Manufacturing success depends on speed, accuracy, and cost control. Yet, many businesses struggle with bottlenecks, inconsistent quality, and rising production costs. If your operations lack structure, inefficiencies creep in, slowing output and increasing expenses.
That’s where the line process transforms production. This method ensures every task follows a structured sequence, cutting waste and improving consistency. Whether you're in automotive, electronics, or large-scale manufacturing, a well-optimized assembly line can increase output, reduce errors, and maximize profitability.
Understanding how line process methods work can help your business streamline production and boost overall efficiency. Let’s break down the key elements that make this system essential for modern manufacturing.
Ready to dive into the heart of modern manufacturing? Let’s start with the backbone of production: the assembly line.
What Is an Assembly Line in Manufacturing?
An assembly line is a structured manufacturing process where a product moves through a series of workstations, with each station handling a specific task. Instead of one worker building an entire product from start to finish, the process is divided into smaller, repeatable steps. This approach saves time, reduces errors, and improves efficiency.
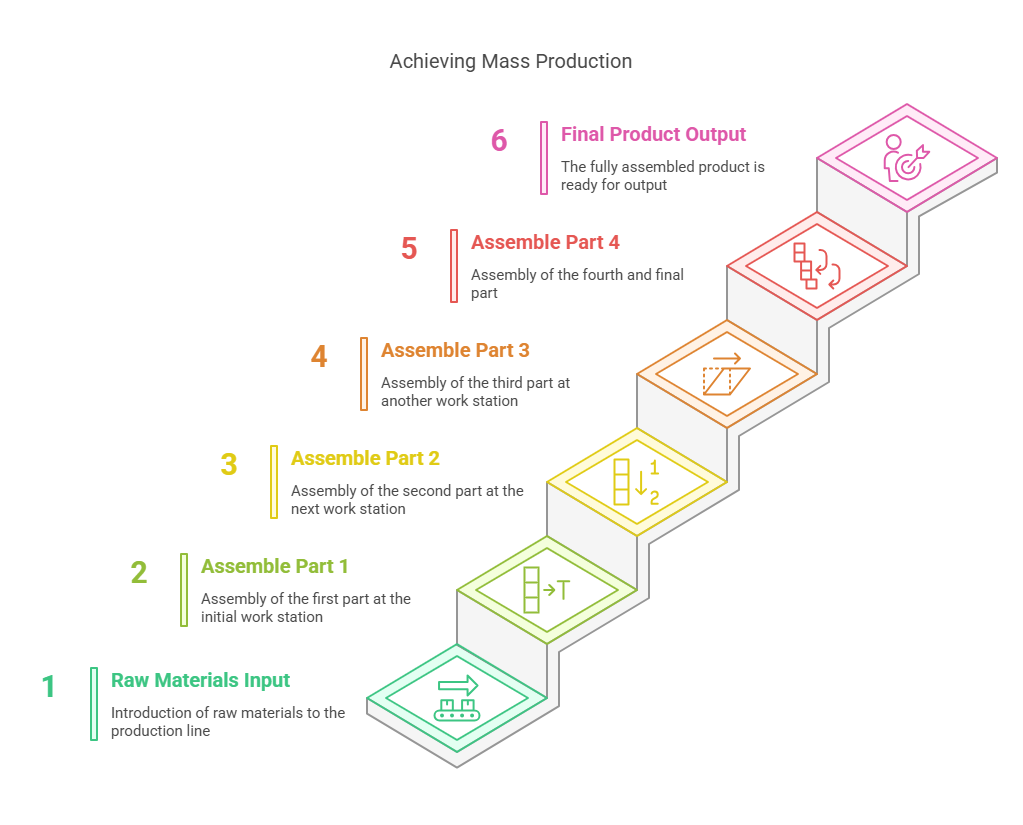
Let’s simplify the concept using an example: Imagine David owns a factory that produces smart home devices. Before using an assembly line, his workers built each device individually, leading to inconsistent quality and slow production. To fix this, David implemented a line process:
- First station: Workers attach the circuit board.
- Second station: The casing is fitted around the board.
- Third station: The device undergoes software installation.
- Fourth station: A quality check ensures everything functions correctly.
- Final station: Packaging and shipping preparation.
By breaking production into specialized steps, David’s factory now produces twice as many devices in the same amount of time. Workers focus on one task at a time, improving precision and speed.
This structured method is the backbone of modern manufacturing, used in industries ranging from automobiles to consumer electronics. When optimized, an assembly line reduces costs, minimizes defects, and keeps up with growing demand.
Now that we know what they are, let’s trace the fascinating journey of how assembly lines became what they are today.
Historical Evolution of Assembly Line Processes
The assembly line process revolutionized manufacturing, making mass production faster, cheaper, and more efficient. From early manual techniques to modern automation, this evolution has shaped industries worldwide.
Early Manufacturing Techniques
Before assembly lines, products were made one at a time by skilled artisans. Manufacturing relied on handcrafting, general-purpose tools, and labor-intensive methods. Production was slow, and quality varied based on the skill of individual workers.
During the Industrial Revolution, manufacturers introduced interchangeable parts and basic machinery, allowing for faster assembly. However, these processes still required workers to assemble entire products themselves, limiting efficiency.
Introduction of the Assembly Line
The introduction of assembly line production marked a major turning point. Instead of assembling a product from start to finish, workers specialized in specific tasks, reducing time and labor costs.
- Early 1900s: The concept of a moving assembly line emerged, cutting production time significantly.
- Mid-20th Century: Mass production expanded across industries, improving affordability and accessibility.
- Late 20th Century to Present: Automation and robotics enhanced precision and efficiency, making production even faster.
Technological Advancements
Modern assembly lines rely on cutting-edge technology to optimize production. Innovations include:
- Robotic arms and AI-driven automation for precision assembly.
- Computerized tracking systems to monitor efficiency.
- Lean manufacturing techniques to reduce waste and improve workflow.
These advancements have made assembly lines more adaptable, scalable, and cost-effective across industries.
Also Read: Deciding on In-line or Off-line Production Automation
With history in mind, let's break down the key characteristics that truly define an assembly line’s power.
Key Characteristics of Assembly Line Processes
The efficiency of an assembly line process depends on key factors like standardization, task division, continuous flow, and automation. This section breaks down how each element improves production speed, accuracy, and cost-effectiveness.
1. Standardization
Standardization ensures that each component and process follows strict guidelines. By using uniform parts and procedures, manufacturers maintain consistent quality and reduce waste. This approach allows for faster repairs, lower costs, and smoother production cycles.
2. Division of Labor
Work is divided into specialized tasks, with each worker or machine handling a specific step in the process. This method:
- Eliminates unnecessary movements and maximizes efficiency.
- Reduces training time by assigning simple, repeatable tasks.
- Speeds up production while maintaining accuracy.
3. Continuous Flow
A well-optimized assembly line operates with minimal interruptions. The continuous movement of products:
- Reduces downtime between steps.
- Minimizes bottlenecks by ensuring a steady workflow.
- Enhances production speed without sacrificing quality.
4. Automation Integration
Modern assembly lines incorporate automated systems to boost productivity. Automation plays a key role in:
- Precision manufacturing through robotics.
- Reducing labor costs and human errors.
- Increasing production speed with real-time adjustments.
But how do these characteristics translate into practical systems? Let’s explore the different types of assembly line methods
Types of Assembly Line Process Methods
Different assembly line methods suit various industries and production needs. Choosing the right approach ensures maximum efficiency, cost savings, and product consistency. Let’s explore each in detail.
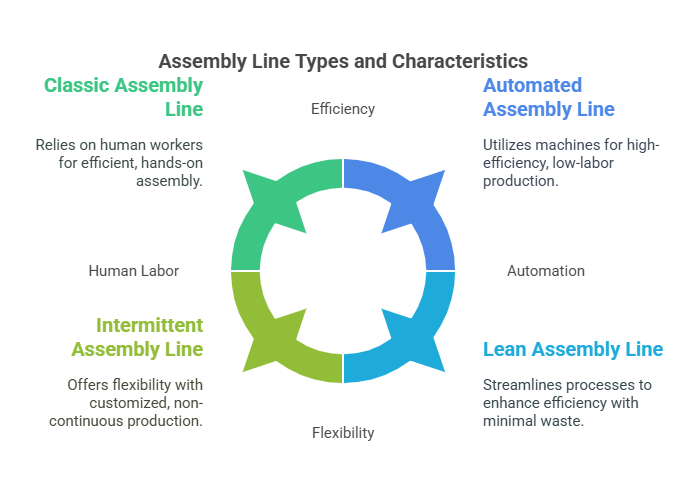
1. Fixed-Position Assembly Line
The product remains stationary in a fixed-position assembly line while workers and machines move around it. This method is common in large-scale manufacturing, where the final product is too big or complex to move easily.
For example, imagine a company assembling commercial airplanes. The aircraft stays in one location while teams install engines, wiring, and interiors. Workers specialize in specific sections, ensuring efficiency without relocating the product.
Advantages
- Best for large or heavy products that cannot be moved easily.
- Allows customization since teams work on different parts simultaneously.
- Flexible for unique or low-volume production.
Disadvantages
- Slower production speed compared to moving assembly lines.
- Requires more space for equipment and workers.
- Higher labor costs due to specialized skill requirements.
2. Product-Based Assembly Line
A product-based assembly line moves products along a structured path, with each workstation performing a specific task. This is the most common method in mass production.
For example, think about a smartphone factory. The devices move through multiple stations:
- One station installs the motherboard.
- Another attaches the screen.
- A different area tests software functionality.
- The final step is packaging.
Advantages
- Maximizes efficiency by reducing time spent on individual tasks.
- Ensures consistency with precise, repeatable steps.
- Ideal for high-volume production of identical products.
Disadvantages
- Limited flexibility—changes to product design require reconfiguring the entire system.
- Initial setup costs are high due to equipment and automation investments.
3. Process-Based Assembly Line
A process-based assembly line groups workstations by function, allowing products to move based on production needs rather than a fixed sequence. This method is common in custom or variable production environments.
For example, consider a furniture manufacturing plant. A wooden chair might go to one station for cutting, another for painting, and another for upholstery, depending on the order’s specifications. The sequence can change based on design variations.
Advantages
- Great for custom or specialized products that don’t follow a fixed sequence.
- Efficient use of machines and labor, as stations work on multiple products.
- Allows for more product variations without major system changes.
Disadvantages
- Slower than product-based assembly lines since items follow different paths.
- More complex logistics to manage workflows efficiently.
- Requires skilled workers to handle diverse tasks.
The beauty of assembly lines lies in their versatility. See how industries across the board are benefiting from them.
Applications Across Industries
Assembly line processes are essential in industries where speed, accuracy, and scalability matter. They enable businesses to produce high volumes without sacrificing quality.
1. Automotive Industry
Every car on the road today was likely built on an assembly line. Vehicles move from frame welding to engine installation and final inspections, ensuring mass production with consistent quality.
2. Electronics Manufacturing
Smartphones, laptops, and televisions rely on precision assembly lines to install delicate components efficiently. Without these methods, electronics would be far more expensive.
3. Pharmaceuticals and Textiles
Medicine production follows strict automated assembly processes, ensuring each dose is measured, packaged, and labeled accurately. In textiles, automated sewing lines enable brands to produce thousands of garments daily.
Could your industry benefit from an optimized assembly line? Understanding the right method could reduce costs and improve efficiency.
Of course, it’s not all smooth sailing. Let’s dive into the major perks that come with assembly line methods.
Advantages of Assembly Line Processes
A well-designed assembly line process isn’t just about making things faster—it’s about working smarter. Breaking production into clear, repeatable steps ensures that every part of the process runs efficiently, from the first component to the finished product. So, let’s go over the most prominent advantages.
1. Gets More Done in Less Time
When workers and machines focus on one specific task at a time, everything moves faster. Instead of shifting between different jobs, employees become highly skilled at their role, and automated systems keep production moving without interruptions. This setup leads to higher output with fewer errors.
2. Reduces Production Costs
Hiring and training workers for every step of production can be expensive. An assembly line lets businesses streamline labor, with each worker specializing in a single, efficient task. Automation further cuts costs by reducing mistakes and material waste, keeping expenses low without sacrificing quality.
3. Ensures Every Product is Built Right
Nobody likes getting a defective product. Assembly lines remove inconsistencies by making sure every item follows the same exact process. With fewer human errors, businesses see higher-quality products, fewer returns, and more satisfied customers.
4. Adapts to Market Demands Quickly
Consumer trends change fast, and companies that can’t keep up risk falling behind. With a well-structured assembly line, manufacturers can increase production during high demand or introduce new products without completely overhauling their process. This flexibility keeps them competitive and ready for what’s next.
5. Makes Work More Efficient for Employees
Instead of overwhelming workers with complex tasks, an assembly line lets them master a specific role. This not only improves accuracy but also reduces fatigue, making jobs easier to learn and perform. As a result, businesses get more done with a focused and efficient workforce.
6. Creates a Safer Work Environment
A messy, unorganized workspace leads to accidents. Assembly lines reduce risks by keeping workflows structured and eliminating unnecessary movement. With automation handling dangerous or repetitive tasks, workers stay safer and more productive in the long run.
Also Read: Top 10 Manufacturing Analytics Software and How It Works
With efficiency comes responsibility. Here’s why ergonomics and safety can’t be overlooked in an assembly line setting.
Ergonomics and Worker Safety in Assembly Lines
In assembly line environments, worker safety and comfort are top priorities. The repetitive nature of assembly line tasks can put employees at risk for musculoskeletal injuries, especially when ergonomics aren’t considered.
1. The Importance of Ergonomic Design
Ergonomics in the workplace is about designing tasks and workstations that fit the worker’s body and abilities. In an assembly line, this means adjusting heights, angles, and tool placements to reduce strain. Proper ergonomic design prevents injuries and allows workers to stay comfortable and productive throughout long shifts.
2. Risks of Repetitive Motion Injuries
Repetitive motion injuries (RMIs) are common in assembly lines, where workers perform the same action repeatedly. Over time, this can lead to muscle strains, joint problems, and even chronic pain. Preventing RMIs requires task rotation, adjustable workstations, and the use of assistive tools to reduce repetitive strain.
3. Technology Enhancing Worker Safety
Technology plays a major role in improving worker safety on assembly lines. Robotics and automation can take over the most physically demanding tasks, reducing human exposure to risks. Moreover, smart sensors and wearables can track the worker’s movements and posture, sending alerts when potential risks are detected, ensuring proactive safety measures are taken.
Maintaining balance on the line is essential. Let’s look at how assembly line balancing keeps production running smoothly.
Assembly Line Balancing Techniques
A key to optimizing any assembly line is ensuring that each workstation has a balanced workload. Assembly line balancing involves distributing tasks evenly to avoid bottlenecks, ensuring smooth, continuous production.
The goal of line balancing is to distribute tasks equally among workstations, so no station becomes overloaded or underutilized. This is crucial for maintaining a steady pace and ensuring maximum efficiency. When tasks are unevenly distributed, some workstations may be idle while others become overwhelmed, slowing down production.
Here are the techniques for balancing tasks
- Cycle Time Analysis: This method ensures that each station completes its tasks in the same amount of time, aligning with the overall cycle time of the assembly line.
- Task Grouping: Involves grouping similar tasks together to make the work process more streamlined and minimize worker movement.
- Workload Optimization: Managers evaluate tasks and assign them to workstations based on worker skills and machine capabilities, ensuring tasks are as efficiently distributed as possible.
And when speed really matters? SMED ensures you maximize efficiency by reducing setup times to a minimum.
Single-Minute Exchange of Die (SMED) in Assembly Lines
The Single-Minute Exchange of Die (SMED) methodology focuses on reducing setup times between production runs, allowing manufacturers to switch production lines quickly and maintain high flexibility.
.png)
SMED is a method designed to cut changeover times to less than 10 minutes (hence "single minute"). This approach focuses on breaking down changeover tasks into two categories:
- Internal Tasks: Tasks that can only be done when the machine is stopped.
- External Tasks: Tasks that can be done while the machine is running.
By converting as many internal tasks to external tasks as possible, SMED minimizes downtime and allows for faster transitions between different production runs.
Why SMED Matters?
- Increased Flexibility: With reduced setup times, companies can produce smaller batches of different products without long downtimes.
- Higher Production Capacity: Faster changeovers mean more time spent on actual production, increasing overall output.
- Cost Reduction: Reducing setup times decreases machine idle time, helping to cut operational costs and improve resource utilization.
Implementing SMED
- Standardized Processes: Having clear procedures for each setup step ensures that changeovers are completed as efficiently as possible.
- Tooling Improvements: Streamlining or improving tooling systems can dramatically speed up the changeover process.
- Training Employees: Well-trained workers are key to implementing SMED successfully. Their ability to quickly and accurately complete each changeover step reduces mistakes and downtime.
As we push the boundaries, let’s see how Industry 4.0 is taking assembly lines into the future.
Impact of Industry 4.0 on Assembly Lines
Industry 4.0, known as the Fourth Industrial Revolution, is transforming how assembly lines operate. By incorporating advanced technologies like the Internet of Things (IoT), big data, and robotics, assembly lines are becoming smarter, more connected, and more efficient than ever before.
1. Smart Factories and Connected Assembly Lines
Smart factories integrate cyber-physical systems that allow for real-time data exchange between machines, sensors, and workers. These connected systems enable better decision-making, predictive maintenance, and optimization of production flows, leading to reduced downtime and increased efficiency.
2. Cyber-Physical Systems in Assembly Lines
Cyber-physical systems (CPS) are the backbone of Industry 4.0 in assembly lines. They merge the physical and digital worlds, allowing machines and sensors to communicate with each other. For example, a machine can automatically adjust its operations based on data from connected sensors, ensuring consistent product quality and performance while minimizing errors and waste.
AI is now a game changer. Find out how integrating AI can optimize and transform your assembly line processes.
Integration of Artificial Intelligence in Assembly Lines
Artificial Intelligence (AI) is revolutionizing the future of assembly lines by making them more autonomous and intelligent. AI systems use advanced data analytics and machine learning algorithms to make real-time decisions that were once left to human operators.
1. Improving Efficiency with AI
AI can optimize workflows by analyzing patterns in production data. It predicts maintenance needs, detects anomalies, and suggests adjustments to improve operational efficiency. With AI-powered robots and machines, assembly lines can become faster, smarter, and capable of handling complex tasks autonomously.
2. Enhancing Quality Control
AI also plays a critical role in quality assurance. By analyzing images and data in real time, AI can identify defects or inconsistencies that might go unnoticed by human workers. This ensures that every product meets the desired standards before moving to the next stage of production.
With technology driving progress, let’s not forget the need for sustainability in modern assembly lines.
Sustainable Manufacturing Practices
As environmental concerns grow, industries are turning toward eco-friendly practices in manufacturing. The shift toward sustainable production methods not only helps reduce environmental impact but also boosts efficiency and long-term profitability.
1. Energy-Efficient Systems
Modern assembly lines are using energy-efficient technologies to cut down on power consumption. Smart sensors and automation systems can monitor energy usage in real time, reducing waste and improving the sustainability of operations.
2. Waste Reduction and Recycling
Sustainability also involves minimizing waste generated during the production process. Technologies like 3D printing and advanced robotics help reduce material waste by allowing for more precise manufacturing and better recycling of leftover materials.
Flexibility is key. Let’s explore how assembly lines are becoming increasingly adaptable to customer needs.
Customization and Flexibility in Assembly Lines
Today's market demands customized products at faster speeds, which means assembly lines must become more adaptable. Flexible manufacturing systems (FMS) and modular production lines are making it possible to produce smaller batches of diverse products without sacrificing speed or quality.
1. Adapting to Customer Demand
With modular assembly lines, manufacturers can switch production setups to accommodate a range of products. This flexibility allows for rapid adjustments in response to changing customer demands, reducing lead times and improving customer satisfaction.
2. Personalized Products
As consumer preferences move toward personalized products, assembly lines are incorporating more customization options. Through advanced automation and robotics, manufacturers can offer made-to-order items at mass production prices.
However, it’s not all perfect. Let's tackle the challenges and limitations that come with assembly line processes.
Challenges and Limitations
Assembly lines offer benefits, but they also come with challenges. These can impact financial investment, flexibility, and worker satisfaction. Here's a breakdown:
1. High Initial Setup Costs
Setting up an assembly line involves high upfront costs, including machinery, training, and facility upgrades. Businesses often face significant financial barriers, especially smaller companies.
Customizing equipment or expanding infrastructure adds to the expenses. While efficiency improves long-term, it can take years to recover the initial investment. The capital-intensive nature of assembly lines may deter smaller businesses or those with tighter budgets.
2. Flexibility Constraints
Assembly lines are difficult to reconfigure for new products. Changing the setup often requires reprogramming machines and retraining workers, which leads to downtime. The rigid structure makes it tough to customize products or shift production without significant adjustments.
Adapting quickly to new trends or small-batch production can be costly and time-consuming, making it a challenge for companies with ever-changing market demands.
3. Worker Satisfaction
Repetitive tasks on an assembly line can lead to monotony, reducing employee engagement. Performing the same task repeatedly can cause boredom and fatigue, impacting morale. Stress from high-performance expectations also adds to job dissatisfaction.
The limited variation in roles can hinder worker development and long-term retention. While some enjoy specialized tasks, many employees find such a work environment less fulfilling.
But fear not! INSIA’s data-driven analytics is the solution to fine-tuning and overcoming those hurdles for ultimate efficiency.
Optimize Assembly Line Performance: Data-Driven Process Control with INSIA Analytics
INSIA transforms assembly line management by providing real-time insights that streamline operations, improve performance, and eliminate inefficiencies. By centralizing data from diverse sources, INSIA enables businesses to make informed decisions and boost productivity.
1. Real-Time Process Monitoring
INSIA helps manufacturers monitor production performance in real-time. By tracking key metrics, you get immediate feedback on line efficiency, potential bottlenecks, and production rates, allowing for quick adjustments.
- Line Efficiency Tracking: Monitor how each workstation is performing. INSIA helps identify underperforming areas so you can quickly address them and maximize throughput.
- Bottleneck Identification: Pinpoint bottlenecks in real time. INSIA tracks where delays are occurring, giving you the tools to resolve issues immediately.
- Cycle Time Analysis: Track cycle times across all workstations. INSIA helps you spot inefficiencies that slow down production and lets you optimize time across the board.
- Production Rate Monitoring: Keep track of production rates to ensure you hit targets. INSIA offers continuous monitoring that helps you stay on track with optimal performance.
2. Assembly Line Analytics
INSIA provides deep insights into every stage of the production process. By analyzing station-level performance, workflow efficiency, and resource utilization, you can identify areas for improvement and make data-backed decisions.
- Station-by-Station Analysis: Understand how each station contributes to the overall process. INSIA lets you see detailed performance metrics at every step, helping you make targeted improvements.
- Workflow Visualization: Visualize the entire production flow. INSIA helps you see how tasks move across the line and identifies areas of inefficiency.
- Resource Utilization Tracking: Get detailed insights into how resources are used. INSIA tracks how materials, equipment, and labor are allocated, making it easier to optimize resources.
- Quality Control Metrics: Use INSIA to monitor quality at every stage of production. By tracking key metrics, you can catch issues early and improve overall product quality.
3. Predictive Assembly Insights
INSIA uses predictive analytics to forecast future trends and optimize your processes. By anticipating demand and identifying potential issues, INSIA helps you stay ahead of the curve and maintain consistent, high-quality production.
- Push AI for Process Optimization: INSIA’s AI-driven insights alert you when action is needed, helping you stay proactive in managing operations and avoiding downtime.
- Production Forecasting: Forecast production needs with confidence. INSIA helps predict future demand, allowing for better resource allocation and smoother operations.
- Resource Planning: Ensure you have the right resources at the right time. INSIA provides predictive resource planning, helping you avoid shortages or excess inventory.
- Quality Predictions: Predict quality issues before they occur. INSIA uses AI-powered predictions to catch potential defects early, ensuring high-quality output.
4. Multi-Source Data Integration
INSIA integrates with a wide range of data sources to create a single source of truth. By connecting your ERP systems, quality management tools, and other data sources, INSIA ensures all your data is in one place for better decision-making.
- ERP System Connection: Seamlessly connect with existing ERP systems for real-time data updates. INSIA centralizes your data for more accurate and timely decisions.
- Production Data Consolidation: Bring together data from all your production systems into one platform. INSIA simplifies data management and provides a clearer view of operations.
- Quality System Integration: INSIA connects your quality management systems, ensuring that quality data is integrated with production data for real-time quality insights.
- Resource Management Data: Align your resource data with production needs. INSIA helps you track resource allocation and optimize your workflows.
5. Manufacturing Evidence
INSIA’s impact is evident in its success stories. Companies like Trident Services, Crescent Foundry, and Kirloskar Oil Engines have seen significant improvements in efficiency, reporting, and decision-making by leveraging INSIA’s platform.
- Trident’s Automated Reporting: Trident reduced their report generation time by 70% and automated 90% of their reporting processes, leading to faster, more informed decisions.
- Crescent Foundry’s Transparency: With INSIA, Crescent Foundry gained full visibility into their operations, reducing reporting costs by 40% and improving time-to-insight by 50%.
Conclusion
INSIA is a powerful data integration and analytics platform designed to optimize assembly line performance. With its real-time monitoring, predictive insights, and seamless data integration, INSIA empowers businesses to make smarter, faster decisions that drive efficiency and quality in production.