Tired of dealing with excess inventory that eats up your capital? Or constantly juggling the pressure to meet customer demand without overstocking? As a business leader or IT professional, you’re always looking for ways to boost efficiency and cut costs.
What if you could streamline your supply chain, reduce waste, and improve your bottom line—without spending big on storage or logistics?
Just in time (JIT) in supply chain management might be the answer. By syncing your inventory with actual demand, JIT helps eliminate overstock, lower costs, and keep your operations agile. But getting JIT right can be tricky—especially across complex, data-heavy industries like finance, healthcare, or retail.
In this blog, we’ll explore how JIT can optimize your supply chain, cut waste, and improve efficiency. Before diving into the details, let's break down exactly what Just-in-Time (JIT) is and why it’s such a game-changer for modern supply chains.
Overview of Just-in-Time (JIT) in Supply Chain Management
In supply chain management, Just-in-Time (JIT) is a strategy that focuses on minimizing inventory and increasing efficiency by having materials arrive exactly when they are needed.
This approach is highly beneficial in industries like manufacturing, where even small inefficiencies can have a significant financial impact.
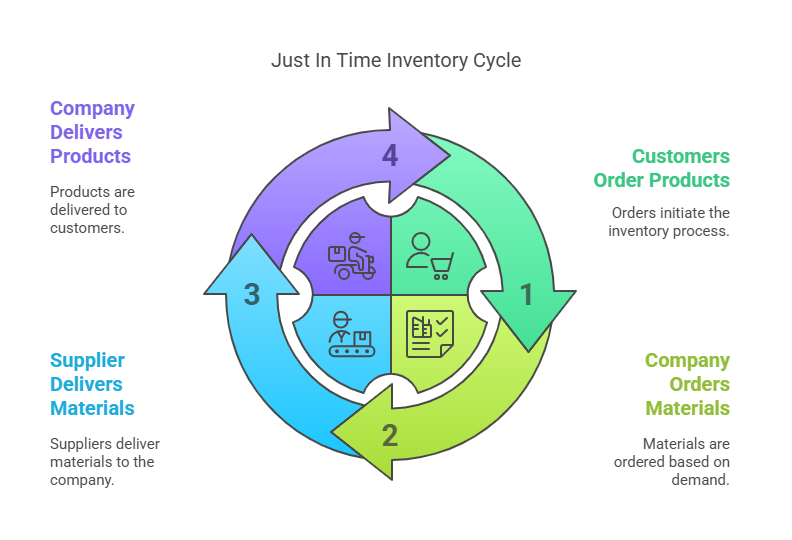
Let’s consider a real-world example to illustrate the concept: Imagine you're managing a car manufacturing plant. In the past, your warehouse stored large quantities of car parts like engines, doors, and tires. The idea was to have plenty of parts on hand to avoid production delays. However, this approach led to higher storage costs, wasted space, and sometimes parts going out of date before they could be used.
With JIT, you make a shift. Instead of holding onto large stockpiles, you work closely with suppliers to deliver parts to your plant right when they are needed on the assembly line. For example, engines arrive just in time for installation, and tires arrive when the car is about to be assembled. This system ensures that production runs smoothly without excess inventory, reducing storage costs and minimizing waste.
The power of JIT in this scenario lies in its precision. By relying on accurate forecasting and a strong relationship with suppliers, the plant is able to avoid overstocking or running out of parts. It cuts costs and improves cash flow, as money isn’t tied up in unused inventory. Additionally, because parts are fresh and on-demand, the risk of defects or obsolescence is reduced, leading to better product quality.
Also Read: Importance and Characteristics of Data Quality in Data Analytics
Now that we have the basics of JIT covered, let's take a closer look at the key principles that make this approach so effective in streamlining operations.
Key Principles of JIT in Supply Chain Management
Understanding the core principles of Just-in-Time (JIT) is crucial for successfully implementing this approach in any supply chain. Let’s break down the four key principles that drive JIT and make it an effective strategy for reducing costs and improving efficiency:
Demand-Driven Production
The first principle of JIT is to produce only what’s needed, when it’s needed. By aligning production schedules closely with actual customer demand, businesses can avoid overproduction—an issue that leads to excess inventory and wasted resources.
.png)
Instead of manufacturing large quantities of products in anticipation of demand, JIT encourages manufacturers to respond dynamically to real-time customer needs. This approach ensures that production stays aligned with market demands, resulting in minimal waste and more responsive operations.
Inventory Minimization
The JIT model focuses on reducing inventory levels to a minimum. By keeping inventory low, businesses can significantly lower holding costs and avoid tying up capital in unsold goods. The focus is on having the right materials available at the right time—nothing more, nothing less. This leads to increased cash flow, as there’s less money spent on maintaining inventory. Companies that adopt JIT also find it easier to manage cash reserves and avoid excess stock that might eventually become obsolete or unsellable.
Continuous Improvement (Kaizen)
In the JIT framework, Kaizen—the Japanese concept of continuous improvement—is a vital component. This principle fosters a culture of ongoing enhancement, where businesses consistently assess and improve processes, quality, and efficiency.
.png)
JIT isn’t just about reducing waste; it’s about refining all aspects of production. Employees are encouraged to identify inefficiencies, innovate, and find ways to improve the overall process, driving productivity and product quality.
Supplier Integration
A critical principle of JIT is building strong relationships with suppliers to ensure the timely delivery of materials. Since JIT relies on precisely timed deliveries, supplier collaboration is essential for success. Companies must work with suppliers to coordinate production schedules, ensure material quality, and guarantee on-time delivery. By fostering these relationships, businesses can create a more reliable and efficient supply chain that meets demand without delay or overstocking.
Elimination of Waste
At the heart of JIT is a constant drive to cut out waste in all forms—whether it’s unnecessary materials, time, or labor. The goal is simple: streamline every part of the production process so that only what’s needed is used. By continually finding ways to eliminate inefficiencies, businesses can focus their resources on what truly adds value, helping them become more profitable while being mindful of sustainability.
Quality Management
In JIT, quality isn’t just a final step—it’s built into every part of the process. The focus is on ensuring that every product meets high standards, from start to finish, which prevents costly defects or rework later on. By prioritizing quality from the get-go, businesses avoid delays, reduce returns, and keep customers happy. This commitment to quality is essential for keeping the JIT approach running smoothly and efficiently.
Efficient Use of Resources
JIT is all about maximizing the potential of every resource at hand—whether that’s human talent, materials, or technology. It’s not just about minimizing inventory but also about ensuring that all resources are being used to their full potential. With the right processes and tools in place, businesses can avoid waste and get the most out of what they have, which means higher productivity and more effective operations.
Standardized Processes
For JIT to work seamlessly, having standardized processes in place is key. This ensures that everything runs smoothly and consistently across the board. With clear procedures in place, errors are minimized, training becomes quicker, and improvements can be identified more easily. It’s all about creating a reliable foundation where every task is predictable, making day-to-day operations much more efficient.
Flexibility and Agility
One of the key strengths of JIT is its flexibility. Since production schedules are driven by real-time demand, businesses need to be ready to pivot quickly. Whether it’s ramping up production to meet a sudden spike in orders or adjusting processes to manage disruptions, the ability to adapt is crucial. Being agile in response to changing market conditions is what helps keep everything on track and the supply chain running smoothly.
With the core principles in mind, it’s time to explore how to put them into practice and implement JIT effectively in your supply chain.
Implementing JIT in Supply Chain Management
The principles of Just-in-Time (JIT) provide the foundation, but turning those ideas into real-world success requires smart strategies and practical tools. Here’s how businesses can make JIT work for them:
- Demand Forecasting
Accurate forecasting is at the heart of JIT. By tapping into data and past trends, businesses can predict what customers will want—and when they’ll want it. This means production schedules are perfectly aligned with actual demand, avoiding both underproduction and overstocking. With precise forecasting, companies can make sure they’re only producing what’s needed, reducing waste and improving cash flow.
- Inventory Management
When it comes to JIT, inventory management is crucial. One key strategy is cross-docking, where products move directly from incoming shipments to outbound ones without sitting in a warehouse. This approach keeps inventory flowing smoothly, reduces storage costs, and ensures materials reach production just in time. With fewer goods stored, companies improve cash flow and make better use of limited warehouse space.
- Supplier Collaboration
A smooth JIT system depends on strong relationships with suppliers. By working closely with suppliers, businesses can sync up on production schedules and delivery times, ensuring parts arrive exactly when needed. When companies and suppliers plan together, it minimizes delays, cuts down on inventory requirements, and keeps the supply chain running smoothly without unnecessary stops or hold-ups.
- Process Optimization
In JIT, improving processes is an ongoing effort. Regularly reviewing and optimizing manufacturing operations helps businesses spot inefficiencies and find ways to improve. Small changes—like refining workflow, redesigning layouts, or adding automation—can lead to big gains in productivity. These improvements help reduce waste and ensure high-quality products are delivered on time, every time.
- Lean Production Processes
To make JIT work, businesses need to focus on lean production. This means cutting out unnecessary steps, reducing extra inventory, and making everything as efficient as possible. By doing this, companies can lower costs, speed up production, and ensure they’re only making what’s needed without wasting resources.
- Flexible Production Scheduling
In a JIT system, flexibility is everything. You need to be able to quickly adjust production schedules to meet changing demands. This might mean adjusting shifts or rearranging production lines to handle different products. The idea is to stay responsive so you’re always on track to meet demand without overdoing it on production.
- Effective Communication Channels
Communication is key when it comes to JIT. Suppliers, production teams, and logistics need to be on the same page. Using clear and open communication channels helps keep things running smoothly, whether tracking delivery times or avoiding potential delays. This coordination prevents hiccups and ensures the supply chain doesn’t hit any roadblocks.
- Technology Integration
Leveraging technology can make a world of difference in JIT. Tools like ERP and MRP systems help manage inventory and production in real time, so you’re always prepared. Plus, automating certain processes reduces errors and speeds things up. With the right tech, companies can keep everything flowing smoothly, from the factory floor to the supply chain.
- Employee Training
For JIT to truly work, everyone in the company needs to understand how it all fits together. That’s where employee training comes in. Regularly updating staff on JIT principles, waste reduction techniques, and efficiency practices ensures they’re empowered to make decisions that keep things running efficiently and reduce bottlenecks in production.
While JIT can work wonders, it's important to understand how it stacks up against traditional inventory models to see if it’s the right fit for you.
JIT vs. Traditional Inventory Management
Understanding the differences between Just-in-Time (JIT) and traditional inventory models is key to choosing the right approach for your business. Let’s break down how JIT stacks up against more conventional inventory management strategies, such as Economic Order Quantity (EOQ) and the order-up-to level.
Key Differences Between JIT and Traditional Inventory Management
Traditional inventory management models like EOQ and order-up-to level focus on keeping stock levels high to prevent stockouts, ensuring that businesses have enough inventory to meet anticipated demand. With EOQ, companies order fixed quantities of stock at regular intervals, regardless of actual demand fluctuations. The idea is to strike a balance between ordering costs and holding costs, but it can lead to excess stock or inventory sitting idle.
In contrast, JIT is demand-driven. The goal is to keep inventory at a bare minimum, only ordering and receiving materials when they are needed in the production process. This eliminates overstocking and helps reduce the costs associated with storing and managing excess goods. JIT relies on precise demand forecasting, supplier relationships, and tight control over production schedules.
Which Method Is Right for You?
The choice between JIT and traditional inventory models depends on several factors, such as the size of your business, the nature of your industry, and how predictable your demand is.
- For large businesses with a consistent supply chain and predictable demand, JIT can be a game-changer, cutting down on excess inventory and storage costs while improving operational efficiency.
- For smaller businesses or industries with fluctuating demand, traditional models like EOQ might offer more security by ensuring that stock is always available to meet uncertain needs.
- In industries like healthcare or retail, where demand can be volatile and product lifecycles are shorter, JIT provides a more agile approach, helping to minimize waste and keep products fresh.
Check out the table below to get a clearer concept:
Now that we know the key differences, let’s dive into the real benefits JIT brings to the table—how it transforms cost efficiency and operational performance.
Benefits of JIT Implementation
Implementing Just-in-Time (JIT) inventory management offers businesses a wide range of benefits, especially when it comes to reducing costs and improving efficiency. Let’s take a closer look at some of the key advantages that JIT brings to the table.
- Cost Reduction
One of the most significant benefits of JIT is cost reduction. By minimizing inventory levels, businesses can drastically cut operational costs associated with storing, managing, and insuring goods. With less stock on hand, companies also reduce the risk of inventory becoming obsolete or spoiled. JIT allows for better cash flow since funds aren’t tied up in excess inventory, freeing up capital for other areas of the business.
- Enhanced Efficiency
JIT boosts production efficiency by reducing the time spent managing and moving inventory. Since materials arrive just in time for use, businesses avoid unnecessary delays in production. This means faster turnaround times, improved timelines, and a more responsive approach to market demand.
Furthermore, by maintaining lean operations, JIT reduces bottlenecks, allowing the business to operate at a smoother, more predictable pace.
- Waste Reduction
One of the key principles of JIT is waste minimization. By producing only what is needed, when it is needed, JIT significantly reduces overproduction and prevents the accumulation of surplus inventory. This also reduces the likelihood of defects, as products are made with fresh materials and immediately used in the production process.
- Better Quality Control
With JIT, production happens in smaller batches, making it much easier to catch issues early. If a defect pops up, it's easier to fix right away, so only top-notch products make it to your customers.
- Lower Lead Times
Since JIT streamlines everything, it speeds up both production and delivery. That means customers get their orders faster, without unnecessary delays, and you're always ahead of the game when demand spikes.
- Optimized Resource Utilization
JIT helps you make the most out of your people, equipment, and materials. You’re not overstocking or underusing anything, which keeps everything running smoothly and reduces waste across the board.
- Increased Profitability
By cutting down on costs like excess inventory and unnecessary downtime, JIT can really boost your bottom line. The savings add up, and quicker production means you can focus on growing profits.
- Improved Customer Satisfaction
Faster deliveries and consistent quality go a long way in making customers happy. When they get exactly what they want, when they want it, you're building trust and loyalty, keeping them coming back for more.
To ensure JIT is delivering on its promises, you need the right metrics. Let's explore the KPIs that will tell you exactly how well JIT is performing.
Metrics and KPIs for Measuring JIT Success
To truly understand how well your Just-in-Time (JIT) inventory system is performing, tracking the right metrics is key. These metrics give you clear insights into areas where things are running smoothly and where adjustments might be needed. Here are the most important metrics to keep an eye on when measuring JIT success:
Inventory Turnover Ratio
The Inventory Turnover Ratio shows you how quickly inventory is moving through your supply chain. In a JIT system, the goal is to keep stock moving efficiently, so a higher ratio indicates that your inventory is being used effectively without overstocking.
- COGS: Total cost of the goods sold over a specific period.
- Average Inventory: The average amount of inventory held during that same period.
A higher turnover means you’re reducing excess inventory and relying on a just-in-time approach to meet demand.
Order Fulfillment Time
Order Fulfillment Time tells you how quickly your business is processing and shipping orders. In a JIT system, faster order fulfillment means your supply chain is in sync with demand. This metric is crucial for understanding how quickly you can respond to customer orders and get products out the door.
Supplier Lead Time Accuracy
This metric measures how often your suppliers deliver on time. In JIT, having suppliers who can reliably deliver materials exactly when you need them is critical. If there’s any delay, it can disrupt your entire operation. This KPI helps you keep track of how well your suppliers are sticking to their delivery schedules.
The higher the percentage, the more reliable your suppliers are in keeping your production line running smoothly without hiccups.
Stockout Rate
The Stockout Rate measures how often you run out of stock. In a JIT system, the goal is to have just enough inventory on hand to meet customer demand without excess. If you’re experiencing frequent stockouts, it could mean that your JIT system needs a little fine-tuning.
A low stockout rate is a good sign that your JIT approach is working well, ensuring you always have the right amount of stock to meet demand.
Of course, no system is without its challenges. Let’s now look at the common risks businesses face when adopting JIT and how to tackle them.
Challenges and Risks
While Just-in-Time (JIT) offers many benefits, it’s not without its challenges and risks. Understanding these risks will help you navigate potential pitfalls and ensure a smoother operation.
- Supplier Reliability
One of the main risks of JIT is the heavy reliance on suppliers for timely deliveries. If a supplier faces any delays—whether due to production issues, shipping disruptions, or external factors—it can create a ripple effect, halting your entire production process. In JIT, where there’s little to no buffer stock, even minor delays can result in significant setbacks. Maintaining strong, reliable relationships with suppliers is essential to mitigate this risk.
- Demand Variability
Customer demand can be unpredictable, and in a JIT system, this can lead to problems if demand suddenly spikes or drops unexpectedly. Since JIT relies on precise forecasting, any fluctuations in demand that were not anticipated can result in stockouts or underproduction. This is especially challenging in industries where demand is seasonal or influenced by external factors, such as fashion trends or market changes.
- Operational Disruptions
External factors, such as natural disasters, pandemics, or geopolitical tensions, can severely disrupt JIT systems. These disruptions may delay shipments, halt production, or cause shortages of key components. For businesses that rely on just-in-time practices, even a temporary disruption can have lasting consequences, affecting customer satisfaction and overall supply chain efficiency. Having contingency plans in place is critical to minimize the impact of such events.
While JIT offers huge potential, modern technology can help overcome its challenges. Here’s how the latest innovations support a more efficient JIT system.
Technology’s Role in Supporting JIT
Technology is a key factor in making Just-In-Time (JIT) systems more successful. Let's dive into how new tech is making JIT smoother, more flexible, and more efficient.
- Tech Integration in JIT
Technologies like the Internet of Things (IoT), Artificial Intelligence (AI), and blockchain are changing the way JIT works. For instance, IoT devices help businesses track inventory in real time, giving them an up-to-date view of stock levels and ensuring materials arrive just when they’re needed. AI takes it further by improving demand forecasting.
By analyzing past data, AI predicts trends more accurately, so businesses can stay ahead. Blockchain adds another layer of reliability by securely tracking product movements and supplier interactions, making deliveries more dependable and less prone to delays.
- The Role of Automation in JIT
Automation is making JIT more efficient across the board. Automated ordering systems help maintain optimal stock levels by automatically placing orders with suppliers once inventory drops below a certain point. Real-time tracking also gives businesses the ability to monitor shipments and production without having to manually check.
Plus, smart warehouse systems are improving inventory management, reducing human errors, and speeding up the process of getting goods out the door. Together, these technologies make JIT systems more agile, responsive, and effective.
Talk is great, but real-world results are even better. Let’s explore some case studies of companies that successfully implemented JIT and reaped the rewards.
Case Studies of Successful JIT Implementation
Real-world examples show how successfully implementing JIT can lead to major boosts in operational efficiency. Let's look at a few companies that have mastered JIT.
Real-World Examples
- One of the most well-known examples of JIT success is Toyota. The company transformed the automotive industry by using JIT to cut down on waste and improve production efficiency. By matching production with actual demand, Toyota minimized inventory costs and boosted product quality.
- Dell has done something similar in the computer manufacturing world, delivering custom PCs directly to customers without keeping large amounts of parts in stock.
These companies show that when done right, JIT can lower costs and make businesses more responsive to customer needs.
Overcoming Challenges
Both Toyota and Dell have faced their share of challenges when rolling out JIT, like supplier disruptions and unpredictable demand. But with strong supplier relationships, accurate demand forecasting, and ongoing process improvements, they’ve overcome these obstacles.
Toyota, for instance, focuses on building close ties with suppliers, ensuring materials arrive exactly when needed. Dell uses real-time data to quickly adjust to changes in customer demand, ensuring products are delivered on time. These examples prove that with careful planning and flexibility, JIT can be highly effective, even when challenges arise.
While JIT works wonders locally, its global impact is significant too. Let’s explore how global events influence JIT systems and what businesses need to consider.
Global Implications of JIT in Supply Chains
As businesses become more interconnected globally, the implications of Just-in-Time (JIT) on international supply chains grow. Let’s take a look at how global events can affect JIT systems and how companies are adapting to these challenges.
- Impact of Global Events on JIT
Global events such as pandemics, trade wars, or natural disasters can have far-reaching effects on JIT supply chains. The COVID-19 pandemic, for example, revealed the vulnerabilities of JIT systems when lockdowns and travel restrictions led to widespread disruptions. In such scenarios, companies with JIT systems faced delayed shipments, stockouts, and production halts. Trade wars and tariffs can also lead to delays and increased costs as companies are forced to adjust their supply chains to comply with new regulations.
- Mitigating Global Supply Chain Risks
To mitigate these risks, companies are increasingly adopting strategies like diversification of suppliers, nearshoring, and building more flexible supply chains. By having multiple suppliers from different regions, businesses can reduce their dependency on any single source, ensuring they can maintain production even if one supplier faces disruptions.
Some companies are also holding minimal buffer stock to provide a cushion against unforeseen events without abandoning the core principles of JIT. These adjustments help businesses maintain resilience while keeping their operations as lean as possible.
Looking at the broader impact, let’s now zoom in on the financial side. What costs should you expect when implementing JIT, and how does it balance out in the long term?
Cost Considerations in JIT
Implementing Just-in-Time (JIT) inventory management can be a big move for any business, but it comes with both upfront costs and long-term savings. Here’s what you need to know to assess the financial impact.
Upfront Costs vs. Long-Term Savings
Starting with JIT may require some initial investments. This could include upgrading your inventory management system, investing in better technologies, or strengthening supplier relationships. But don’t let these upfront costs scare you off.
Over time, JIT can lead to significant savings. By reducing excess inventory and optimizing processes, companies can save on storage costs, decrease handling fees, and cut down on the risk of obsolescence. In the long run, the benefits of JIT often outweigh the initial investment, resulting in more efficient operations and higher profit margins.
Let’s simplify the concept through the table below.
Cost Efficiency in Operations
JIT can have a big impact on everyday operational costs. When you keep inventory levels low, you reduce the need for large storage spaces, which means savings on warehousing. Labor costs also drop because there’s less time spent managing stock.
On top of that, transportation becomes more efficient—since inventory is managed more precisely, shipments are optimized, reducing the number of trips needed. All these factors come together to improve your bottom line, helping your business run leaner and more cost-effectively.
Also Read: How to Measure Production Efficiency?
As we focus on cost, it’s impossible to ignore sustainability. Here’s how JIT also plays a key role in creating more eco-friendly and efficient supply chains.
Role of Sustainability in JIT
Sustainability is top of mind for many businesses today, and JIT can help align your operations with green goals. Let’s explore how JIT contributes to a more sustainable supply chain.
- Environmental Impact
JIT is naturally more sustainable because it helps reduce waste. By ordering only what you need and eliminating excess inventory, businesses cut down on overproduction, which in turn reduces waste. This approach also minimizes the need for large storage facilities, which can lower energy consumption and carbon footprints.
In short, JIT not only streamlines your supply chain but also supports a greener, more eco-friendly business model.
- Green JIT Practices
JIT doesn’t just reduce waste in terms of inventory—it can also incorporate green logistics practices. For example, optimizing transportation routes to reduce fuel consumption is a smart way to make your supply chain greener.
Additionally, companies can minimise their environmental impact by using sustainable packaging and energy-efficient warehouses. Aligning your JIT system with green practices not only helps the planet but also appeals to environmentally-conscious customers, improving brand reputation and long-term growth.
Sustainability isn’t just a trend—it’s the future. Now, let’s look at how JIT will evolve, especially with technology and sustainability at its core.
The Future of JIT in Supply Chain Management
As technology continues to evolve, so does the future of Just-in-Time (JIT). Let’s look at how advancements and changing priorities will shape the next generation of JIT systems.
- Technological Advancements
The future of JIT will be powered by technology. AI-driven tools will help businesses predict demand more accurately and adjust quickly to changes, reducing the risk of stockouts or overproduction. The Internet of Things (IoT) will provide real-time visibility into inventory levels, so you’ll always know exactly where your products are in the supply chain.
Blockchain will further improve transparency, ensuring that deliveries arrive on time and reducing the likelihood of errors. With these advancements, JIT will become even more efficient and adaptable to market shifts.
- Building Resilience
While JIT is all about efficiency, the future will focus on building more resilience into the system. We’ve seen how disruptions—whether from natural disasters or global health crises—can throw JIT off balance.
Moving forward, businesses will need to create supply chains that are both lean and flexible. This means having contingency plans in place and diversifying suppliers so that, if something goes wrong, you can still keep things moving smoothly without major delays or stockouts.
- Sustainability Focus
Sustainability will continue to play a big role in the future of JIT. Businesses will look for ways to not only improve efficiency but also reduce their environmental footprint. From cutting waste to optimizing resource usage, sustainability will be at the heart of future JIT practices. By integrating these green priorities, companies can align their supply chains with eco-friendly goals while continuing to drive efficiency and cost savings.
With all this in mind, the future of JIT is promising. But it’s clear that embracing the right tools today can ensure long-term success for your business - and that is where you need INSIA.
Enhancing JIT with INSIA's Data Integration Platform
To make Just-in-Time (JIT) inventory management effective, real-time data and seamless integration are crucial. INSIA’s Data Integration Platform enhances JIT by offering powerful tools that centralize data, provide actionable insights, and streamline processes.
Here’s how INSIA helps businesses optimize their JIT systems:
- Real-Time Demand Forecasting
Accurate demand forecasting is vital for JIT, ensuring that materials arrive just when needed. INSIA’s platform integrates data from various sources, enabling real-time insights into demand trends. With AI-powered predictive analytics, businesses can forecast demand more accurately, allowing them to adjust production schedules and reduce inventory overstock or shortages.
- Streamlined Supplier Coordination
JIT depends on reliable, timely deliveries from suppliers. INSIA simplifies supplier management by centralizing supplier data and providing real-time visibility into supplier performance. With this data, businesses can proactively manage supplier relationships, adjust orders based on demand, and minimize delays, ensuring smooth, continuous operations in the JIT system.
- Automated Reporting and Data-Driven Insights
One of the biggest advantages of JIT is the ability to make quick adjustments. INSIA’s automated reporting tools make it easy to generate real-time insights into key performance metrics, such as inventory turnover and supplier lead times. With these reports, businesses can respond to operational challenges without the delays of manual data processing, improving decision-making and efficiency.
- Enhanced Collaboration Across Departments
JIT requires alignment across procurement, production, and distribution. INSIA’s platform enables collaboration between departments, ensuring that everyone is on the same page regarding inventory, demand, and production schedules. Real-time data sharing and communication make it easier to stay coordinated and responsive, which is essential for the success of JIT.
Conclusion
Adopting Just-in-Time (JIT) inventory management can significantly boost your supply chain efficiency, but it takes more than just reducing stock levels. It requires accurate forecasting, solid supplier partnerships, and real-time insights to stay ahead of demand.
That’s where INSIA comes in. With its powerful data integration platform, INSIA helps businesses optimize JIT by centralizing all your data, providing predictive analytics, and streamlining supplier coordination. If you’re ready to take your JIT operations to the next level and make smarter, faster decisions, INSIA is your solution.