TL;DR – Key Takeaways
- Manufacturers use real-time sensor data and historical trends to anticipate equipment failures and schedule maintenance before breakdowns.
- Predictive analytics helps manufacturers like Ford and Dell align production with market trends, avoid overproduction, and manage inventory efficiently, reducing waste and lost sales.
- Companies such as Coca-Cola use predictive models to plan for raw material costs and procurement, leading to better budgeting, supplier management, and reduced operational expenses.
- Predictive analytics flags unreliable vendors and disengaged customers early on, allowing for proactive retention strategies and more resilient supply chain decisions.
- By analyzing data from sensors during production, manufacturers can detect quality issues early, minimize rework and defects, and ensure high customer satisfaction.
Manufacturers often face challenges like unexpected equipment breakdowns, inefficient inventory management, and fluctuating demand, all of which can lead to costly setbacks. Predictive analytics in manufacturing offers a solution by using data-driven insights to forecast potential issues and optimize operations. By analyzing historical data and identifying patterns, manufacturers can predict equipment failures, manage inventory more effectively, and even anticipate shifts in demand.
This proactive approach reduces costs and improves efficiency, making it a game-changer for the industry. In fact, the global predictive analytics market was valued at $10.2 billion in 2023 and is expected to reach $63.3 billion by 2032, growing at a remarkable annual rate of 22.4%.
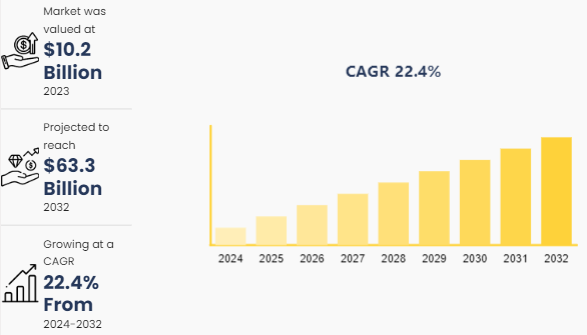
This article will explore key use cases, benefits, and future predictive analytics trends, providing actionable insights to enhance manufacturing processes and improve decision-making.
Introduction to Predictive Analytics in Manufacturing
Predictive analytics in manufacturing leverages data to anticipate future events, empowering manufacturers to make proactive decisions and reduce downtime. By combining historical data, machine learning, and statistical models, manufacturers can identify patterns that reveal potential issues before they arise. Today, predictive analytics incorporates external data, such as seasonal demand trends.
For example, generator manufacturers can use predictive insights on warmer weather patterns to prepare for increased demand in summer. This holistic approach helps solve everyday production challenges, improve resource planning, and boost operational efficiency.
Now, let’s look at a predictive maintenance analytics example. Consider a car manufacturing plant where hundreds of machines work daily to assemble vehicles. These machines often undergo wear and tear over time, and unexpected breakdowns can halt production for hours, leading to costly delays. The factory uses predictive analytics to collect data on each machine's operating conditions, such as temperature, vibrations, and performance levels.
Over time, the data reveals patterns indicating when a machine will likely experience issues. For instance, if a particular machine's temperature rises before malfunctioning, predictive analytics can signal the maintenance team to service it before it breaks down. This proactive approach reduces unplanned downtime and saves significant repair costs, improving overall efficiency.
Now that we've covered the basics, let’s explore how predictive analytics transforms manufacturing through real-world applications.
Key Use Cases of Predictive Analytics in Manufacturing
In June 2022, the U.S. Federal Government took steps to support data-driven decision-making in a rapidly changing and competitive national economy. Predictive analytics has transformed the manufacturing industry by providing data-driven insights that improve efficiency and reduce costs. Here are some key use cases where predictive analytics can make a significant difference:
Preventive Asset Maintenance
One of the most critical predictive analytics applications is preventive asset maintenance. Manufacturers rely on machines and equipment to keep production lines running smoothly. However, sudden breakdowns can cause delays and increase costs.
Predictive analytics helps identify patterns in machine performance by analyzing data such as temperature, vibration, and usage history. When certain indicators show that a machine will likely fail soon, maintenance can be scheduled before the breakdown occurs. This approach reduces unexpected downtime and extends the lifespan of the machinery.
For example, Samsung’s preventive asset management approach uses IIoT (Industrial Internet of Things) sensors, mobile devices, and predictive analytics to monitor equipment health continuously. By collecting real-time data on asset conditions and analyzing them for early signs of wear, Samsung can preemptively address issues, reducing downtime and extending asset life. Mobile tools like the Galaxy Tab Active2 ensure maintenance teams receive immediate alerts and insights, enabling timely intervention and optimizing equipment performance, which aligns with preventive strategies to minimize reactive maintenance costs.
Demand Forecasting
Accurately predicting future demand is crucial for manufacturers to ensure they produce the right goods. Overproduction leads to excess inventory and waste, while underproduction results in lost sales opportunities. Predictive analytics analyzes historical sales data, seasonal trends, and external factors like market shifts to forecast demand more accurately.
For example, Ford reported a $722 million loss in its electric vehicle (EV) division for Q1 2024 despite overall profits. This emphasizes the need for better demand forecasting. Predictive analytics can help manufacturers like Ford analyze historical data and market trends to predict better shifts in consumer demand for EVs versus gasoline-powered vehicles. With this insight, Ford can optimize production, minimize excess inventory, and better align with consumer preferences, improving operational efficiency and profitability.
Inventory Management
Inventory is one of the most challenging aspects of manufacturing. Too much inventory ties up capital and increases storage costs, while too little inventory can disrupt production and sales. Predictive analytics can optimize inventory management by forecasting raw materials and finished product demand.
By analyzing historical consumption data and supplier lead times, manufacturers can predict when to restock certain materials and in what quantities. This reduces the chances of stockouts while minimizing excess inventory.
For example, Dell manages inventory using a Build-to-Order (BTO) supply chain, where products are assembled only after receiving customer orders. This reduces the need to hold large inventories of finished goods and allows for more flexibility in manufacturing. Dell minimizes excess inventory and reduces costs by customizing components and streamlining procurement. The strategy will enable Dell to respond quickly to customer demands while maintaining an efficient and cost-effective production process, leading to improved profitability and supply chain optimization.
Spend Forecasting
Predictive analytics is helpful for physical operations and can also help manufacturers manage their finances more effectively. Spend forecasting uses historical data on expenses such as raw materials, labor, and equipment maintenance to predict future costs. By understanding spending trends, manufacturers can budget more effectively and identify areas where cost-saving measures can be implemented.
For example, Coca-Cola uses predictive analytics for spend forecasting by analyzing various factors like weather, crop yields, pricing, and demand trends. This approach helps the company make better decisions about sourcing raw materials, like oranges for juices. By predicting future costs and ingredient availability, Coca-Cola optimizes its procurement strategies and ensures efficient use of resources in its manufacturing processes. This leads to cost savings and more effective inventory management, ultimately improving operational efficiency.
Customer Churn Risk Prediction
While not often associated directly with manufacturing, customer churn is critical for manufacturers selling directly to consumers or distributors. Predictive analytics can identify customers at risk of discontinuing purchases by analyzing behavioral data, purchasing history, and engagement levels.
For example, a company that manufactures home appliances may use predictive analytics to determine which customers will likely stop buying its products based on declining purchase frequency. By identifying these customers early, manufacturers can take proactive steps, such as offering discounts or personalized recommendations, to retain them.
Vendor Risk Prediction
Vendors are a key part of the manufacturing supply chain, and disruptions on their end can directly impact production. Predictive analytics can assess vendor reliability by analyzing past performance data, delivery times, and product quality. This allows manufacturers to identify potential risks before they become critical.
For example, Boeing uses predictive analytics to manage vendor risks by evaluating supplier performance, delivery times, and product quality. This helps them anticipate potential disruptions and proactively address issues before they impact manufacturing. Boeing can make informed decisions by monitoring supplier reliability data, such as switching vendors if delays are detected. This approach ensures smoother production processes and minimizes costly delays in the supply chain.
Understanding how predictive analytics is applied across manufacturing gives us a clearer picture of its advantages. Let’s now explore the key benefits driving its adoption.
Benefits of Predictive Analytics in Manufacturing
Predictive analytics offers manufacturers a wide range of benefits by allowing them to make smarter, data-driven decisions. These advantages improve day-to-day operations and help manufacturers plan for the future more accurately. Here are some key benefits:
- Cost Savings
Predictive analytics helps manufacturers cut costs in various areas by optimizing processes. For example, predictive maintenance monitors machine performance and can save significant money by preventing unexpected equipment breakdowns. Imagine a factory where repairing a broken machine could cost $50,000 due to halted production and repair expenses. Using predictive analytics to schedule maintenance before a breakdown might cost $5,000 instead, saving $45,000. These savings multiply when applied across an entire production line.
Additionally, predictive analytics helps manage inventory more efficiently, reducing overstocking or understocking issues. For example, manufacturers can avoid holding too much inventory by predicting demand more accurately, which ties up cash. A manufacturer might reduce excess inventory by 10%, saving millions of dollars annually.
- Increased Customer Satisfaction
When manufacturers can accurately predict demand, they are better equipped to meet customer needs. Predictive analytics can help ensure products are always available, reducing the chances of stockouts that frustrate customers.
For example, during peak shopping seasons, such as Black Friday, predicting demand spikes helps companies maintain optimal stock levels, ensuring customers receive their products on time.
Moreover, predictive analytics can help improve product quality by detecting issues early. If a product shows signs of quality decline, manufacturers can fix the problem before customers are impacted, leading to higher satisfaction rates. For instance, early detection of a 5% increase in product defects can help prevent large-scale returns or complaints.
- Improved Product Quality
Manufacturing processes are complex, and small issues can quickly snowball into significant quality problems. Predictive analytics allows manufacturers to identify quality issues early in the process. By analyzing data from sensors on machines or production lines, manufacturers can detect subtle patterns suggesting a drop in product quality.
Suppose a factory produces smartphones. Predictive analytics monitors key factors like temperature and pressure during the assembly process. If a minor variation in these factors is detected, such as a slight increase in temperature during screen assembly, it can indicate potential defects. The system alerts the production team, allowing them to adjust settings before the quality of the final product is compromised.
This early detection prevents large-scale quality issues, reducing the likelihood of faulty products reaching customers and minimizing costly recalls or rework.
- Proactive Decision-Making
One of the biggest shifts predictive analytics brings to manufacturing is moving from reactive to proactive decision-making. Predictive analytics allows manufacturers to foresee and address potential issues beforehand instead of waiting for issues like machine failures, inventory shortages, or quality problems. This results in smoother operations and fewer disruptions.
For example, consider a manufacturer relying on a global supply chain for raw materials like steel. Predictive analytics may forecast a shortage of steel due to geopolitical factors or market fluctuations. With this information, the company can proactively source alternative suppliers or stockpile materials before the shortage hits.
This foresight prevents production delays and costly downtime, ensuring operations continue without disruption. By making decisions ahead, the manufacturer avoids scrambling for solutions during a crisis, leading to smoother, more efficient production.
- Making Manufacturers Future-Ready
Predictive analytics doesn’t just focus on solving current problems; it also prepares manufacturers for future challenges. By continuously analyzing data, manufacturers can adapt to changing market conditions, customer preferences, and supply chain fluctuations.
For instance, consider an automobile manufacturer transitioning to electric vehicles (EVs). By using predictive analytics, the company can analyze consumer trends, market data, and regulatory changes to anticipate future demand for EVs. For example, it might predict that by 2028, 40% of consumers will prefer electric cars due to rising fuel prices and stricter environmental laws. Based on this insight, the manufacturer could invest in EV production facilities, securing supply chains for necessary materials like lithium and cobalt ahead of time. This proactive planning positions them to meet future market demands seamlessly.
While the benefits are compelling, implementing predictive analytics in manufacturing comes with its own set of challenges. Here’s a look at these obstacles and how they can be effectively addressed.
Challenges and Solutions in Implementing Predictive Analytics in Manufacturing
While predictive analytics offers many benefits, implementing it can be challenging. Understanding these roadblocks and knowing how to address them is key to a successful integration.
- Data Collection and Quality
One of the biggest challenges manufacturers face is gathering accurate and high-quality data. Machines generate massive amounts of data, but if this data is incomplete or inconsistent, it can lead to unreliable predictions. For example, if sensor data from a production line isn’t captured consistently, predictive models may not provide accurate forecasts.
Solution: Manufacturers should implement systems that ensure real-time and accurate data collection. Regularly maintaining sensors and machines and cross-checking data integrity ensures predictions are based on trustworthy information.
- Expertise and Strategy
Predictive analytics requires combining data science skills and a clear strategy aligned with business goals. Many manufacturing teams lack the internal expertise to leverage these advanced tools fully.
Solution: Partnering with external data experts or training in-house teams on data science can help bridge this gap. A clear roadmap ensures that predictive analytics is aligned with long-term goals, providing manufacturers with the insights to stay competitive.
Overcoming challenges is key, but a strong foundation ensures lasting success. Let's look at the essential elements for sustainable impact in manufacturing.
Foundational Elements for Success in Predictive Analytics
Certain foundational elements must be in place for manufacturers to benefit from predictive analytics. These core components ensure that predictions are accurate, actionable, and aligned with business goals.
- Single Source of Truth
Data is often scattered across different manufacturing systems, making it hard to understand what’s happening clearly. A Single Source of Truth (SSOT) means centralizing all relevant data so that every team member can access the same accurate and up-to-date information.
Generating reliable insights is easier when all departments, from production to maintenance, rely on one unified data system. For example, when the production and quality control teams access the same machine data, they can spot issues faster and improve coordination.
- Simplifying Machine Learning Implementation
Machine learning is a powerful tool in predictive analytics, but its implementation doesn’t always have to rely on a large team of data scientists. With technological advancements, manufacturers can use user-friendly platforms that automate much of the machine learning process. These platforms allow even non-experts to implement predictive models by following guided steps.
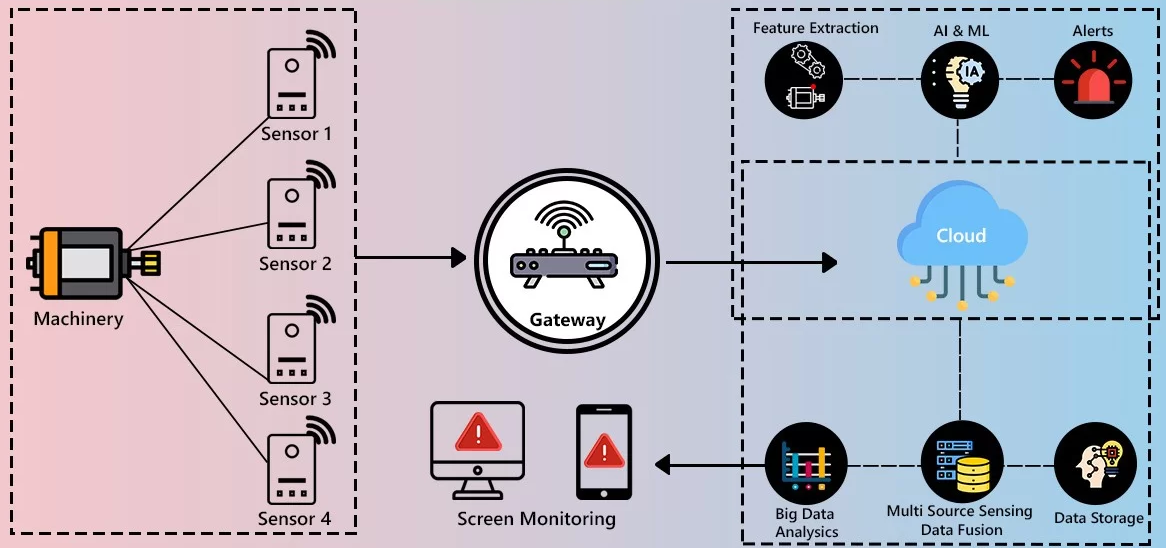
For example, imagine a production supervisor with limited technical knowledge who can use a simple interface to set up an AI-based predictive maintenance model that monitors machinery performance in real time.
- Monitoring and Tracking Algorithm Performance
Once predictive analytics models are in place, monitoring their performance is crucial. Predictions are only useful if they stay accurate over time. This involves regularly tracking the performance of algorithms to ensure they continue to provide meaningful insights. Manufacturers must monitor predictive analytics and other types, such as descriptive, diagnostic, and prescriptive analytics. By keeping everything in one place, businesses can use data holistically to improve decision-making.
With the foundational elements in place, let’s look at how predictive analytics is set to shape the future of manufacturing.
Future of Predictive Analytics in Manufacturing
The future of predictive analytics in the manufacturing industry looks promising, especially with the advancements in artificial intelligence (AI) and machine learning. As these technologies evolve, manufacturers will have access to even more powerful tools to optimize their operations and make smarter decisions.
Self-Serve Predictive Analytics
One major trend is the rise of self-serve predictive analytics tools. These platforms are designed to be user-friendly, allowing people with little to no technical expertise to harness the power of predictive analytics.
Here’s a simple breakdown of how Self-Serve Predictive Analytics works:
- Users log into the system and access a user-friendly dashboard.
- They choose a pre-built predictive model suited to their task (e.g., predicting equipment failure).
- Guided workflows help users input their data step-by-step.
- The tool analyzes real-time data and runs predictions.
- Automated reports present insights through easy-to-understand visuals.
- Users can quickly apply actionable insights to improve decision-making without a deep understanding of data science.
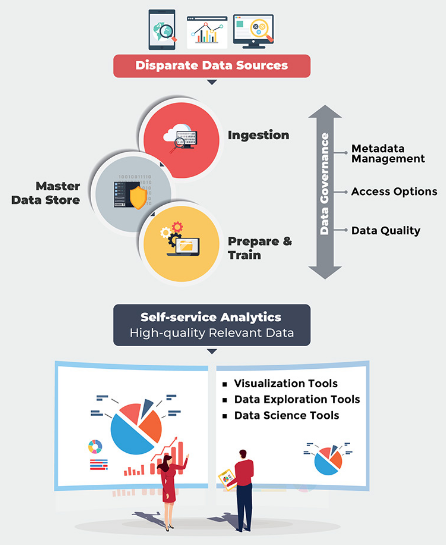
For manufacturers, this means that employees across different departments—whether in production, supply chain, or quality control—can easily access and use data insights without relying heavily on data science teams. For instance, a plant manager could use a self-serve tool to predict equipment maintenance needs based on data, even if they don’t have a background in data science.
Self-Learning Platforms
Another exciting development is the emergence of self-learning platforms. These systems continuously improve their algorithms by learning from new data and feedback. In manufacturing, this could mean that predictive models become more accurate over time as they process more data and adjust to real-world conditions.
Here’s how Self-Learning Platforms work:
- The platform starts with a basic predictive model built on historical data.
- The system continuously learns and updates its algorithms as new data flows in.
- It adjusts based on feedback and real-time performance, improving accuracy over time.
- The platform uses this updated data to refine predictions, making them more precise with each iteration.
- Over time, the system becomes better at recognizing patterns and trends, helping manufacturers make more informed decisions with minimal manual intervention.
For example, a predictive maintenance model might flag machinery issues based on past data. The model learns and more accurately predicts future problems as it receives new performance data.
Conclusion
Predictive analytics revolutionizes manufacturing by improving efficiency, reducing costs, and enabling proactive decision-making. INSIA’s platform equips manufacturers with the tools to harness this power seamlessly.
Here’s how INSIA can help manufacturers with predictive analytics:
- Push AI: Uses AI to provide proactive insights, allowing manufacturers to predict real-time issues like equipment failures or demand changes.
- Predictive Analytics: Helps forecast trends and efficiently manage production without complex coding.
- Real-Time Insights: Manufacturers get instant updates on their operations, enabling quicker, more informed decisions.
- Drill-Down Analytics: Allows deeper exploration of production data, identifying trends or potential issues quickly.
- Automated Reporting: Reduces manual effort by delivering timely insights via dashboards and email.
- Custom Dashboards: Tailored for manufacturers to track specific metrics, such as equipment health and production output.
- Data Transformation: Combines multiple data sources (like ERP systems), ensuring comprehensive and accurate data for analysis.
Frequently Asked Questions (FAQs)
1. What is Predictive Analytics?
Predictive analytics might sound complicated, but at its core, it's all about using data to predict what’s coming next. Imagine being able to anticipate when your machines will need maintenance, or knowing in advance if demand for your product will spike. By looking at past data, predictive analytics lets manufacturers make smarter, proactive decisions instead of reacting to issues as they pop up. It's like being a step ahead—every time.
2. How Can Predictive Maintenance Keep My Equipment Running Smoothly?
You know how frustrating it is when a machine breaks down unexpectedly. It disrupts everything, right? Predictive maintenance changes that. By using data from your machines, like temperature or vibration readings, you can spot signs that something might go wrong before it actually does. So, instead of waiting for a machine to stop working, you can fix it when it’s convenient, saving you time and a lot of money in the long run.
3. How Does Demand Forecasting Help Me Plan Better?
Nobody likes overstocking (hello, extra storage costs!) or running out of stock (goodbye, sales). Predictive analytics helps you get that balance just right. By looking at past data and market trends, it helps you predict future demand. That means you can plan your production schedules and inventory so that you’re always ready for whatever the market throws at you—without overdoing it.
4. Can Predictive Analytics Help Me Manage Inventory Better?
Let’s be honest— too much stock, and you’re paying for storage. Too little, and you risk running out of what you need. Predictive analytics helps by giving you a heads-up on when and how much stock you’ll need. By analyzing past usage patterns, it helps you avoid the pitfalls of both overstocking and understocking, saving you money and keeping your operations running smoothly.
5. How Does Predictive Analytics Improve Product Quality?
Nobody wants to deal with faulty products or returns. With predictive analytics, you can spot issues early in the production process before they affect your final product. By monitoring data like machine performance or production conditions, predictive analytics can alert you to quality issues before they become big problems, saving time, reducing waste, and keeping your customers happy.
6. How Can Predictive Analytics Help Me Set the Right Price?
Setting the right price for your products isn’t easy, especially when market conditions change quickly. Predictive analytics helps you find the sweet spot by considering things like demand, production costs, and even competitor pricing. With real-time data, you can adjust your prices accordingly, making sure you’re competitive while still maintaining healthy margins.
7. How Can Predictive Analytics Speed Up Product Development?
Want to get your products to market faster? Predictive analytics can help by giving you insights into what customers actually want. By analyzing trends and feedback, you can refine your product designs and focus on the features that will resonate most with your audience. It’s like having a map that helps you avoid detours and get to your goal quicker.
8. How Can Automation and Robots Benefit My Factory?
Automation’s been a game-changer for manufacturing, and predictive analytics makes it even smarter. With data from sensors and AI, you can figure out exactly where automation will save you time and reduce mistakes. Whether it’s robots taking over repetitive tasks or AI helping with decision-making, predictive analytics helps ensure that automation is working for you, not against you.
9. How Do I Make Sure My Predictive Analytics System Keeps Working Well?
Once you’ve implemented predictive analytics, it’s important to keep an eye on how things are going. That means monitoring your data systems and algorithms to ensure they’re still providing accurate predictions. The good news? New tools are making it easier to manage and adjust predictive models, so even non-technical users can stay on top of things. Keeping everything in one place means quicker decisions and smoother operations.
10. What’s Next for Predictive Analytics in Manufacturing?
The future’s looking bright for predictive analytics in manufacturing. With self-serve tools, more people (even those without a data science background) can start using analytics to improve their work. Plus, we’re seeing more platforms that learn from data on their own, getting better over time without needing much manual intervention. And with new technologies like digital twins and a focus on sustainability, predictive analytics is only going to get more powerful.