Are you struggling to keep up with fluctuating demand? Do unexpected surges leave your resources strained? You know that inefficient resource allocation impacts your bottom line. You see that your data shows a mismatch between your capacity and your needs. Many businesses face these exact challenges. You want to avoid lost revenue and customer dissatisfaction. You need to know how to plan effectively.
This article provides strategies to balance your resources. You learn how to meet demand with precision. You will discover processes to improve your operations. You want practical steps you can implement today.
Now that you’ve got the big picture, let’s break down what capacity planning truly means and why it matters.
Understanding Capacity Planning
Capacity planning determines the resources you need to meet future demand. You must align your production abilities with customer needs.
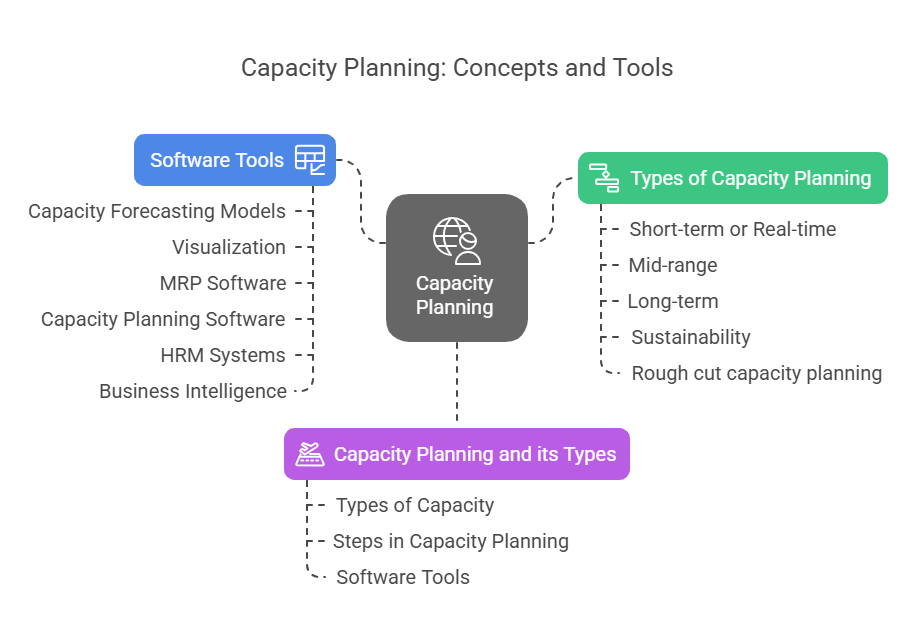
Consider a manufacturing plant that produces smartwatches. This plant has a fixed number of machines and workers. The plant's capacity is the maximum number of smartwatches it can produce in a given period. If demand for these smartwatches increases, the plant must plan to meet that demand. You could add more machines or hire more workers. You might improve the efficiency of current processes.
Without proper planning, the plant risks delays and lost sales. You could also overspend on resources you do not need. Good planning helps you avoid these issues. You ensure your resources match your output requirements. You maintain operational efficiency and customer satisfaction.
Knowing the "what" is key, but the "which" reveals how to tailor your approach.
Types of Capacity Planning
You need to understand the different types of capacity planning to manage your resources effectively and meet your business goals. Each type focuses on a specific resource area, which allows you to fine-tune your operations.
Workforce Capacity Planning: Ensuring Adequate Staffing
You must ensure you have the correct number of employees with the right skills available at the right time to handle your workload. For example, in a manufacturing plant producing electronic components, you need to determine the number of assembly line workers required during peak production seasons to meet customer demand without delays. You analyze historical production data and sales forecasts to predict staffing needs.
Product Capacity Planning: Managing Resources for Production
You optimize the availability of materials and machinery to meet your production requirements and fulfill customer orders efficiently. Consider a food processing plant that produces packaged snacks. You need to ensure sufficient raw material inventory and operational machinery to meet the daily production targets. You monitor inventory levels and schedule machine maintenance to prevent production bottlenecks.
Tool Capacity Planning: Availability of Equipment and Tools
You ensure that all necessary equipment and tools are readily available for your projects to maintain smooth operations and prevent downtime. For instance, in a metal fabrication shop, you must ensure that all welding machines, cutting tools, and other equipment are properly maintained and available for use when needed. You conduct regular equipment inspections and maintenance to minimize disruptions.
Also Read: Strategies to Improve Work, Operational, and Production Efficiency
Once you understand the types, it’s time to look at the strategies that guide how we manage our capacity.
Capacity Planning Strategies
You have three primary strategies to plan your capacity, each with distinct advantages and disadvantages, and you must select the one that aligns with your business objectives and risk tolerance.
Lead Strategy: Proactive Capacity Increase
You increase your capacity in advance of anticipated demand to ensure you can meet future customer needs and capture potential market share. For example, a car manufacturer might invest in expanding its assembly line capacity before launching a new car model, anticipating a surge in demand. This proactive approach ensures they can meet the expected sales volume.
Lag Strategy: Reactive to Demand
You increase your capacity only after demand has been realized, allowing you to avoid excess capacity and reduce costs by responding to actual market conditions. For example, a furniture manufacturing company might add a second production shift only after observing a consistent increase in customer orders, thus minimizing the risk of overspending on resources.
Match Strategy: Flexible Combination of Lead and Lag
You employ a hybrid approach that balances proactive and reactive strategies, allowing you to adapt to changing market conditions and optimize resource utilization. For instance, a textile factory might increase its raw material inventory slightly in anticipation of seasonal demand, while simultaneously monitoring sales data to determine when to add additional production lines, providing flexibility and cost efficiency.
With strategies in hand, let’s move to the step-by-step capacity planning process that ensures smooth operations.
.png)
Capacity Planning Process
You must follow a systematic process to plan capacity. This ensures your plans are accurate and effective.
.png)
You must consider these steps.
- Forecasting Demand and Analyzing Data
You predict future demand. You use historical data and trends. Your analysis helps you understand patterns. You might analyze sales data. You then predict future demand for your services. This allows you to plan for upcoming needs.
- Determining and Aligning Required Capacity
You calculate the capacity needed. This is to meet forecasted demand. You align your resources with your business goals. You must match your resources with your business’s requirement. You might calculate server capacity. This is based on projected data traffic. You ensure your infrastructure can handle the load.
- Utilizing Planning Tools and Software
You use software solutions. This helps you optimize and streamline the planning process. You gain insights into your resource usage. You automate capacity adjustments. You might use data analysis software. You then track resource utilization. You make informed decisions.
Processes in motion require measurement; metrics reveal if you are on the right track.
Capacity Planning Metrics
To ensure that capacity planning efforts are effective, businesses need to track specific metrics that offer insights into their resource utilization, production efficiency, and operational performance. These metrics help businesses assess how well they are aligning their capacity with demand and identify areas for improvement.
Key Metrics for Capacity Planning:
Utilization Rate
This metric measures the percentage of available capacity being used. A high utilization rate indicates efficient use of resources, while a low rate suggests underutilization, which may point to the need for adjustments in production or staffing levels.
- “Actual Output" is the amount of goods or services produced during a specific period.
- "Maximum Possible Output" is the total amount that could have been produced with the available resources in the same period.
The result is multiplied by 100% to express the utilization rate as a percentage.
Example: If a factory produced 800 units out of a maximum capacity of 1000 units, the utilization rate is (800 / 1000) * 100% = 80%.
Capacity Cushion
This metric indicates the amount of unused capacity available to handle sudden increases in demand. It’s important for businesses to maintain an appropriate cushion to manage unexpected demand spikes without overcommitting resources.
This metric shows the percentage of unused capacity. It is the difference between the maximum possible output and the actual output, expressed as a percentage of the maximum possible output.
Example: If a factory has a utilization rate of 80%, the capacity cushion is 100% - 80% = 20%.
Lead Time
Lead time refers to the amount of time required to fulfill an order or produce goods. Tracking this metric helps businesses gauge how quickly they can respond to customer demand and whether they need to adjust their capacity to meet delivery expectations.
- "Order Fulfillment Time" is the point in time when the order is completed and ready for delivery.
- "Order Placement Time" is the point in time when the order is received.
The result is the duration between these two points.
Example: If an order is placed at 9:00 AM and fulfilled at 3:00 PM, the lead time is 6 hours.
Throughput
Throughput is the rate at which goods are produced or services are provided. Measuring throughput ensures that businesses are operating at the optimal level of production, allowing them to identify potential bottlenecks and areas for improvement.
- "Number of Units Produced" is the quantity of goods or services completed within a given time frame.
- "Time Period" is the duration over which the production is measured (e.g., hours, days, weeks).
The result is the rate of production per unit of time.
Example: If a machine produces 500 units in 5 hours, the throughput is 500 units / 5 hours = 100 units per hour.
Next, let’s distinguish between capacity planning and resource planning—they may sound similar, but they’re worlds apart.
Comparing Capacity and Resource Planning
Capacity planning and resource planning are often used interchangeably, but they address different aspects of operational management. Both are critical for optimizing your operations, but they serve distinct purposes and strategies. Understanding the differences between them can help businesses improve efficiency, reduce costs, and ensure they’re prepared for both short-term and long-term challenges.
- Capacity Planning: A Long-Term Strategy
Capacity planning (as mentioned above) is a strategic approach that focuses on ensuring your organization has the ability to meet future demand. This involves forecasting the resources needed—such as equipment, space, and manpower—to handle anticipated growth or fluctuations. The goal is to avoid under-utilization of resources or overloading systems as demand increases.
For example, a business might plan its manufacturing capacity for the next few years, taking into account predicted demand spikes during the holiday season or after the launch of a new product line. Capacity planning is often forward-looking and involves evaluating whether the current infrastructure and operations can meet future requirements.
- Resource Planning: A Tactical Approach
Resource planning, on the other hand, is more focused on the day-to-day and tactical allocation of resources. It’s about making sure the necessary human, technological, and physical resources are available when and where they’re needed, ensuring operational efficiency on a much shorter timeline.
In resource planning, you’re looking at the specifics: which employees are needed for a particular task today? Do you have enough inventory to complete an order? Are there enough machines running for your team to meet their production targets? Unlike capacity planning, which addresses the broader picture, resource planning hones in on detailed, immediate needs and resource utilization.
Here’s a side-by-side comparison that breaks down the key differences between capacity planning and resource planning:
Also Read: What is Category Management and its Key Principles in Procurement?
Once the differences are clear, let’s dive into why capacity planning isn’t just important but a game-changer for your business.
Benefits and Importance of Capacity Planning
Whether you’re managing a manufacturing plant, a service-based business, or a technology firm, understanding the benefits of capacity planning can transform the way you manage your operations and resources.
But why is it so crucial? Let’s break it down.
- Maximizes Resource Efficiency
Effective capacity planning ensures that you’re utilizing your resources—whether it’s human capital, machinery, or technology—at their fullest potential. By aligning capacity with actual demand, businesses can avoid the common problem of over or underutilizing their assets.
For example, a manufacturing facility with proper capacity planning won’t risk operating below capacity, leading to waste or missed opportunities. Likewise, businesses won’t be burdened with idle resources, which can drain financial resources unnecessarily.
- Reduces Operational Costs
One of the most significant capacity planning benefits is its ability to reduce operational costs. By forecasting future demand and aligning it with available resources, businesses can avoid the unnecessary expenses associated with urgent hiring, overtime pay, or expedited procurement of additional resources.
With a strategic capacity plan, businesses can spread out their investments over time, ensuring that resources are only scaled up when genuinely needed, preventing the cost burden of unused or underused assets.
- Enhances Customer Satisfaction
Customer expectations today are higher than ever. Slow responses, delayed deliveries, or service lapses can quickly lead to customer dissatisfaction and lost business. Capacity planning helps you meet these expectations by ensuring you have the right resources in place when demand surges.
- Supports Growth and Scalability
As your business grows, so do your needs. Whether it’s expanding your product line, entering new markets, or increasing your customer base, capacity planning helps ensure you can scale effectively without compromising quality or performance.
By forecasting future demand, businesses can prepare for growth by scaling their infrastructure, workforce, and technology gradually, ensuring a smoother transition as they increase production or service output. This ability to scale efficiently is one of the primary reasons capacity planning is crucial for businesses aiming for long-term success.
- Mitigates Risks and Avoids Bottlenecks
Every business faces challenges—whether it’s a sudden surge in demand or unexpected disruptions in the supply chain. Capacity planning mitigates these risks by ensuring that you can adjust quickly and effectively.
A proper capacity plan allows businesses to identify potential bottlenecks before they become significant issues. For instance, if demand increases unexpectedly, your plan may already include provisions for increasing workforce shifts or acquiring additional machinery, reducing the impact of such disruptions.
- Increases Competitive Advantage
In today’s competitive market, businesses that can respond quickly and efficiently to customer demand have a significant edge. By planning your capacity effectively, you’ll ensure that your organization is always prepared to meet demand in real-time, allowing you to stand out from competitors who may struggle to keep pace.
Proactively managing capacity not only gives you an edge in operational efficiency but also positions your business as a reliable, customer-centric entity in the marketplace.
- Facilitates Better Decision-Making
Effective capacity planning also enables better strategic decision-making. When you have a clear understanding of your resource requirements and limitations, you can make informed decisions about everything from investments in new technology to entering new markets.
Capacity planning tools and software provide valuable insights into your organization’s current and future resource needs, making it easier to create data-driven strategies that align with business goals.
To truly appreciate its impact, let’s see how capacity planning plays out in various industries, from manufacturing, healthcare to retail nd more.
Capacity Planning in Different Industries
Capacity planning is a critical component across various industries, with each sector having its own specific needs and challenges. Understanding how capacity planning applies to different industries is essential for businesses looking to optimize their resources and improve efficiency.
.png)
Manufacturing Industry
In manufacturing, capacity planning ensures that production lines can meet demand without overloading the system. Manufacturers need to consider both machine capacity and labor availability to ensure they can meet production schedules while minimizing downtime and maintenance costs. Effective capacity planning helps manufacturers optimize production rates, reduce bottlenecks, and ensure timely product delivery.
Technology Industry
Capacity planning in the technology industry involves ensuring that IT infrastructure—like servers, cloud storage, and networks—can handle the increasing demand for data processing and online services. Technology companies need to anticipate spikes in usage, particularly during product launches or system updates. Cloud services, for example, need to plan for variable traffic loads to ensure their services are scalable and reliable.
Hospitality Industry
In the hospitality industry, capacity planning plays a key role in managing guest accommodation and services. Hotels, restaurants, and event venues must forecast demand based on seasonal trends, local events, and holidays. Effective capacity planning ensures there is adequate staffing, room availability, and resources for events to provide a seamless customer experience without overextending operations.
Healthcare Industry
In healthcare, capacity planning revolves around ensuring adequate staffing, facilities, and equipment to handle patient demand. This includes managing the number of beds, medical staff, and available medical devices, such as ventilators, during times of high patient volumes. Hospitals, for example, must anticipate seasonal flu outbreaks or other public health emergencies to ensure they have sufficient resources available to handle surges in patients without compromising the quality of care.
Retail Industry
For retailers, capacity planning is key to managing inventory and ensuring there is sufficient stock to meet demand, particularly during peak periods such as holidays or sales events. Retailers must plan for optimal staffing levels, warehouse capacity, and stock levels to prevent overstocking (which leads to increased storage costs) or stockouts (which can result in lost sales).
Logistics Industry
In logistics, capacity planning is all about managing transportation, warehousing, and supply chain infrastructure. It involves forecasting the necessary fleet sizes, warehouse space, and labor requirements to accommodate demand fluctuations, especially during high-demand seasons like the holiday period. For logistics companies, effective capacity planning can minimize delivery delays and ensure smooth operations during peak shipping times.
Also Read: Understanding Elements of Analytical Quality Control and Assurance
Industries may vary, but one thing’s universal—seasonality and cyclical demand are inevitable challenges in capacity planning.
The Impact of Seasonality and Cyclical Demand
Managing seasonal and cyclical demand is a challenge that businesses across all industries face. These fluctuations in demand often occur during predictable times, such as holidays, the back-to-school season, or even weather patterns. Understanding how to handle these periods is vital to maintaining efficiency and profitability.
Key Strategies to Manage Capacity During Seasonality and Cyclical Demand:
- Flexible Resource Allocation
Businesses can ensure that resources are allocated dynamically to meet fluctuations in demand. This can mean ramping up staff during peak periods or utilizing temporary workforce solutions to manage short-term increases in demand.
By analyzing historical sales data and industry trends, businesses can better predict when peak demand will occur. This helps adjust production or staffing plans in advance, allowing businesses to scale their operations efficiently.
- Inventory Management
Effective inventory management is crucial for handling seasonal demand. Businesses must ensure they have the right amount of stock to meet customer demand during peak seasons while avoiding excess inventory that incurs storage costs.
With demand cycles in mind, let’s explore how capacity planning strengthens supply chain resilience in turbulent times.
Role of Capacity Planning in Supply Chain Resilience
In today's interconnected global market, supply chain resilience is more important than ever. Capacity planning plays a critical role in ensuring businesses can quickly adapt to disruptions in their supply chains, whether caused by natural disasters, geopolitical issues, or unforeseen market conditions.
.png)
How Capacity Planning Contributes to Supply Chain Resilience:
- Proactive Resource Allocation
Effective capacity planning ensures businesses have backup resources, whether it’s alternative suppliers, additional inventory, or flexible production schedules. By diversifying their supply chains and maintaining contingency plans, businesses can mitigate the impact of disruptions.
- Improved Risk Management
With robust capacity planning, companies can identify potential weak points in their supply chains and take steps to address them before a disruption occurs. This might involve creating safety stocks, maintaining relationships with multiple suppliers, or investing in technology to improve visibility.
- Agility and Adaptability
Capacity planning ensures that businesses can quickly scale up or scale down production and staffing as needed. This level of flexibility is key to responding swiftly to supply chain disruptions and ensuring business continuity.
As supply chains evolve, automation and AI are reshaping how we approach and execute capacity planning.
Impact of Automation and AI on Capacity Planning
Automation and Artificial Intelligence (AI) are rapidly transforming how businesses approach capacity planning.
According to Market Research Future (MRFR), the capacity management market reached a valuation of $2.13 billion in 2022. Projections indicate a substantial market expansion, rising from $2.4 billion in 2023 to $6.9 billion by 2032. This growth signifies an anticipated compound annual growth rate (CAGR) of approximately 12.46% throughout the forecast period spanning 2024 to 2032.
Key Benefits of Automation and AI in Capacity Planning:
- Enhanced Forecasting and Predictive Analytics
AI-driven tools can analyze vast amounts of data to predict future demand patterns with much greater accuracy than traditional methods. This allows businesses to plan their capacity needs ahead of time, reducing the risk of over- or under-utilizing resources.
- Real-Time Adjustments
Automation allows businesses to make real-time adjustments to their resource allocation, responding to sudden shifts in demand or supply chain disruptions. For instance, AI tools can help adjust staffing levels or production schedules automatically based on real-time data.
- Operational Efficiency
With automation, businesses can streamline their planning processes by eliminating manual tasks, such as data entry or resource tracking. This leads to faster decision-making, reduced human error, and optimized resource use.
But when uncertainty strikes, even the smartest systems need agile capacity planning to weather the storm.
Capacity Planning During Times of Uncertainty
Whether it’s economic downturns, global crises, or sudden shifts in market conditions, businesses often find themselves in periods of uncertainty. During such times, capacity planning must adapt to the fluctuating nature of demand and unpredictable supply chain conditions.
Handling Capacity Planning in Uncertain Times:
- Scenario Planning
During times of uncertainty, businesses should adopt scenario planning to prepare for different possible outcomes. This involves creating flexible plans that allow for adjustments depending on how the situation unfolds. By simulating various scenarios, companies can plan for both worst-case and best-case outcomes.
- Flexible and Scalable Solutions
Businesses should build flexibility into their operations, from labor and staffing to production capacity and inventory management. For instance, having a flexible workforce or the ability to scale production up or down based on market conditions can provide resilience during uncertain times.
- Constant Monitoring and Adaptation
Uncertainty requires continuous monitoring of key performance indicators (KPIs) and operational metrics. Regularly updating forecasts and adapting plans based on changing conditions will help businesses navigate unpredictable events with greater agility.
Horizons shift, so anchor your plans with proven practices for enduring success.
Best Practices for Capacity Planning
Effective capacity planning is a cornerstone of efficient operations. However, successfully forecasting and preparing for fluctuating demand requires more than just a basic understanding of resources and needs. To ensure that your capacity planning leads to measurable improvements in performance and growth, following established best practices is essential.
Below, we explore key best practices that will help you optimize your capacity planning strategy and enhance your business’s efficiency.
- Start with Accurate Demand Forecasting
The foundation of good capacity planning is a precise demand forecast. Predicting future demand accurately is crucial to aligning your capacity with the market’s needs. Inaccurate forecasting can lead to overcapacity (wasting resources) or undercapacity (missing business opportunities).
To ensure accuracy, leverage historical data, market trends, customer insights, and industry forecasts. Combining quantitative data with qualitative insights helps create a robust demand forecast. Regularly review and adjust your forecast based on the latest data to keep your capacity planning aligned with current market conditions.
- Align Capacity with Business Goals
Every capacity planning decision should align with the broader objectives of the business. If your business is focused on scaling up, the capacity plan should reflect that by ensuring you have enough resources—whether it’s staff, machinery, or technology—to support growth.
Ensure that your capacity planning process takes into account both short-term goals (such as seasonal demand spikes) and long-term objectives (like expansion into new markets). This alignment ensures that you’re not just reacting to current conditions but preparing strategically for future opportunities.
- Identify and Address Potential Bottlenecks Early
One of the most effective ways to prevent resource constraints is by identifying potential bottlenecks before they arise. By regularly monitoring processes and assessing each area of production, service delivery, and resource utilization, you can pinpoint weaknesses in your system. These weaknesses could include equipment failures, staffing shortages, or supply chain disruptions.
To address these challenges, develop contingency plans and incorporate flexibility into your capacity strategy. For example, having backup suppliers or multiple shift options for employees can help you stay agile when bottlenecks occur.
- Use Technology and Tools to Streamline Planning
Modern capacity planning relies heavily on technology. Utilizing software tools for resource management, scheduling, and forecasting can significantly improve the precision of your plans. These tools help analyze data, track resource usage, and make real-time adjustments as necessary.
Tools such as Enterprise Resource Planning (ERP) systems, data analytics platforms, and forecasting software can automate many aspects of the planning process. By implementing these solutions, you can optimize resource allocation, reduce manual errors, and gain insights into areas where capacity might be underutilized or overstretched.
- Regularly Review and Update Your Plans
Capacity planning is not a one-time activity but a dynamic process that requires constant monitoring and adjustment. Regularly reviewing your capacity plan ensures that it stays relevant and effective as business needs evolve. This practice allows you to adapt to unexpected changes—whether that’s a sudden increase in demand or a disruption in the supply chain.
Make it a routine to evaluate your capacity plan against actual performance. Are you hitting your targets for resource utilization and output? If not, analyze why and adjust your plan accordingly. By doing so, you’ll continuously improve your operations and reduce the risk of capacity mismatches.
- Build Flexibility into Your Plans
In today’s unpredictable business environment, flexibility is essential. Rigid capacity planning can lead to inefficiencies and missed opportunities. Build flexibility into your capacity plans by incorporating scalability options that can be adjusted as needed.
For example, having the option to scale up or down your workforce or production capacity quickly is invaluable. This flexibility allows your business to respond to demand fluctuations and avoid the pitfalls of overcommitting resources or losing out on sales.
- Involve All Stakeholders in the Planning Process
Capacity planning is not an isolated task—it should involve input from multiple departments and stakeholders across the business. Whether it’s the operations team, HR, or finance, each department can provide valuable insights that will help improve the accuracy and effectiveness of your plans.
Collaborative planning also ensures that everyone is aligned and working toward the same goals. It helps identify resource constraints early and enables teams to address them before they impact performance.
- Balance Capacity and Resource Utilization
The goal of capacity planning is to match resources with demand efficiently, but it's equally important to avoid both underutilization and overutilization of resources. If your resources are consistently underutilized, you may be wasting money on unnecessary capacity. On the other hand, overutilizing your resources can lead to burnout, delays, and missed deadlines.
Implement a balanced approach to resource allocation, ensuring that your capacity utilization is optimal. This means scaling resources based on actual demand, rather than purely theoretical needs. Through precise monitoring, you can maintain this balance and maximize productivity without overwhelming your assets.
- Focus on Continuous Improvement
Continuous improvement should be at the heart of your capacity planning process. As with any aspect of business management, the goal is to learn from each iteration of your planning process and refine it for the future. Use the insights gained from previous capacity planning cycles to identify areas for improvement.
Incorporate feedback loops into your capacity planning process to ensure that you’re always striving for better outcomes. By focusing on continuous improvement, you ensure that your capacity planning remains adaptable and resilient in the face of changing market demands.
Success is built on practices, but INSIA.ai provides the platform to reach new heights.
How INSIA.ai Can Support Efficient Capacity Planning?
You know that accurate data is the foundation of effective capacity planning. Without it, you risk overspending or underperforming. INSIA.ai addresses this challenge by centralizing your data. It pulls information from diverse sources. This creates a single source of truth. You gain real-time insights into your operations. This is crucial for forecasting demand and aligning resources.
- Centralized Data for Real-Time Insights
INSIA.ai centralizes data from diverse sources. This provides a single, unified view. You can access real-time insights into your operations. This is essential for accurate demand forecasting. You can also align resources effectively.
- Customizable Dashboards for KPI Monitoring
INSIA's "Connect" module lets you create custom dashboards. These dashboards visualize key performance indicators. You can monitor utilization rates and lead times instantly. You can also track inventory turnover and resource efficiency. This helps you maintain operational control.
- Search-Driven Analysis for Demand Pattern Prediction
The “Analyze” module allows you to perform search-driven analysis. You can quickly find data related to demand patterns. This helps you predict future needs. You can make informed decisions based on accurate data.
- Predictive Analytics for Proactive Resource Adjustment
The "Push AI" feature offers predictive analytics. You can forecast demand with greater accuracy. You can anticipate fluctuations in your business. This helps you implement lead, lag, or match strategies. You can adjust your resources proactively.
- No-Code Interface for Accessibility
INSIA's no-code interface makes advanced analytics accessible. You do not need technical expertise. You can use the "Transform" module to manipulate data. This ensures your data is ready for analysis.
- Mobile Analytics for On-the-Go Monitoring
INSIA's mobile analytics ensures you have access to data on the go. You can monitor capacity utilization from any device. You can receive real-time updates. This allows you to respond quickly to changes. This is important during periods of high demand.
- Robust Security and Compliance
The platform’s robust security features ensure your data is protected. Role-based access control allows you to manage who sees what data. Automated backups safeguard your information.
- Client Success Stories: Real-World Impact
Without saying much, let’s look how we helped some of the clients - based on results:
- Consider the success of Trident Services. They improved report generation by 70%. They also automated reporting by 90%. This was achieved by consolidating data with INSIA.
- Kirloskar Oil Engines reduced reporting time by 70%. They streamlined data from various systems.
- Crescent Foundry reduced reporting costs by 40%. They improved time-to-insights by 50%.
- Alaric Enterprises reduced manual effort by 50%. They also reduced forecasting time by 60%.
These results demonstrate INSIA's impact on different industries.
Conclusion
You’ve learned that effective capacity planning balances resources with demand, optimizing operations and reducing costs. Now, imagine achieving this with precision.
INSIA.ai centralizes your data, offering real-time insights and predictive analytics. You can forecast demand accurately and adjust resources proactively. This platform empowers you to make data-driven decisions, eliminating guesswork. Client success stories prove its impact.