Data-driven decisions are no longer optional in manufacturing—they're the key to staying competitive. The business intelligence in manufacturing industry has transformed how companies track production, manage supply chains, and reduce costs. With the right BI tools, manufacturers can turn raw data into actionable insights, improving efficiency at every stage of operations.
From predictive maintenance to real-time quality control, business intelligence in manufacturing industry helps companies make faster, smarter decisions. The result? Optimized processes, reduced downtime, and higher profitability. Whether you're aiming to cut waste, streamline workflows, or forecast demand with precision, BI is the game-changer modern manufacturers can't afford to ignore.
Understanding Business Intelligence in Manufacturing
Manufacturing generates massive amounts of data every second—from production lines to supply chains, inventory levels, and quality control metrics. However, without the right tools, this data remains untapped potential. This is where business intelligence in manufacturing industry makes a difference. BI solutions transform raw data into clear, actionable insights that improve efficiency, reduce costs, and enhance overall decision-making.
To understand the impact, consider a mid-sized automotive parts manufacturer struggling with unpredictable machine failures. Without a BI system, unexpected breakdowns lead to production delays, high maintenance costs, and missed deadlines. However, by implementing BI-powered predictive analytics, the company gains real-time visibility into machine performance. Sensors track wear and tear, and AI-driven insights predict when maintenance is needed—preventing costly downtime and keeping production on schedule.
The demand for BI solutions is growing at an unprecedented rate. In 2024, the global business intelligence market was valued at $30.1 billion. It is expected to surpass $116.25 billion by 2033, with a 14.98% CAGR from 2025 to 2033. This rapid expansion signals a clear trend—manufacturers are prioritizing data-driven decision-making to stay competitive in an evolving market.
Manufacturing has always relied on data, but how companies use it has changed. Let’s explore BI’s journey from manual records to AI-driven insights.
The Evolution of Business Intelligence in Manufacturing
Manufacturers have always relied on data, but the way they use it has changed dramatically over time. In the early 20th century, businesses focused on manual record-keeping and time-motion studies, pioneered by Frederick Taylor’s scientific management. The goal was simple: improve efficiency by analyzing workflows.
By the 1960s, manufacturing companies started using basic computer systems to track inventory and production metrics. These systems laid the foundation for more sophisticated Enterprise Resource Planning (ERP) software, which gained traction in the 1990s. ERP solutions helped manufacturers consolidate their data, offering a clearer picture of supply chains, production efficiency, and financial performance.
The real shift happened in the early 2000s when business intelligence (BI) tools became mainstream. Instead of just collecting data, manufacturers began analyzing trends, identifying inefficiencies, and making data-driven decisions to improve operations. The rise of cloud-based platforms and automation made BI even more powerful, turning it into an essential part of modern manufacturing.
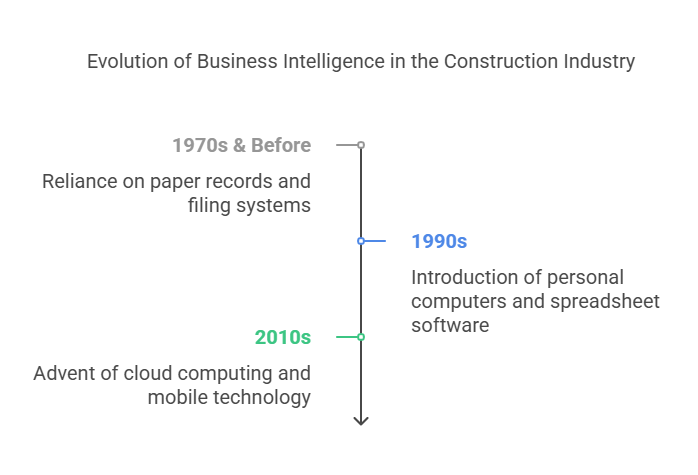
The progression of BI in manufacturing has been propelled by several key technological innovations:
- Big Data & Advanced Analytics – Instead of relying on spreadsheets and manual reports, manufacturers can now analyze massive datasets in real time. This helps identify inefficiencies, predict demand, and optimize production schedules.
- Artificial Intelligence (AI) & Machine Learning – AI-driven BI tools help manufacturers detect patterns that humans might miss. Predictive maintenance is a perfect example—machines equipped with sensors can alert teams before a breakdown happens, reducing downtime and maintenance costs.
- Internet of Things (IoT) & Smart Factories – Machines, sensors, and devices are now connected, constantly collecting and sharing data. This real-time feedback improves efficiency, ensures quality control, and helps manufacturers fine-tune their processes.
- Cloud Computing & Remote Access – Instead of relying on local servers, manufacturers can store and analyze data in the cloud. This allows decision-makers to access insights anytime, anywhere, without the need for expensive on-site IT infrastructure.
Also Read: Role and Benefits of Business Analytics in Manufacturing Industry
BI has evolved beyond static reports. But what makes a BI system truly effective for manufacturing? Let’s break down its essential components.
Key Components of Business Intelligence in Manufacturing
Business Intelligence (BI) has become a critical asset in manufacturing, allowing companies to transform complex data into actionable insights. A successful BI framework relies on three key components—accurate data collection, seamless integration, and advanced analytics.
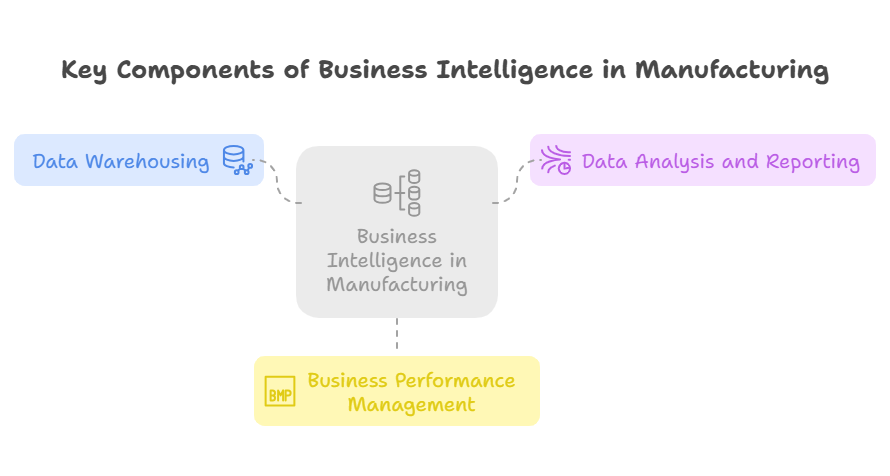
The following elements work together to improve efficiency, streamline operations, and enhance decision-making across the production floor:
- Data Sources and Collection for Manufacturing Insights
Manufacturers rely on real-time data to monitor efficiency, track quality, and prevent production issues. However, without structured data collection, critical insights get lost, leading to inefficiencies. Capturing accurate, real-time data is the first step in building a strong BI strategy.
Manufacturing data typically comes from:
- IoT Sensors and Smart Machines – Track performance, machine uptime, and potential failures.
- ERP and MES Systems – Consolidate production, inventory, and supplier data.
- Supply Chain & Logistics Databases – Monitor material availability and delivery timelines.
With automated data collection, manufacturers eliminate human error and ensure their BI system works with real-time, high-quality data.
- Integration of Data into Warehouses for Analysis
Raw data holds immense potential, but without proper integration, it remains fragmented and difficult to analyze. A centralized data warehouse allows manufacturers to store, organize, and process data efficiently—turning scattered information into structured reports.
Effective data integration allows manufacturers to:
- Unify production, inventory, and supplier data in one place.
- Detect inefficiencies by comparing historical and real-time performance.
- Standardize reporting across multiple manufacturing plants.
With a structured data warehouse, businesses gain a complete, 360-degree view of their operations, making decision-making faster and more reliable.
- Use of Advanced Analytics and Visualization Tools
Having data is one thing—understanding it is another. BI tools help manufacturers visualize performance trends, detect inefficiencies, and predict future challenges through dashboards, reports, and AI-driven analytics.
Modern BI platforms provide:
- Real-time dashboards to track production efficiency.
- Predictive analytics for maintenance and quality control.
- Custom reporting tools for executives and plant managers.
By turning raw data into clear insights, BI solutions empower manufacturers to make faster, smarter decisions that drive profitability.
Knowing what powers BI is one thing, but how does it transform daily operations? Here’s how manufacturers apply BI to optimize efficiency.
Applications of Business Intelligence in Manufacturing
Business Intelligence isn’t just about collecting data—it’s about applying it to improve manufacturing operations. From production scheduling to supply chain optimization, BI solutions help businesses increase efficiency, reduce costs, and maintain quality standards. Below are five real-world applications of BI in manufacturing.
Production Scheduling and Real-Time Machine Insights
An efficient production schedule ensures that materials, workforce, and machinery work in sync to maximize output. However, unexpected bottlenecks, equipment failures, and supply shortages can throw schedules off track, leading to delays and financial losses.
BI tools provide real-time machine monitoring and automated scheduling, allowing manufacturers to:
- Detect slowdowns before they disrupt production.
- Optimize resource allocation based on real-time demand.
- Ensure machines operate at peak efficiency.
By aligning production with real-time insights, manufacturers reduce waste, avoid downtime, and meet customer demands on time.
Optimizing Supply Chain Management with Real-Time Visibility
A well-functioning supply chain ensures that raw materials arrive on time and at the right cost. Disruptions—whether due to supplier delays, demand fluctuations, or geopolitical factors—can lead to costly bottlenecks.
BI-powered supply chain monitoring allows businesses to:
- Track supplier performance and predict potential disruptions.
- Adjust procurement strategies based on market conditions.
- Ensure seamless coordination between logistics, production, and distribution.
With real-time supply chain insights, manufacturers gain better control over inventory, costs, and delivery timelines.
Maintaining Optimal Inventory Levels and Forecasting Demand
Excess inventory ties up cash, while shortages halt production. A data-driven approach helps manufacturers find the right balance between supply and demand.
BI solutions analyze historical sales data, production trends, and supplier lead times to:
- Predict material shortages before they occur.
- Minimize excess inventory and reduce carrying costs.
- Ensure smooth production without overstocking.
By forecasting demand accurately, businesses cut costs and improve order fulfillment rates.
Quality Management and Real-Time Defect Tracking
A single product defect can damage brand reputation and lead to costly recalls. Manufacturers need a proactive approach to detect defects before they reach customers.
BI-powered quality tracking systems allow manufacturers to:
- Analyze defect patterns across different production lines.
- Pinpoint the root causes of quality issues in real time.
- Implement corrective measures before large-scale problems occur.
By monitoring quality metrics continuously, manufacturers ensure higher product consistency and lower rejection rates.
Predictive Maintenance to Minimize Downtime
Unexpected machine failures disrupt production, increase costs, and delay shipments. Instead of relying on scheduled maintenance, manufacturers can use BI-driven predictive maintenance to prevent failures before they happen.
BI tools help businesses:
- Monitor machine performance and detect early signs of wear.
- Schedule repairs proactively based on data insights.
- Reduce downtime and extend equipment lifespan.
With predictive analytics, manufacturers save money on maintenance and prevent costly production halts.
Also Read: Top 10 Data Analytics Tools for 2025
BI isn’t just about tracking data—it’s about turning insights into action. Here’s why adopting BI drives efficiency, cost savings, and quality improvements.
Benefits of Implementing BI in Manufacturing
Manufacturing is all about efficiency—keeping production on track, managing costs, and maintaining quality. But when decisions rely on gut feeling or outdated reports, companies risk delays, waste, and missed opportunities. Business Intelligence (BI) changes the game by turning raw data into real-time insights. Here’s how.
- Improving Operational Efficiency and Decision-Making
Every second counts in manufacturing. A delayed shipment, a machine running below capacity, or a bottleneck in production can set back entire operations. Without clear visibility, decision-making is slow and reactive. BI provides real-time data on production lines, inventory, and machine performance, helping managers spot and fix issues before they become major problems.
When teams can see performance trends and adjust schedules instantly, they reduce downtime and keep output steady. Instead of waiting for reports, decision-makers get the answers they need—when they need them—so the business runs at full speed.
- Cost Reduction Through Process Optimization
Wasted materials, inefficient labor, and unnecessary energy use all eat into profit margins. Many manufacturers don’t realize how much money they’re losing due to small inefficiencies that add up over time. BI pinpoints where costs are creeping up and what changes can make a real impact.
By tracking machine efficiency, production waste, and supply chain expenses, businesses can identify areas to streamline and cut excess spending without sacrificing productivity. With BI, manufacturers gain control over their costs, reduce financial waste, and make every dollar count.
- Enhancing Product Quality Through Data-Driven Insights
A single defective product can hurt a company’s reputation and lead to costly recalls. Traditional quality control methods often catch issues too late, when products have already left the factory. BI changes that by monitoring production quality in real time. It flags defects as soon as they appear, allowing teams to identify patterns, pinpoint root causes, and fix problems before they escalate.
If a supplier is delivering faulty materials or a production step is causing inconsistencies, BI makes it easy to track and correct. By focusing on quality at every stage, manufacturers can reduce defects, lower return rates, and keep customers satisfied.
- Increased Visibility and Control Over Manufacturing Operations
Manufacturing involves so many moving parts that it’s easy to lose track of what’s really happening. BI centralizes data from across the factory, giving decision-makers a clear, real-time view of operations.
Instead of juggling different reports from various teams, managers can see everything in one place—inventory levels, production speed, machine performance, and supply chain updates. With this kind of oversight, teams react faster to issues, improve coordination, and ensure that operations run smoothly from start to finish.
Every investment needs justification. So, how can manufacturers measure BI’s impact beyond intuition? Let’s break down ROI calculation for BI success.
How to Calculate the ROI of Business Intelligence in Manufacturing?
Calculating ROI isn’t just about looking at immediate cost savings—it involves analyzing long-term operational improvements, efficiency gains, and revenue growth. A structured approach ensures that manufacturers can quantify the financial impact of BI and make data-driven investment decisions. Here's how to do it.
Step 1: Identify the Costs of Implementing BI
To measure ROI accurately, manufacturers must start with the total investment in BI. This includes both upfront and ongoing expenses such as:
- Software Licensing & Subscriptions – Costs for BI platforms, data analytics tools, and cloud-based solutions.
- Hardware & Infrastructure – Servers, data storage systems, and IoT sensors required for real-time data collection.
- Implementation & Integration – Costs for installing BI software, setting up data pipelines, and integrating with existing ERP or MES systems.
- Training & User Adoption – Expenses for onboarding employees, hiring consultants, and providing ongoing support.
- Maintenance & Upgrades – Long-term costs for system updates, security patches, and scaling capabilities.
Once all costs are documented, manufacturers gain a baseline figure that represents the total investment in BI.
Step 2: Measure the Financial Gains from BI
The next step is to quantify the financial impact BI has on manufacturing performance. ROI is measured by calculating how BI contributes to:
- Increased Productivity – Faster decision-making, reduced downtime, and better workflow automation.
- Lower Operational Costs – Reduced waste, optimized material usage, and predictive maintenance that prevents costly breakdowns.
- Improved Quality Control – Lower defect rates, fewer recalls, and enhanced product consistency leading to reduced rework costs.
- Supply Chain Optimization – Better inventory management, fewer shortages, and improved supplier coordination.
- Revenue Growth – Higher production output, better customer satisfaction, and improved forecasting that prevents stockouts or excess inventory.
By assigning a dollar value to each improvement, manufacturers can calculate the total financial gain from BI adoption.
Step 3: Use the ROI Formula
Once the costs and financial benefits are identified, manufacturers can apply a simple formula to calculate the ROI of BI:
For example, if a manufacturer invests $500,000 in BI and sees annual cost savings and revenue increases totaling $1.5 million, the ROI would be:
A 200% ROI means that for every $1 invested, the company gains $2 in returns, demonstrating a high-value investment.
Step 4: Track and Adjust Over Time
BI’s impact evolves over time, so ROI measurement shouldn’t be a one-time calculation. Manufacturers should continuously track key performance indicators (KPIs) such as production efficiency, defect rates, and cost reductions. By analyzing trends and making adjustments, companies can maximize BI’s value and ensure long-term profitability.
Also Read: What is Cloud Data Analytics?
A high ROI is great, but is your data accurate and secure? Without governance, insights lose value. Here’s how to protect and manage BI data.
Data Governance and Security in Manufacturing BI
Data is one of the most valuable assets in manufacturing, but without proper governance and security, it can become a liability. Business Intelligence (BI) relies on accurate, accessible, and secure data to drive decision-making. However, manufacturers face growing risks such as data breaches, compliance violations, and system vulnerabilities.
Below, check out how establishing a robust data governance framework ensures that BI systems function efficiently, securely, and fully comply with industry regulations.
The Role of Data Governance in BI
Effective BI starts with well-structured data governance. This involves defining policies, standardizing data collection, and ensuring data integrity across all systems. Without governance, manufacturers risk inconsistent reporting, duplicate records, and inaccurate insights that can lead to costly mistakes.
A strong data governance strategy includes the following:
- Data Ownership and Accountability – Assigning clear roles for who collects, manages, and validates data.
- Standardization and Consistency – Ensuring all data follows a uniform format across different departments and facilities.
- Access Control and Permissions – Restricting data access based on job roles to prevent unauthorized modifications.
- Auditability and Traceability – Keeping a record of changes to ensure data integrity and compliance.
By implementing a structured governance framework, manufacturers reduce errors, improve data trustworthiness, and ensure that BI-driven decisions are based on accurate insights.
Security Challenges in Manufacturing BI
Manufacturers process vast amounts of sensitive data, including production metrics, supplier contracts, intellectual property, and customer information. Cyber threats such as ransomware attacks, insider threats, and data leaks pose significant risks if security measures are not in place. Weak security compromises operational continuity, damages brand reputation, and leads to regulatory penalties.
Key security challenges include:
- Unauthorized Access – Poorly configured access controls can expose critical production and financial data to unauthorized users.
- Data Breaches – Hackers target manufacturing networks to steal intellectual property and disrupt operations.
- Legacy System Vulnerabilities – Older infrastructure often lacks modern security protocols, making it an easy target for cyberattacks.
- Regulatory Compliance Risks – Failure to meet industry standards, such as GDPR, CCPA, or ISO 27001, can lead to legal consequences and financial penalties.
Ignoring these risks can cripple operations and erode competitive advantage, making security a top priority in BI implementation.
Best Practices for Securing BI in Manufacturing
To protect BI data from threats, manufacturers must adopt a proactive security approach that covers both infrastructure and internal policies. A layered security strategy ensures that data remains confidential, accessible only to authorized personnel, and resilient against attacks.
Key security measures include:
- Role-Based Access Controls (RBAC) – Granting employees access only to the data necessary for their job function to minimize risk.
- Encryption and Secure Data Storage – Encrypting data both in transit and at rest to prevent unauthorized interception.
- Multi-Factor Authentication (MFA) – Requiring multiple verification steps for accessing BI platforms and dashboards.
- Continuous Monitoring and Threat Detection – Using AI-driven analytics to detect unusual activity and prevent security breaches in real time.
- Regular Security Audits and Compliance Checks – Ensuring adherence to industry regulations and updating security policies as threats evolve.
By implementing these safeguards, manufacturers protect their BI infrastructure from threats while maintaining compliance with industry standards.
Even the best BI tools face adoption hurdles. How can manufacturers implement BI successfully? Let’s uncover challenges and best practices for seamless integration.
Challenges and Best Practices for BI Adoption
Business Intelligence (BI) adoption in manufacturing requires more than just installing software—it’s about ensuring seamless integration, user adoption, and long-term value. However, manufacturers often struggle with data inconsistencies, lack of company-wide adoption, and tool selection, which can slow down implementation. Addressing these challenges early prevents bottlenecks and maximizes BI’s potential.
- Ensuring Data Quality and Consistency
BI insights are only as good as the data they process. When numbers don’t align across systems, decision-makers question BI’s reliability and revert to manual processes. Manufacturing data comes from multiple sources—production lines, supply chains, and inventory systems—often resulting in inconsistencies.
To prevent this, companies must standardize data collection methods, enforce validation rules, and automate data cleansing. Regular data audits ensure reports remain accurate and actionable, allowing teams to make informed decisions without second-guessing the numbers.
- Stakeholder Involvement Across the Organization
BI tools deliver results only when employees actively use them. If only data analysts engage with BI while plant managers and executives continue relying on spreadsheets and intuition, adoption remains fragmented. For BI to succeed, it must be embedded into daily workflows at every level.
Companies should focus on role-specific training to ensure employees understand how BI benefits their specific tasks. Simplified dashboards with user-friendly visualizations encourage daily use, and leadership must lead by example by making BI insights central to strategic discussions.
- Selecting the Right BI Tools and Techniques
Not all BI platforms are built for manufacturing needs. Some focus on basic reporting, while others specialize in predictive analytics and real-time monitoring. Choosing the wrong tool can result in poor adoption, integration difficulties, and wasted investment.
Before selecting a BI system, companies must define clear objectives—whether it’s reducing machine downtime, optimizing supply chains, or improving defect tracking. Compatibility with existing ERP, IoT, and automation systems is critical. A phased rollout, starting with a pilot implementation before full deployment, ensures smoother adoption.
- Monitoring and Measuring BI Implementation Progress
BI isn’t a set-it-and-forget-it tool—its success depends on ongoing performance tracking and refinement. Many manufacturers implement BI without setting clear benchmarks, leading to uncertainty about its impact.
To ensure BI delivers value, companies should track KPIs directly tied to operational improvements—such as faster production cycles, fewer equipment failures, or reduced inventory costs. If adoption rates are low, teams should evaluate whether BI dashboards are intuitive enough and delivering insights that are truly actionable.
- Security and Privacy Concerns in BI Adoption
As BI adoption expands, balancing security with accessibility becomes a challenge. Companies must protect sensitive production and financial data while ensuring employees can access the insights they need to make fast decisions. Overly restrictive security policies can slow down BI adoption, while weak security creates compliance risks.
One major challenge is resistance to stricter data access policies. Employees accustomed to unrestricted access may push back against new role-based restrictions that limit what they can see or modify. Striking the right balance requires tiered access policies that align with operational workflows, ensuring security without hindering productivity.
Another issue is the complexity of securing BI across multiple facilities and cloud-based systems. Unlike traditional on-premise security models, BI often integrates with external cloud platforms, supplier networks, and remote monitoring systems, increasing the risk of third-party vulnerabilities.
Companies must enforce secure API connections, real-time activity monitoring, and vendor compliance checks to protect data integrity without disrupting BI functionality.
BI is evolving rapidly. What’s next? From AI to IoT, the future of manufacturing intelligence is already here. Let’s explore what’s ahead.
The Future of BI in Manufacturing
Manufacturers are moving beyond traditional BI dashboards and embracing intelligent, automated systems that process data in real time. Here’s how it's moving forward.
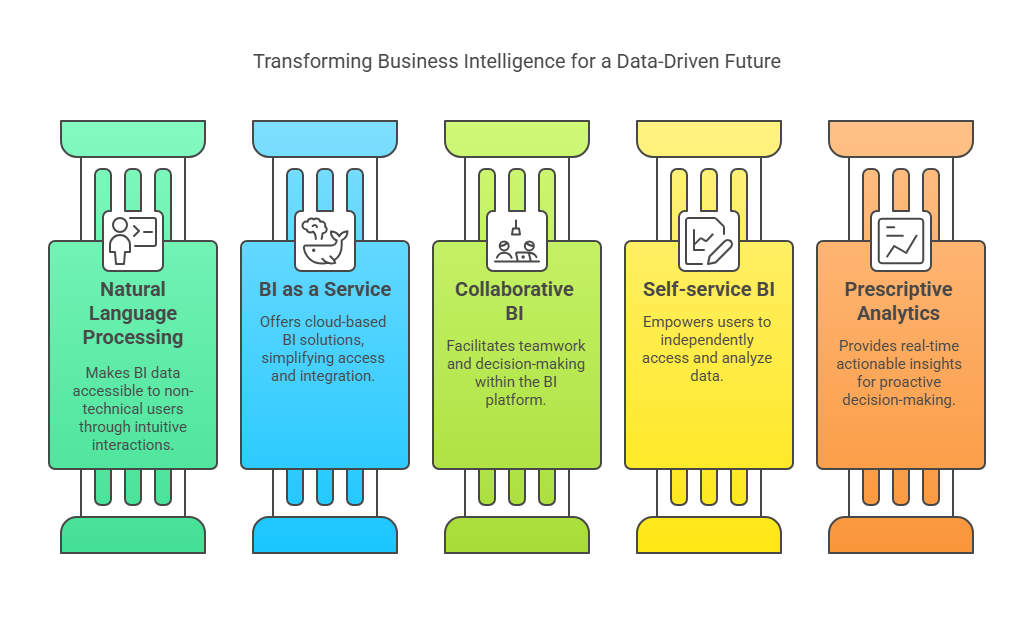
Artificial Intelligence and Machine Learning: From Analysis to Automation
AI and ML are no longer just about finding trends in data—they are enabling BI to take action autonomously. The next generation of AI-powered BI systems will continuously learn from new data, making real-time adjustments to production schedules, inventory levels, and machine performance without requiring human intervention.
Here’s how AI and ML are evolving within BI:
- Automated Decision Augmentation – AI is transitioning from passive data analysis to active decision support, where BI platforms provide actionable recommendations rather than static reports.
- Self-Learning Systems – ML algorithms are improving BI accuracy over time by refining predictions and recommendations based on historical data and real-time inputs.
- AI-Powered Process Automation – AI-driven BI tools are integrating with manufacturing execution systems (MES) and ERP platforms, automating adjustments to inventory levels, procurement orders, and production workflows based on demand fluctuations.
Companies like Stellantis are already using AI-powered BI to analyze market trends and optimize production capacity in real time. As these systems advance, manual data analysis will become obsolete, replaced by AI-driven, self-optimizing BI ecosystems.
IoT and BI: Breaking Data Silos and Enhancing Real-Time Decision Cycles
The integration of IoT and BI is revolutionizing real-time data processing by eliminating delays in reporting and decision-making. Instead of collecting data, analyzing it separately, and then acting on it, IoT-driven BI enables instant action based on live insights.
How IoT is transforming BI in manufacturing:
- Real-Time Operational Intelligence – IoT sensors continuously feed machine performance, energy consumption, and environmental data into BI systems, allowing manufacturers to detect inefficiencies the moment they occur.
- Eliminating Data Silos – Traditional BI often relies on batch-processed data, causing delays in insights. IoT-integrated BI systems process live, streaming data from multiple sources, enabling faster and more accurate decision-making.
- End-to-End Supply Chain Synchronization – IoT-powered BI links suppliers, logistics, and production teams to ensure materials arrive on time, equipment operates efficiently, and demand fluctuations are instantly accounted for.
For instance, Telefónica and Siemens are developing fully digitalized industrial environments that merge 5G, IoT, and AI to enable autonomous factory operations, where BI not only monitors but actively controls production in real time.
Cloud Computing: Making BI More Adaptive and Scalable
Cloud BI is evolving beyond data storage and processing—it’s now about real-time collaboration, AI integration, and multi-cloud ecosystems that enhance flexibility and security. The shift to cloud-native BI solutions is removing technical barriers, making BI more adaptable and cost-effective.
Key advancements in cloud-based BI:
- Edge Computing for Instant Data Processing – Instead of sending all data to the cloud, BI platforms process critical insights at the edge (on-site), reducing latency and ensuring real-time responsiveness.
- Multi-Cloud Strategies for Resilience – Manufacturers are adopting multi-cloud BI architectures to avoid vendor lock-in and improve system redundancy, ensuring data availability even if one cloud provider experiences downtime.
- Cloud-AI Convergence – AI-driven BI tools hosted in the cloud allow for scalable, AI-powered analytics without the need for expensive on-premise hardware.
By applying cloud-native BI systems, manufacturers can scale their analytics capabilities globally, integrating IoT data, AI insights, and real-time collaboration tools into a single, unified platform.
The future is clear—data-driven manufacturing is non-negotiable. But why settle for outdated tools? INSIA takes BI to the next level.
Revolutionize Manufacturing Decisions: Unleashing INSIA's BI Power on Your Floors
Manufacturing is moving at an unprecedented pace. Staying competitive means having instant access to data, predicting challenges before they happen, and making split-second decisions that optimize production, reduce waste, and improve efficiency. Traditional Business Intelligence (BI) tools fall short because they are slow, disconnected, and require manual effort to consolidate data.
INSIA changes that.
INSIA is a game-changer for manufacturers, providing real-time analytics, AI-powered predictions, and seamless cross-department integration. Whether you’re on the shop floor, in the boardroom, or managing supply chains, INSIA’s powerful BI platform ensures you have the right data at the right time, on any device. Let’s check how INSIA works.
- Mobile Analytics for Manufacturing: Decision-Making at Your Fingertips
Manufacturing doesn’t happen behind a desk—it happens on the production floor. INSIA’s mobile analytics ensure that real-time insights are available wherever you are, so you can make critical decisions on the go.
Key Benefits:
- Real-Time Production Insights – Stay ahead of disruptions by monitoring machine performance, supply chain data, and operational KPIs in real time.
- Cross-Device Accessibility – Whether on a smartphone, tablet, or laptop, INSIA’s responsive design keeps you connected without being tied to an office.
- On-the-Go Decision Making – Make faster, data-backed decisions with AI-powered alerts and real-time reporting.
- Shop Floor Monitoring – View live production metrics and spot inefficiencies before they cause downtime.
Case Study: Kirloskar Oil Engines reduced reporting time by 70% after implementing INSIA, streamlining production insights and accelerating data-driven decision-making.
- Manufacturing-Specific Dashboards: Instant Clarity, Zero Guesswork
INSIA offers custom-built dashboards designed specifically for manufacturers, helping teams track key production, quality, and inventory metrics in real time.
What You Can Monitor:
- Production KPIs – Track cycle times, throughput, downtime, and yield rates to optimize efficiency.
- Inventory Levels – Gain a real-time view of raw materials, work-in-progress (WIP), and finished goods to prevent overstocking or shortages.
- Quality Control Metrics – Reduce defects with automated analytics that detect inconsistencies and ensure compliance.
- Equipment Performance Visualization – View machine health, energy consumption, and predictive maintenance alerts to avoid unexpected failures.
Case Study: Crescent Foundry used INSIA to gain a comprehensive operations view, resulting in a 40% reduction in reporting costs and 50% faster insights.
- Predictive Analytics Features: Eliminate Surprises, Stay Ahead
INSIA doesn’t just report what happened—it predicts what will happen next. Using AI-powered Predictive Analytics, manufacturers can anticipate production issues, optimize resource planning, and forecast demand with accuracy.
AI-Powered Features:
- Push AI for Production Forecasting – Get instant, AI-driven recommendations on optimizing production schedules based on historical and real-time data.
- Maintenance Predictions – Reduce machine failures by detecting early warning signs and scheduling maintenance before breakdowns occur.
- Demand Forecasting – Accurately predict market trends and customer demand, ensuring optimal inventory levels and reducing excess stock.
- Resource Optimization – INSIA automatically identifies ways to improve material usage, workforce allocation, and energy consumption.
Case Study: Alaric Enterprises reduced forecasting time by 60% and manual effort by 50% after adopting INSIA’s AI-powered predictive analytics.
- Cross-Department Integration: A Unified Data Ecosystem
One of the biggest challenges in manufacturing is data fragmentation—with different teams using separate tools for production, inventory, finance, and quality control. INSIA eliminates these silos by seamlessly integrating all critical manufacturing data into one platform.
Seamless Integration With:
- ERP Systems – Connect SAP, Oracle, Microsoft Dynamics, and other enterprise systems for a single source of truth.
- Production Data – Link shop floor data with financial planning, supply chain, and demand forecasting for better decision-making.
- Inventory Management – Avoid stock issues by automating real-time inventory tracking and forecasting needs.
- Quality Control Systems – Identify patterns in defect rates, compliance metrics, and corrective actions to improve product consistency.
Case Study: Trident Services automated 90% of its reporting and achieved a 70% faster report generation time after implementing INSIA’s cross-department integration.
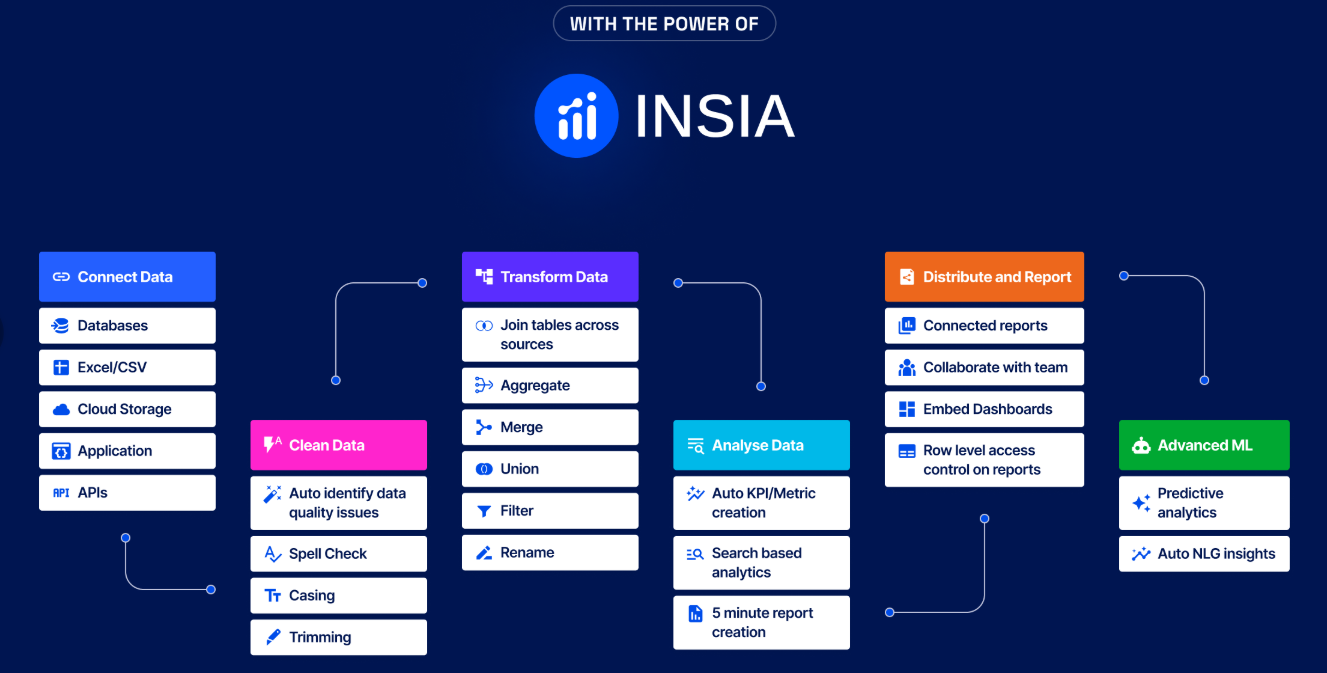
Conclusion
Manufacturers who rely on outdated, manual reporting waste time, miss opportunities, and struggle to stay competitive. INSIA empowers manufacturing leaders with real-time insights, AI-driven predictions, and a fully integrated data ecosystem—all accessible on any device, anytime, anywhere.