Is your supply chain keeping up with the fast-evolving market demands? In industries like manufacturing, finance, healthcare, and retail, where data-driven decisions make or break success, supply chain optimization has become the secret to staying ahead.
Consider this: The global supply chain management market is projected to surge from USD 35.30 billion in 2025 to an astonishing USD 89.57 billion by 2034, growing at a rate of 10.92% CAGR.
In North America alone, the market size was valued at USD 12.71 billion in 2024, with a growth rate of 10.95% CAGR. This growth isn't just a trend—it's a call to action for businesses to optimize their operations.
But what does optimization really mean for you? How can you take control of rising costs, unpredictable demand, and operational inefficiencies while increasing agility and customer satisfaction?
In this guide, we’ll break down the key strategies behind supply chain optimization, offering real-world insights on how you can transform your operations, reduce costs, and make smarter, faster decisions.
Let’s begin by defining what supply chain optimization actually means and why it’s your business's secret weapon.
What is Supply Chain Optimization?
Supply chain optimization is the process of making every step in your supply chain as efficient and cost-effective as possible. It involves improving the flow of goods, data, and information to reduce waste and better meet customer demands.
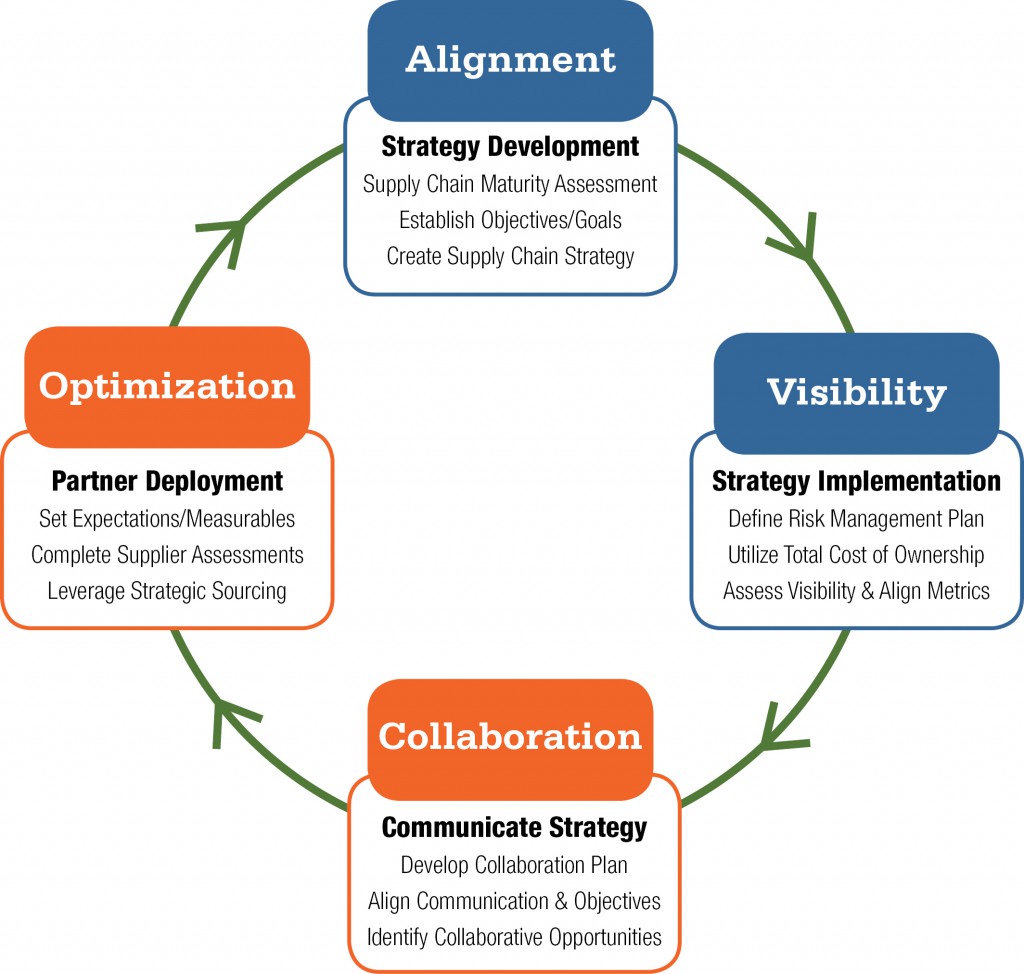
Let’s break this down with a manufacturing example: Imagine a car manufacturer that depends on various suppliers for parts like engines, tires, and electronics. In an optimized supply chain, the company ensures timely deliveries while minimizing inventory, cutting transportation costs, and speeding up production.
Here’s how optimization works:
- Demand Forecasting: Using data to predict the number of cars to produce based on market demand, avoiding overproduction or stockouts.
- Inventory Management: Working with suppliers for just-in-time deliveries to minimize storage costs.
- Logistics Optimization: Streamlining shipping routes to reduce fuel costs and delivery times.
Through smarter decisions at every stage, the manufacturer lowers costs, improves delivery times, and boosts customer satisfaction.
Also Read: Procurement vs Supply Chain Analytics: Types and Use Cases
Now that we’ve set the stage, let’s dive into the core goals that make supply chain optimization so essential.
Key Objectives of Supply Chain Optimization
Supply chain optimization is not just about improving efficiency—it’s about aligning every part of the process to achieve key goals that directly impact the bottom line. Here are the core objectives:
- Maximize Profits While Minimizing Costs
Reducing costs is at the heart of optimization. By streamlining processes, managing inventory efficiently, and cutting unnecessary expenses, businesses can increase profitability without sacrificing product quality or service delivery.
- Enhance Customer Experience and Satisfaction
A well-optimized supply chain ensures fast, accurate deliveries and reduces the chances of stockouts. Meeting customer demand with precision enhances satisfaction and builds brand loyalty, which can lead to repeat business and positive word-of-mouth.
- Achieve Agility and Flexibility in Responding to Market Changes
Market conditions are unpredictable. An optimized supply chain allows businesses to adapt quickly to changes in demand, disruptions, or supply shortages. Flexibility ensures that operations can continue smoothly even when facing unexpected challenges.
- Improve Collaboration Across the Supply Chain
Effective communication and collaboration with suppliers, partners, and internal teams are critical for smooth operations. Strengthening these relationships can lead to better decision-making, shared resources, and faster issue resolution.
- Enhance Supply Chain Visibility
Real-time visibility into supply chain activities allows for better tracking and control over inventory, shipments, and production. This transparency leads to more informed decision-making and helps prevent issues before they become critical.
- Reduce Lead Times and Improve Operational Efficiency
Streamlining the supply chain to minimize delays between order placement, production, and delivery is key. Reducing lead times increases efficiency, lowers costs, and boosts the speed at which businesses respond to market demands.
Understanding the objectives is half the battle; now let’s explore the strategies that bring them to life.
Techniques and Practices for Optimization
To truly optimize your supply chain, you need to employ the right techniques and practices that tackle inefficiencies and streamline operations. Let’s break down the key strategies that can make a significant impact on your supply chain performance:
Effective Analysis and Planning
Data-driven decisions are the cornerstone of any successful supply chain. Are you leveraging your data for accurate demand forecasting, inventory management, and route optimization? By analyzing historical trends and market signals, businesses can predict future demand and align their resources accordingly—ensuring the right products are at the right place at the right time.
Utilization of Mathematical Modeling and Management-Based Approaches
Complex supply chains often require complex solutions. This is where mathematical models and management strategies come in. From linear programming to simulation modeling, these tools can help businesses predict potential bottlenecks, optimize resource allocation, and evaluate multiple strategies before execution.
Have you considered these approaches in your decision-making process?
Adoption of Technology, Including Software Solutions and Analytics Tools
Technology is no longer optional—it’s essential. Advanced software solutions like supply chain management (SCM) platforms, predictive analytics, and AI tools can significantly enhance decision-making and streamline processes. Whether it’s automating routine tasks or analyzing vast amounts of data to identify patterns, technology can give you a clear advantage.
How integrated is your current technology stack with your supply chain processes?
Collaborative Planning and Supplier Relationship Management (SRM)
Building strong relationships with suppliers isn’t just about negotiation. Collaborative planning and information sharing can help you better align production schedules, manage risks, and reduce lead times. A well-executed SRM system allows both parties to communicate more effectively, ensuring smoother operations across the board.
How much visibility do you have into your supplier’s processes?
Automation of Routine Tasks
Automation isn't just about reducing human error; it’s about freeing up valuable resources for more strategic work. From automated order processing to robot-assisted warehouses, automating mundane tasks can drastically reduce operational costs, improve efficiency, and speed up decision-making.
Are you ready to embrace automation in your supply chain?
We’ve covered the strategies—now it’s time to dig into the actual processes that need fine-tuning.
Optimizing Supply Chain Processes
To achieve true supply chain optimization, every process from design to execution needs to be fine-tuned. Here’s how you can enhance the critical stages of your supply chain:
- Step 1: Supply Chain Design
Optimization begins with designing an efficient supply chain network. Are your material flows, warehouse locations, and transportation methods aligned with your operational needs? By mapping out your network and strategically placing warehouses and suppliers, you can reduce transportation costs and improve delivery times. A well-designed supply chain ensures that every resource is utilized effectively from the start.
- Step 2: Supply Chain Planning
Planning is key to staying ahead of demand fluctuations. How accurate are your demand forecasts? Utilizing predictive analytics, you can anticipate customer demand and adjust production schedules and inventory levels accordingly. Effective inventory management ensures you’re never overstocked or understocked, minimizing costs and maximizing service levels.
- Step 3: Supply Chain Operations
The daily operations of your supply chain are where optimization shines through. From managing logistics and transportation routes to handling data and navigating global trade complexities, every decision impacts efficiency. Do you have real-time visibility into your operations? Streamlining logistics and using data to optimize routes can significantly cut delivery times and fuel costs, while better data management helps avoid errors and delays.
While optimization is key, let's face it: even the best-laid plans come with a fair share of hurdles.
Challenges in Supply Chain Optimization
Optimizing a supply chain is no easy feat. Businesses face numerous challenges that hinder their efforts to streamline processes and achieve maximum efficiency. Here are the most common challenges:
Invisible Bottlenecks and Inefficiencies
Have you ever noticed delays without knowing exactly where they’re coming from? Hidden bottlenecks can plague supply chains, slowing down production, logistics, or even inventory management. These inefficiencies are often buried deep within complex workflows, and pinpointing them requires constant monitoring and an eye for detail.
Global Disruptions and Supply Chain Volatility
Global disruptions—from trade wars to pandemics—can have an immediate impact on your supply chain. Rising tariffs, political instability, or unexpected events like natural disasters make it difficult to maintain steady inventory flow and manage logistics. How can you ensure smooth operations when your supply chain is at the mercy of world events?
Data Fragmentation and Lack of Real-Time Visibility
Is your data spread across multiple systems? Without a unified view of operations, it’s almost impossible to make quick, data-driven decisions. Fragmented data creates silos, leaving gaps in crucial information and preventing you from responding to issues as they arise.
Demand Volatility and Customer Expectations
Can you keep up with changing customer demands? With the shift toward instant gratification, customers expect faster deliveries and more product availability. But predicting demand in real-time is tough—especially when consumer behavior shifts unexpectedly. How do you balance the fine line between satisfying customers and avoiding overstocking or understocking?
Inaccurate Demand Forecasting and Risk Management
Forecasting demand with precision is a tough challenge, especially in unpredictable markets. Relying on inaccurate data can lead to stockouts or excessive inventory. Without a strong risk management framework, small miscalculations can result in big losses.
We’ve examined the struggles; now, let’s uncover the substantial rewards that come with overcoming these challenges.
Benefits of Effective Supply Chain Optimization
While the challenges are real, the rewards of optimizing your supply chain are undeniable. Here’s what your business can gain:
- Lower Operational Costs
Streamlining your processes doesn’t just increase efficiency—it directly cuts costs. From reduced storage fees to lower shipping expenses, optimizing inventory and logistics leads to significant savings. The more efficiently your resources are used, the lower your costs across the board.
- Faster Delivery and Higher Customer Satisfaction
Faster deliveries aren’t just a convenience—they’re a competitive advantage. Supply chain optimization ensures that products get to your customers quickly and accurately. In fact, studies show that businesses that optimize their supply chains see a measurable increase in customer satisfaction and loyalty.
- Stronger Supplier Relationships and Improved Collaboration
Strong partnerships with suppliers are crucial to a successful supply chain. Optimized communication and planning allow you to collaborate more effectively, leading to better lead times, more consistent product quality, and fewer disruptions. Have you nurtured these relationships to their full potential?
- Improved Data-Driven Decision Making
With real-time data and integrated systems, you can make decisions on the fly. Gone are the days of reacting to issues after they occur. An optimized supply chain gives you the visibility to predict and prevent disruptions, turning data into a powerful tool for proactive decision-making.
- Agility and Resilience in a Dynamic Market
Agility is critical in today’s fast-moving market. When your supply chain is optimized, you can quickly pivot to meet new demands, adjust to supply shortages, or adapt to unforeseen disruptions. Businesses with resilient supply chains can continue to operate smoothly—even when market conditions change overnight.
Also Read: Just-in-Time (JIT) in Supply Chain: 9 Key Principles and Benefits
With the benefits clear, it’s time to focus on the best practices that ensure your supply chain runs like a well-oiled machine.
Best Practices in Supply Chain Optimization
To get the most out of your supply chain, applying the right strategies is key. These best practices can help you streamline your operations, cut unnecessary costs, and improve overall efficiency. Let’s discuss in detail below.
- Centralized Management Software
Instead of managing multiple systems, try using one software platform that brings everything together. This helps you track everything—inventory, orders, suppliers—all in real time. With a clearer view of your supply chain, you can make quicker, smarter decisions.
- Collaborative Planning with Suppliers
Strong supplier relationships are built on open communication. By working closely with your suppliers, sharing forecasts, and planning together, you can stay ahead of demand changes and avoid delays. This collaborative approach makes operations smoother and keeps everyone on the same page.
- Scenario Planning and Simulation
The unexpected can throw off even the best-laid plans. Scenario planning lets you test different responses to potential disruptions—whether it’s a supply shortage or a natural disaster—so you’re better prepared when things don’t go as planned.
- Continuous Data Monitoring and Real-Time Analytics
With real-time data at your fingertips, you can track key metrics like inventory levels and delivery times. By monitoring your supply chain continuously, you can catch potential issues early, making sure you’re always one step ahead.
- Optimizing Inventory Management
Balancing supply and demand is crucial. With systems like just-in-time (JIT) and automated stock replenishment, you can keep your inventory at the perfect level—avoiding excess stock and reducing storage costs, all while ensuring customers get what they need on time.
- Adopt Automation and Robotics
Automation isn’t just for big companies. Whether it’s automating your order processing or using robots in your warehouse, these tools can reduce errors, cut labor costs, and speed up operations. In the end, this leads to faster deliveries and happier customers.
- Sustainability and Ethical Sourcing
More customers care about how products are made and delivered. By sourcing responsibly and reducing your carbon footprint, you not only improve your brand image but also contribute to a more sustainable future—something that’s increasingly important to your customers.
- Benchmarking Against Industry Standards
Staying competitive means knowing where you stand. Benchmark your supply chain’s performance against industry standards—like lead times, costs, and accuracy—to see where improvements are needed. This ongoing assessment helps you stay sharp and continuously improve.
You’ve got the best practices down—now, let’s see how IoT can give your supply chain a serious technological boost.
Role of IoT in Supply Chain Optimization
The Supply Chain IoT market is experiencing rapid growth, with projections to reach USD 495.58 billion by 2034, up from USD 99.41 billion in 2025, growing at a CAGR of 19.54%. This growth is fueled by the rising demand for optimized, efficient supply chains across industries.
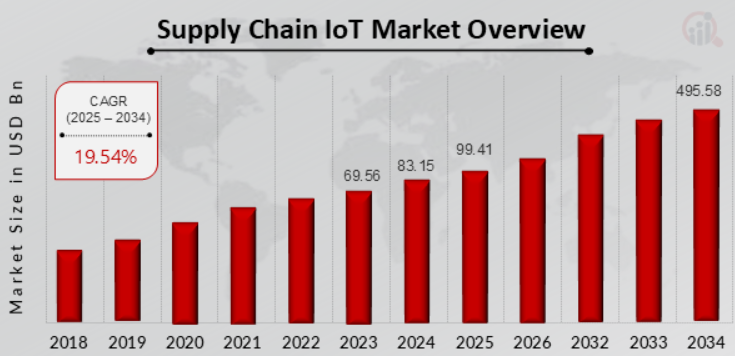
Why is IoT so essential for supply chains? By integrating IoT, cloud technology, and analytics, businesses can significantly boost visibility, reduce costs, and enhance service. Real-time data drives this transformation, enabling businesses to track inventory, monitor assets, and optimize operations at scale.
Key Benefits of IoT in Supply Chain Optimization
1. Real-Time Visibility
IoT enables continuous tracking of goods and assets, providing businesses with constant updates on inventory, location, and condition. This visibility helps businesses respond quickly to issues, improving efficiency. The inventory management segment, which holds 27.5% of the market share, is expected to grow to USD 80.5 billion by 2032 at a CAGR of 19.8%.
2. Increased Efficiency
Integrating IoT with cloud platforms automates processes like inventory management and fleet optimization. This reduces manual work, minimizes errors, and cuts costs. The fleet management segment is projected to grow to USD 55.6 billion by 2032, with a CAGR of 19.1%.
3. Predictive Maintenance
IoT sensors monitor equipment and predict when maintenance is needed, minimizing downtime and reducing repair costs. The incorporation of AI and machine learning enhances forecasting and maintenance planning.
4. Smarter Decision-Making
IoT systems provide valuable insights for better forecasting, inventory management, and decision-making. The software segment is expected to grow at a CAGR of 20.5% from 2025 to 2034, driven by increasing demand for analytics.
The IoT hardware segment leads the market with 45% of the share in 2023, reflecting the growing adoption of IoT sensors and RFID technology.
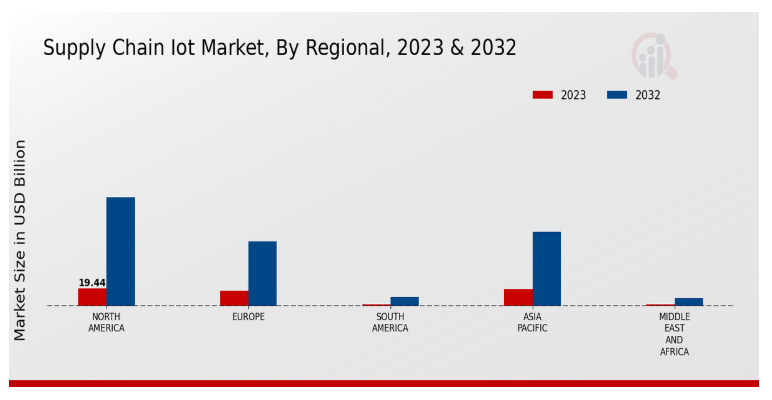
North America leads IoT adoption, projected to generate USD 120.6 billion in 2024, followed by growth in Europe and Asia-Pacific, fueled by manufacturing growth and government support for IoT.
We’ve looked at how IoT is transforming today’s supply chains; now, let’s peek into what the future holds.
Future of Supply Chain Optimization
The future of supply chain optimization is driven by new technologies that increase automation, improve accuracy, and make the entire system more resilient. These innovations will continue to shape how businesses manage their supply chains, ensuring they can keep pace with market demands.
Blockchain for Transparency and Security
Blockchain technology provides a secure, transparent way to track transactions across the supply chain. With each step recorded on an immutable ledger, businesses can ensure data integrity and reduce fraud.
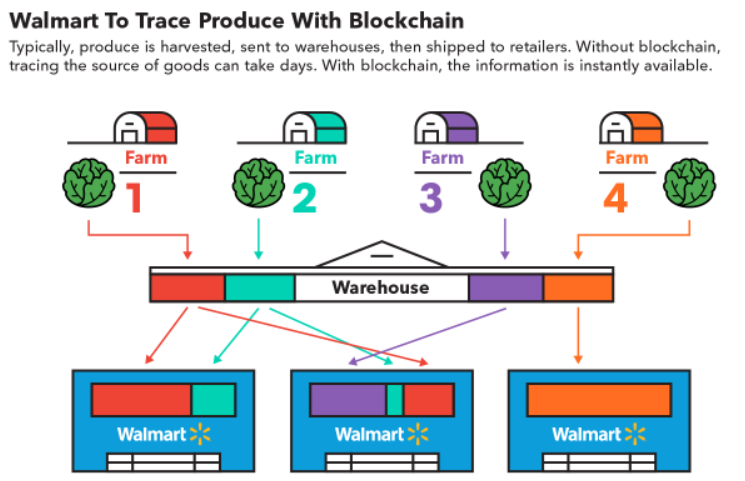
Example: A food supplier uses blockchain to track every step of their product—from farm to table. Consumers can scan a product’s QR code to verify its origin and safety, ensuring transparency and building trust in the brand.
AI and Autonomous Vehicles
AI will continue to play a larger role in automating supply chains, optimizing routes, and managing inventory. Autonomous trucks and drones will revolutionize logistics, reducing human error and speeding up deliveries.
Example: An e-commerce company utilizes AI-powered autonomous drones to deliver products to customers in urban areas. This reduces delivery times from days to hours, enhancing customer experience while reducing transportation costs.
Self-Healing Supply Chains
The concept of a self-healing supply chain refers to systems that automatically adjust to disruptions—whether from demand fluctuations or external factors—without requiring manual intervention. By using AI and machine learning, these systems learn from past disruptions and proactively implement solutions.
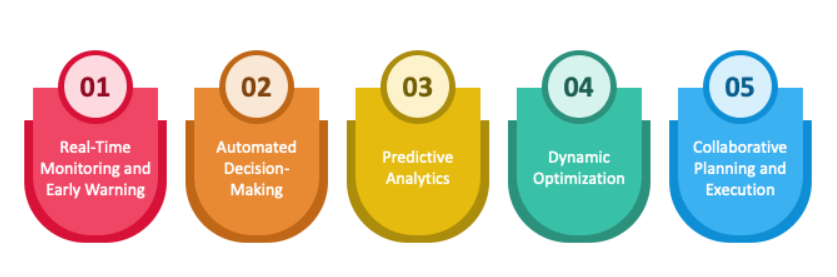
Example: A car manufacturer faces a supply chain disruption when a major supplier unexpectedly shuts down. With a self-healing system, the AI automatically identifies alternative suppliers and adjusts production schedules, minimizing downtime without human input.
The future is bright, but what about today? Here are actionable tips to help SMEs optimize their supply chain right now.
Supply Chain Optimization Tips for SMEs
For small and medium-sized businesses, optimizing the supply chain can make a huge difference. The good news? You don’t need a massive budget to make it happen. Here’s how SMEs can improve their supply chain without breaking the bank:
- Embrace Affordable Tech Solutions
There are plenty of cost-effective tools to automate inventory tracking and order processing. These tools help reduce manual work, avoid mistakes, and free up your time for more important growth activities.
- Simplify Inventory Management
With just-in-time (JIT) systems, you can keep your stock levels in check, avoiding the costs of excess inventory. Real-time tracking helps ensure you only hold what you need, boosting cash flow and minimizing storage costs.
- Optimize Your Shipping
Partnering with third-party logistics (3PL) providers can give you access to better shipping rates and more efficient distribution networks. This helps cut shipping costs while still delivering on customer expectations for speed and reliability.
- Strengthen Supplier Relationships
Building strong partnerships with your suppliers can lead to better pricing, flexible delivery schedules, and early alerts about potential issues. A smooth relationship means fewer disruptions and a more reliable supply chain.
- Use Data to Make Smarter Decisions
Analytics tools don’t have to be expensive. Tracking sales trends, inventory turnover, and supplier performance can give you valuable insights, helping you make better decisions and stay agile in a competitive market.
- Go for Scalable Solutions
Choose cloud-based solutions that grow with your business. These platforms are affordable and adaptable, providing the flexibility you need as your operations expand without heavy upfront costs.
Ready for a game-changer? Let’s see how INSIA.ai can turn your supply chain optimization into a true competitive edge.
How INSIA.ai Can Supercharge Your Supply Chain Optimization?
When your supply chain is scattered across multiple systems and data sources, making informed decisions becomes a challenge.
Enter INSIA.ai, the all-in-one solution designed to integrate, streamline, and optimize your entire supply chain process.
With INSIA.ai, you’re not just managing your supply chain—you’re taking it to the next level. Here’s how:
- Real-Time Data Integration for Smarter Decisions
Stop chasing fragmented data across multiple platforms. INSIA.ai centralizes everything in one place, pulling data from 30+ sources so you can finally make decisions based on a single, reliable source of truth. Efficiency just got a major upgrade.
- Predictive Analytics for Proactive Optimization
What if you could predict the future? Well, INSIA.ai lets you do just that. With predictive analytics (Push AI), you can forecast disruptions, optimize inventory, and adjust production schedules before the chaos hits. It’s like having a crystal ball, but more data-driven.
- AI-Powered Risk Management
Let’s face it—supply chain disruptions are inevitable. But with INSIA’s AI insights, you’ll spot potential risks long before they turn into full-blown problems. So when a bump in the road comes along, you’re already prepared to handle it smoothly.
- Seamless Integration and Automation
We get it—manual processes are the worst. INSIA.ai integrates smoothly with your existing systems, automating tasks and freeing up your team to focus on what really matters.
- Agility and Scalability in a Fast-Moving Market
In today’s market, you need to move fast. INSIA’s real-time insights and scalable solutions let you adapt to demand shifts or production changes without breaking a sweat. Stay flexible and responsive—because in this game, agility is everything.
- Customizable KPIs and Dashboards
Not all KPIs are created equal. With INSIA.ai, you can create custom dashboards that track the metrics that matter to your business. No more sifting through irrelevant data—just the insights you need to make smarter decisions, faster.
- Anomaly Detection and Alerts
Let’s keep it simple—INSIA spots problems before you do. With automated anomaly detection, the platform identifies potential issues and sends real-time alerts, so you can jump in and mitigate risks before they turn into disasters.
- Collaboration Tools
INSIA makes collaboration easy with built-in data sharing tools that enable your teams to access and discuss insights across departments. Improved communication and collaboration lead to quicker decision-making and more efficient operations across the board.
Conclusion
Running an efficient supply chain isn’t just important—it’s essential for success. With INSIA.ai, you can streamline your processes, gain real-time insights, and make smarter decisions faster.
Instead of waiting for problems to arise, INSIA.ai helps you stay ahead, optimize inventory, and make sure everything runs smoothly, all while saving you time and money.