progress, helping you adjust MRP parameters instantly.
- Predictive Analytics: With INSIA, you can predict when certain materials might run low, or when you might experience a bottleneck in production, and proactively adjust your MRP settings.
3. Improved Inventory Management
A key objective of MRP is to maintain optimal inventory levels—too much inventory ties up capital, while too little causes production delays. INSIA helps you keep your inventory in check by providing real-time data on stock levels and demand fluctuations, which can be integrated with your MRP system to avoid overstocking or understocking.
- Inventory Visibility: INSIA tracks inventory levels and integrates this information with your MRP, allowing you to forecast material needs more accurately.
- Cost Reduction: By automating inventory management and reducing excess stock, INSIA helps minimize waste and lowers storage costs, aligning perfectly with MRP’s goal of maintaining low inventory.
4. Enhanced Coordination Across Teams
Manufacturing processes require close coordination between multiple teams: procurement, production, and sales. INSIA’s integration capabilities help synchronize these teams by providing a single platform where everyone can access the same data in real-time. This ensures that your MRP system is always working with the most accurate and up-to-date information.
- Collaboration Tools: INSIA allows teams to collaborate through customizable dashboards and data-driven reports, ensuring that everyone from procurement managers to production line workers is aligned with the MRP process.
- Synchronized Schedules: By integrating production and procurement schedules, INSIA ensures that materials arrive just in time, so your MRP system can operate efficiently and meet production deadlines.
Conclusion
We all know how important it is to keep production running smoothly, manage inventory, and meet deadlines. But if you’re struggling with fragmented data or delays in decision-making, your MRP system alone might not be enough.
By bringing all your data together in one place, INSIA helps you make quicker, smarter decisions. It complements your MRP system by giving you real-time insights and seamless coordination across your teams. No more wasted time or missed opportunities.