The manufacturing industry faces an ongoing battle—maximizing efficiency while reducing costs and downtime. Traditional operations struggle with outdated systems, unexpected equipment failures, and fragmented data, leading to costly delays and inefficiencies. IoT solutions for manufacturing are transforming the industry by bridging these gaps, providing real-time visibility, and enabling data-driven decision-making.
From predictive maintenance that eliminates unplanned downtime to automated production lines that boost efficiency, manufacturers leveraging IoT solutions for manufacturing gain a competitive edge. The ability to monitor, analyze, and optimize operations in real time allows businesses to scale faster, reduce waste, and enhance workplace safety.
But how exactly does IoT drive these results? Let’s break down the most impactful applications, use cases, and key benefits—so you can determine how this technology fits into your manufacturing strategy.
Understanding IoT’s potential is just the start—let’s explore how it integrates into manufacturing to create smarter, more connected factories.
Overview of IoT in Manufacturing
Keeping a manufacturing plant running smoothly is no small task. Machines wear out, supply chains fluctuate, and unexpected breakdowns can bring production to a halt. IoT solutions for manufacturing are changing that by making operations more connected, intelligent, and predictive.
At its core, IoT in manufacturing involves a network of sensors, devices, and software that collect and analyze real-time data from machines and production lines. Instead of relying on routine maintenance schedules or reacting to problems as they arise, IoT helps manufacturers predict failures before they happen, automate processes, and optimize efficiency.
For example, imagine a mid-sized electronics manufacturer, SwiftTech Industries. They used to struggle with unexpected machine failures, leading to costly delays. Their maintenance team relied on manual inspections, often missing early warning signs. After integrating IoT solutions for manufacturing, their machines were equipped with smart sensors that monitored temperature, vibration, and performance trends. When one of their machines started showing irregular vibrations, the system instantly sent an alert, allowing the team to replace a worn-out part before it caused downtime.
This shift toward smarter, data-driven manufacturing isn’t just a trend—it’s shaping the future of the industry. In fact, the Internet of Things (IoT) market in manufacturing is projected to grow from USD 0.49 trillion in 2025 to USD 1.51 trillion by 2030, expanding at a CAGR of 25.33%. As more manufacturers embrace IoT, those who fail to adopt these technologies risk falling behind in an increasingly competitive market.
Also Read: Understanding Overall Equipment Effectiveness (OEE) in Manufacturing
Now that we’ve defined IoT in manufacturing, let’s break down the measurable advantages that make it a game-changer for businesses.
Key Benefits of IoT in Manufacturing
Manufacturers face constant pressure to increase efficiency, reduce costs, and minimize downtime. IoT solutions for manufacturing address these challenges by connecting machines, sensors, and analytics platforms to optimize operations, predict failures, and improve productivity.
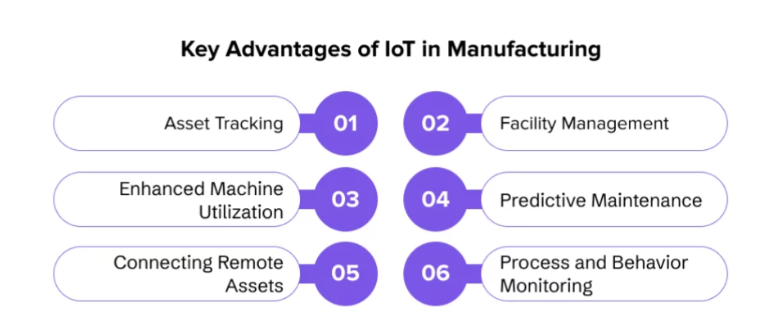
Here’s how IoT is reshaping manufacturing and delivering real business value:
Greater Operational Efficiency
IoT enables real-time monitoring and automation, reducing reliance on manual oversight. With smart sensors and AI-driven robotics, manufacturers can optimize tasks like assembly, inspection, and inventory management. These systems identify inefficiencies and correct errors instantly, improving throughput and reducing waste.
Predictive Maintenance to Avoid Downtime
Unexpected equipment failures lead to costly production delays. IoT prevents this by continuously monitoring machine performance, temperature, and vibration levels. Manufacturers may have to pay up to $260,000 per hour for these unplanned downtime occurrences, and Industry EMEA estimates that these problems cost them over $50 billion a year. When irregularities arise, the system sends alerts, allowing maintenance teams to fix issues before they cause breakdowns. This extends equipment lifespan and prevents revenue loss.
Higher Product Quality with Fewer Defects
IoT-powered automated quality control ensures that defects are detected immediately. Smart cameras and sensors analyze products with more accuracy than human inspectors, reducing almost 65% of recalls and waste. By maintaining strict quality standards, manufacturers improve customer trust and product reliability.
Improved Workplace Safety
Hazardous tasks and manual labor risks are significantly reduced with IoT. Wearable sensors, smart helmets, and automated monitoring systems detect unsafe conditions and alert workers in real time. Additionally, IoT-driven compliance tracking helps ensure adherence to safety regulations, minimizing workplace incidents.
Cost Optimization and Resource Management
By automating repetitive tasks, IoT helps manufacturers lower labor costs and improve resource allocation. Predictive analytics further reduces expenses by preventing unnecessary service calls and emergency repairs. Remote monitoring also cuts travel and operational costs, enhancing overall efficiency.
Scalability for Future Growth
Scaling production traditionally requires more staff, larger facilities, and costly upgrades. IoT enables flexible, data-driven scaling, allowing manufacturers to adjust production levels, optimize supply chains, and integrate new technologies without major disruptions.
These benefits aren’t just theoretical—real-world manufacturers are leveraging IoT in specific ways to drive efficiency and reduce downtime.
IoT Use Cases in Manufacturing
The rise of IoT solutions for manufacturing is reshaping the industry by enabling real-time monitoring, predictive maintenance, and automated production processes. Manufacturers can boost efficiency, minimize downtime, and improve product quality by integrating smart sensors, data analytics, and cloud connectivity. Let’s explore some of the most impactful applications of IoT in modern manufacturing.
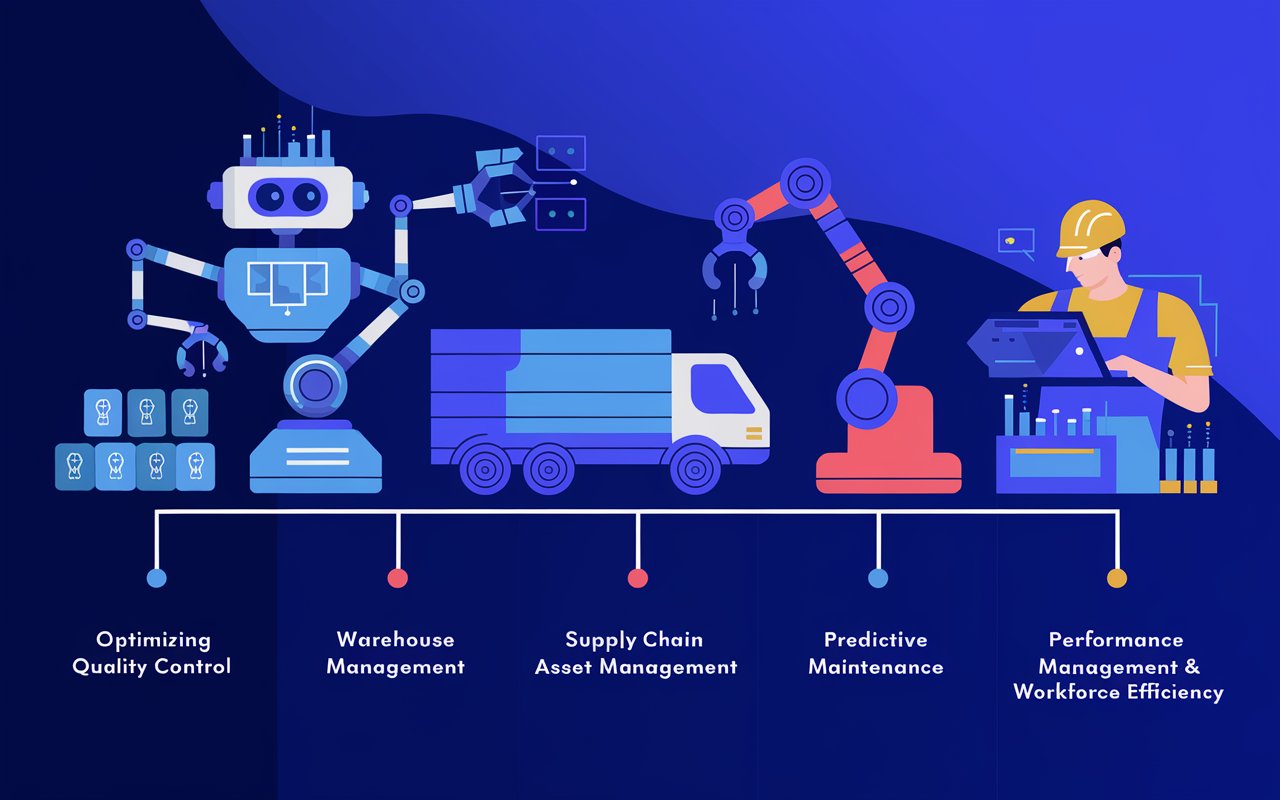
Smarter Quality Control
Maintaining consistent product quality requires precise monitoring of various environmental and mechanical factors. Temperature, humidity, air quality, and pressure fluctuations can significantly impact production reliability. For instance, excess humidity can lead to:
- Inaccurate testing results
- Material degradation
- Higher energy consumption
Traditional quality control relied on manual inspections, which were prone to human error. With IoT-driven monitoring, manufacturers can now track real-time quality metrics, ensuring compliance with industry standards such as ISO and GMP. Smart sensors detect deviations instantly, allowing manufacturers to identify potential defects before products reach the market.
Warehouse Management with IoT
As consumer demand grows and supply chains become more complex, efficient warehouse management is more critical than ever. Many companies invest heavily in storage and logistics but fail to address key challenges such as:
- Cost control
- Operational speed
- Capacity planning
- Logistics complexity
IoT-powered inventory tracking provides complete visibility across the supply chain, ensuring materials and products are accounted for at all times. When an inventory issue arises, automated alerts notify warehouse managers before it disrupts production. This enables faster decision-making and prevents costly bottlenecks.
Supply Chain Asset Tracking
A seamless supply chain is essential for meeting production goals. IoT technology enables manufacturers to track raw materials and finished goods throughout the production and delivery process, offering real-time insights into supply chain performance.
For example, if a critical raw material shipment is delayed, IoT monitoring helps management pinpoint the issue and take corrective action immediately. By identifying and addressing potential slowdowns before they escalate, manufacturers can reduce production delays and lower costs.
Predictive Maintenance to Reduce Equipment Failures
Traditional maintenance models rely on time-based schedules, but research shows that 82% of equipment failures occur unpredictably—not due to age. This highlights the inefficiency of scheduled maintenance and the need for a more data-driven approach.
IoT-powered predictive maintenance uses sensors to monitor equipment performance, temperature fluctuations, and mechanical wear. Instead of following rigid maintenance schedules, manufacturers can assess actual wear and tear, triggering service only when necessary.
For example, in steel production, furnaces rely on water-cooled panels to maintain stable temperatures. If a leak occurs in these panels, it can cause serious safety hazards and halt production. With IoT-based monitoring, plant managers receive early warnings of leaks or irregularities, allowing them to address issues before they lead to costly downtime.
Performance Management and Workforce Productivity
IoT provides deep insights into production efficiency, enabling manufacturers to optimize machine performance, workflow efficiency, and workforce allocation. By reducing downtime and improving resource utilization, businesses can significantly cut operational costs.
With real-time data collection, companies can:
- Optimize equipment efficiency by minimizing disruptions
- Develop continuous improvement strategies using performance analytics
- Reduce waste and energy consumption through smarter resource management
Additionally, automation allows workers to focus on higher-value tasks instead of repetitive, time-consuming work. This shift leads to increased job satisfaction, improved productivity, and better overall business outcomes.
Also Read: A Guide on Data-Driven Manufacturing: Benefits, Challenges and Strategies
To see these IoT applications in action, let’s examine the key components that power smart, connected manufacturing environments.
Components of IoT in Manufacturing
The Industrial Internet of Things (IIoT) relies on multiple interconnected technologies to drive efficiency, automation, and data-driven decision-making in manufacturing. These components work together to collect, transmit, analyze, and act on data, enabling smarter production processes.
1. Smart Assets and Sensors for Data Collection
At the heart of IoT in manufacturing are smart sensors and connected devices that capture real-time operational data. These sensors monitor machine performance, environmental conditions, energy consumption, and production flow, providing continuous insights that help manufacturers optimize processes.
For example, in an assembly line, temperature and vibration sensors detect anomalies in machinery before failure occurs. By tracking these metrics in real time, maintenance teams can schedule repairs proactively, preventing costly downtime.
2. Data Communication Infrastructure
Once data is collected, it must be transmitted securely and efficiently for analysis. Modern manufacturing relies on high-speed networks like 5G and cloud-based platforms to ensure seamless data flow across factories, supply chains, and remote locations.
Why It Matters:
- 5G enables ultra-fast, low-latency communication, essential for real-time monitoring and automated decision-making.
- Cloud storage ensures scalability, allowing businesses to store and access massive datasets from anywhere.
- Edge computing processes data closer to its source, reducing response times for critical operations like predictive maintenance.
3. Software and Analytics for Decision-Making
Raw data is only valuable if it leads to actionable insights. AI-powered analytics platforms process IoT data to identify patterns, predict failures, and optimize workflows.
For example, an AI-driven system analyzes historical production data to forecast demand spikes. Manufacturers can then adjust production schedules and resource allocation accordingly, minimizing waste and maximizing output.
4. Human Interaction and IoT Integration
Despite automation, human oversight remains essential in IoT-driven manufacturing. Workers interact with IoT dashboards, wearables, and smart alerts, using the data to make informed decisions and optimize operations.
How It Enhances Productivity:
- Supervisors receive automated alerts when production inefficiencies arise, allowing quick intervention.
- Operators monitor machine health through digital dashboards, reducing manual inspections.
- Wearable IoT devices improve safety by tracking worker fatigue and posture.
By combining automation with human expertise, manufacturers achieve the best balance of efficiency, safety, and quality control.
With the right IoT components in place, manufacturers can remotely monitor and control operations, ensuring seamless production and minimal downtime.
Remote Monitoring and Control in Manufacturing
The ability to remotely monitor and control equipment is one of the most significant advantages of IoT in manufacturing. With real-time connectivity, manufacturers can oversee production lines, troubleshoot issues, and optimize performance—no matter where they are.
Here’s how IoT enables remote monitoring:
IoT sensors continuously track machine status, energy consumption, and operational efficiency. This data is transmitted to a centralized dashboard, where managers and technicians can monitor performance and take immediate action if an issue arises.
Key Benefits of Remote Monitoring:
- Reduced Downtime: Alerts notify teams about irregularities before they lead to breakdowns.
- Improved Efficiency: Production bottlenecks can be identified and resolved remotely.
- Lower Maintenance Costs: Predictive analytics ensure timely repairs, avoiding costly emergencies.
Furthermore, during events like global pandemics, supply chain disruptions, or extreme weather conditions, on-site supervision may be limited or unsafe. IoT enables manufacturers to maintain operational visibility without physical presence.
For example, a factory facing travel restrictions during a pandemic uses remote IoT dashboards to monitor production. When a critical machine shows signs of overheating, the system triggers an automated shutdown and maintenance request, preventing severe damage.
Implementing IoT is an investment—so how do manufacturers measure its impact? Let’s dive into ROI calculations and performance tracking.
ROI of IoT in Manufacturing: Measuring Success
Investing in IoT solutions for manufacturing requires a clear understanding of return on investment (ROI). To determine whether an IoT project is delivering value, manufacturers must track key performance indicators (KPIs), measure cost savings, and assess productivity gains.
1. Framework for Calculating IoT ROI
To calculate ROI, businesses should evaluate the following metrics:
- Initial Investment Costs
- IoT hardware (sensors, devices, connectivity)
- Software and analytics platforms
- Implementation and training expenses
- Operational Cost Reductions
- Savings from predictive maintenance (fewer repairs and machine failures)
- Lower labor costs due to automation
- Reduced energy consumption with smart resource management
- Productivity and Efficiency Gains
- Reduction in unplanned downtime
- Faster production cycles due to real-time monitoring
- Improved quality control, resulting in fewer defective products
- Revenue Growth and Competitive Advantage
- Higher customer satisfaction from better product quality
- Faster time-to-market for new products
- Improved ability to scale production based on market demand
2. Tracking IoT Project Performance
To ensure long-term success, manufacturers must continuously track IoT project outcomes. Establishing KPIs helps measure performance and optimize IoT strategies over time.
Key KPIs to Track:
- Equipment Uptime: Has predictive maintenance reduced machine failures?
- Production Output: Are IoT-driven optimizations improving manufacturing speed?
- Energy Efficiency: Has IoT reduced power consumption and operating costs?
- Quality Assurance: Has defect detection improved with real-time monitoring?
- Cost Savings: Are automation and efficiency gains leading to measurable savings?
Despite its advantages, IoT adoption isn’t without hurdles. Here’s what manufacturers must overcome to fully capitalize on its potential.
IoT Challenges in Manufacturing
While IoT brings immense value to manufacturing, successful implementation requires careful planning, security measures, and seamless integration with existing systems. Choosing the right IoT solution provider ensures a scalable, secure, and efficient deployment. However, manufacturers must navigate several key challenges when adopting IoT-driven solutions.
1. Security Risks: Protecting Industrial IoT from Cyber Threats
Security remains one of the biggest concerns in industrial IoT. If cybercriminals gain access to IoT-connected systems, they can steal or manipulate critical operational data, potentially disrupting production and affecting product quality. For industries like healthcare, defense, and critical infrastructure, a security breach can have severe financial and regulatory consequences.
Additionally, IoT devices that are not regularly updated become vulnerable to attacks, which can result in downtime, data breaches, and reputational damage. To mitigate these risks, manufacturers must implement strong encryption, regular security updates, and strict access controls.
2. Interoperability: Integrating IoT with Existing Systems
Manufacturing environments rely on a mix of legacy equipment and modern technology, making IoT integration complex. With multiple platforms, communication protocols, and device standards, ensuring seamless interoperability can be challenging.
To avoid compatibility issues, manufacturers must evaluate IoT platforms carefully, ensuring they work with existing IT infrastructure, automation systems, and industrial protocols. Standardized IoT frameworks and working with experienced systems integrators can help bridge gaps between different technologies.
3. Data Privacy: Securing Sensitive Information
By connecting IoT sensors and devices to the internet, manufacturers become more exposed to cyber threats that can compromise confidential production data, proprietary designs, and operational insights. Unauthorized access to this data can lead to competitive risks, compliance violations, and legal consequences.
To minimize data privacy vulnerabilities, businesses should:
- Use end-to-end encryption to protect sensitive information
- Implement role-based access controls to limit unauthorized data access
- Ensure compliance with industry data protection regulations
4. Private Networks: A Secure Solution for IoT Challenges
One way to address security, interoperability, and data privacy concerns is by deploying a private network. Many manufacturers are adopting private 5G or LTE networks to create a secure, dedicated environment for IoT operations.
Benefits of Private Networks for IoT:
- Stronger Security: Limits external access, reducing the risk of cyberattacks.
- Improved Reliability: Ensures better network performance and quality of service.
- Greater Control: Allows businesses to manage data flow, security policies, and access permissions more effectively.
By implementing private networks, manufacturers can enhance IoT security, optimize device communication, and improve operational efficiency, ensuring a resilient and future-proof industrial IoT strategy.
Also Read: Predictive Analytics in Manufacturing: Use Cases, Tips and Benefits
While challenges exist, IoT is evolving rapidly. Let’s explore the future trends that will shape the next wave of smart manufacturing.
Future Trends in IoT for Manufacturing
The evolution of IoT in manufacturing continues to accelerate, with emerging technologies enhancing automation, efficiency, and data-driven decision-making. As manufacturers seek faster, smarter, and more secure operations, the integration of AI, 5G, edge computing, and blockchain is shaping the future of industrial IoT.
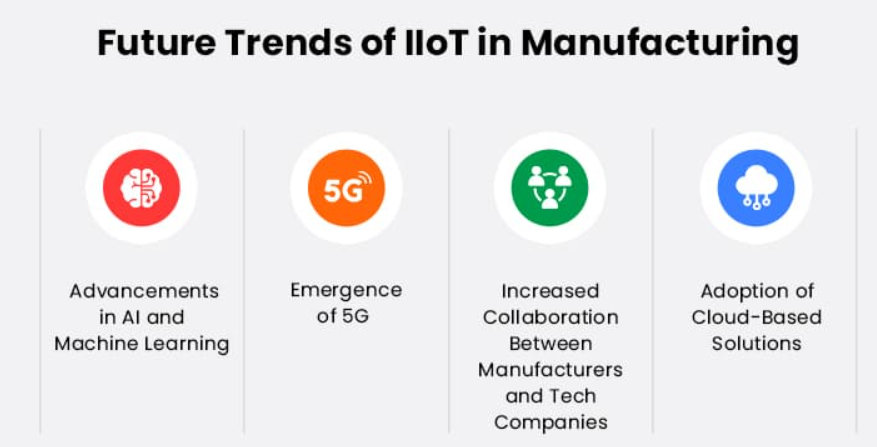
- AI and Machine Learning: Smarter Manufacturing with IoT
The combination of IoT and artificial intelligence (AI) is revolutionizing how manufacturers analyze data, optimize production, and predict failures. Machine learning algorithms process vast amounts of IoT-generated data to identify patterns, anomalies, and efficiency improvements—all in real time.
How AI Enhances IoT in Manufacturing:
- Predictive Maintenance: AI analyzes IoT sensor data to forecast machine failures before they happen, minimizing downtime.
- Process Optimization: Smart algorithms adjust production workflows dynamically based on real-time conditions.
- Automated Quality Control: AI-powered vision systems detect defects and inconsistencies faster than manual inspections.
By integrating AI with IoT, manufacturers can reduce waste, improve accuracy, and boost operational agility, making processes more intelligent and self-optimizing.
- 5G Connectivity: Unlocking the Full Potential of IoT
The adoption of 5G networks in manufacturing is transforming IoT performance, speed, and reliability. Compared to traditional networks, 5G offers ultra-low latency, higher bandwidth, and more stable connections, allowing IoT devices to communicate in real time with minimal delays.
Key Benefits of 5G in IoT Manufacturing:
- Faster Data Transmission: Enables instant analytics and decision-making for critical production processes.
- Improved Device Connectivity: Supports thousands of IoT sensors per square kilometer, ensuring seamless integration across facilities.
- Remote Operations: Enables real-time monitoring and control of machinery from anywhere, enhancing productivity and flexibility.
With 5G-powered IoT, manufacturers can achieve greater automation, optimize resource allocation, and drive next-level efficiency.
- Edge Computing: Processing IoT Data Closer to the Source
Traditional cloud-based IoT systems often experience latency issues and network congestion when handling large volumes of data. Edge computing solves this by processing data locally—at the edge of the network, closer to IoT devices.
Why Edge Computing Matters in IoT:
- Faster Response Times: Critical machine data is processed instantly, reducing delays in automated adjustments and alerts.
- Lower Bandwidth Usage: Only essential data is sent to the cloud, reducing network strain and improving efficiency.
- Enhanced Security: Keeping data on-site minimizes exposure to cyber threats and strengthens data privacy.
For manufacturers dealing with high-speed production lines or real-time quality control, edge computing ensures quick decision-making and operational stability without reliance on external servers.
- Blockchain for Secure and Transparent Supply Chains
As manufacturing supply chains grow more complex, ensuring transparency, security, and authenticity becomes a challenge. Blockchain technology, when combined with IoT, offers a decentralized and tamper-proof ledger to track materials, transactions, and product movements with full visibility.
How Blockchain Enhances IoT in Manufacturing:
- End-to-End Supply Chain Transparency: Each product or component is tracked with an immutable record of its origin, movement, and status.
- Fraud Prevention & Security: Transactions and production logs cannot be altered, reducing risks of counterfeiting or unauthorized modifications.
- Automated Compliance Tracking: Smart contracts ensure real-time verification of regulatory standards at every stage.
By integrating blockchain with IoT, manufacturers can increase trust, enhance traceability, and streamline logistics, making supply chains more resilient and efficient.
Trends point toward a data-driven future, but actionable insights matter most. Here’s how INSIA turns IoT data into real intelligence.
From IoT Data to Manufacturing Intelligence: Unlock Hidden Insights with INSIA's Analytics Platform
Manufacturers generate vast amounts of IoT data, but without a system to integrate, analyze, and act on it, valuable insights go untapped.
INSIA.ai provides a centralized analytics platform that turns raw IoT data into actionable intelligence, helping businesses improve efficiency, predict failures, and enhance decision-making.
Here’s how INSIA revolutionizes manufacturing intelligence:
- Real-Time Data Integration: Unifying IoT Data Across Systems
IoT-powered manufacturing requires seamless data integration to ensure real-time visibility into operations. INSIA centralizes sensor data, machine connectivity, and multiple data sources into a single, intelligent platform.
- Sensor Data Collection – Connects directly to IoT devices, PLCs, and edge sensors to capture real-time machine data.
- Machine Connectivity – Ensures interoperability between legacy systems, industrial equipment, and modern IoT solutions.
- Multiple Data Source Integration – Consolidates ERP, MES, and third-party data for a single source of truth.
- Automated Data Streaming – Delivers continuous, real-time insights without manual intervention.
Outcome: No data silos. Just real-time intelligence for smarter decision-making.
- Connected Factory Analytics: Driving Efficiency and Predictability
Once data is centralized, INSIA applies advanced analytics to extract insights that optimize production, enhance maintenance, and improve quality control.
- Equipment Performance Monitoring – Tracks uptime, energy use, and performance trends to maximize operational efficiency.
- Predictive Maintenance Insights – Uses AI-driven analysis to identify potential failures before they cause downtime.
- Production Line Analytics – Provides real-time production metrics, helping manufacturers adjust workflows dynamically.
- Real-Time Quality Control – Detects defects and inconsistencies instantly, reducing waste and rework costs.
Outcome: Prevent issues before they happen and keep production running at peak efficiency.
- Push AI for IoT Data: Intelligent Automation for Proactive Decision-Making
INSIA doesn’t just report on past performance—it predicts, prevents, and optimizes operations using AI and machine learning.
- Automated Anomaly Detection – Identifies irregularities in machine behavior to prevent failures.
- Predictive Analytics – Forecasts demand, optimizes maintenance schedules, and reduces downtime.
- Machine Learning Patterns – Learns from historical data to improve production efficiency over time.
- Proactive Alerts – Sends instant notifications when machines exceed critical thresholds, enabling fast corrective action.
Outcome: AI-powered insights that help manufacturers stay ahead of potential disruptions.
- Interactive IoT Dashboards: A Clear, Customizable View of Operations
INSIA transforms complex data into easy-to-read dashboards, ensuring manufacturers see critical information at a glance.
- Equipment Health Monitoring – Tracks the status of every machine in real time.
- Production Metrics Visualization – Converts raw data into intuitive charts and KPIs.
- Real-Time Sensor Data Display – Monitors vibration, temperature, and operational metrics from IoT sensors.
- Custom KPI Tracking – Allows teams to set and track manufacturing-specific performance indicators.
Outcome: Instant access to the insights that matter most—when and where you need them.
Conclusion
The integration of IoT in manufacturing is no longer a futuristic concept—it’s a business necessity. From real-time data integration and predictive maintenance to AI-driven analytics and automated quality control, IoT solutions are redefining efficiency, reducing costs, and preventing downtime.
However, collecting IoT data is just the beginning. The true value lies in transforming raw data into actionable intelligence—and that’s where INSIA.ai comes in.
With INSIA, manufacturers don’t just collect data—they use it to drive better decisions, eliminate inefficiencies, and future-proof their operations.
Don’t let valuable data go to waste. Discover how INSIA’s AI-powered analytics can transform your factory’s performance and keep your operations running at peak efficiency.